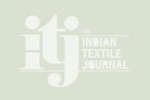
Improving fabric printing with Yamada AODD pumps
With the switch-over to AODD pump, Royal Classic Mills could get smooth printing, easier pump handling and less AMC. Uniform transfer of colours is critical to ensure excellent printing evenness. That’s where the colour paste pumps come in. However, the conventional process using gear pumps for colour transfer is beset with numerous problems including frequent pump breakdowns.
With the switch-over to AODD pump, Royal Classic Mills could get smooth printing, easier pump handling and less AMC.
Uniform transfer of colours is critical to ensure excellent printing evenness. That’s where the colour paste pumps come in. However, the conventional process using gear pumps for colour transfer is beset with numerous problems including frequent pump breakdowns. Yamada’s specially designed AODD pump for colour transfer is a perfect solution that not only improves the fabric printing quality, but saves printers from the frequent maintenance hassles! No wonder then that the Royal Classic Mills, a leading integrated textile player in Tirupur, Tamil Nadu, switched over to Yamada AODD pumps replacing the gear pumps for its printing machines. This mill is very happy with the long term benefits of using the Yamada AODD pumps.
Background
Royal Classic Mills is a Rs 900 crore company vertically integrated all the way to its retail outlets, Classic Polo, andits apparel brand Smash. Royal Classic deals with all kinds of textiles such as 100 per cent cotton, 100 per cent mercerized, poly cotton blended, cotton/rayon blended, linen/cotton blended, spandex, hydrotec, polyester, micro fabric, and premium knits.
Rotary screen printing
The rotary screen printing method involves the use of a separate rotary screen for each colour. The fabric passes under a rotating screen through which printing paste is pumped. A squeegee in each rotary screen forces the paste through the screen on to the fabric; the fabric then passes into a drying oven where it is cured to set the colour, before it is washed.
Challenges
The rotary printing machines at Royal Classic were equipped with gear pumps for colour transfer on to printing screens. Since these pumps are usually placed below ground level, they get frequently flooded with water flowing through channels, thus making them prone to failures. Other problems faced by the mill were frequent burning of motors due to contact with water, pump choking due to change in the viscosity of the paste, need for constant lubrication and maintenance, loss of production, improper fabric printing, and wastage of colour.
Solution
Having understood the requirement and the problems faced, A.T.E. suggested a solution with Yamada’s AODD pump to replace the existing conventional gear pumps. AODD pumps provide better transfer rates for colour. They operate on a pneumatic principle and hence do not require a motor. This eliminates the chances of motor failure due to water contact. Pastes of different viscosities are efficiently handled by this AODD pump without any choke-up. These pumps have few moving parts, and hence require lesser maintenance and no lubrication.
Result
With the switch over to AODD pump, Royal Classic Mills could gain the following benefits:
- •Smooth fabric printing – pump works smoothly without any choking
- •Easier pump handling – regular dismantling and reassembly not needed for AODD pumps
- •Less annual maintenance cost – these pumps do not have motors, and their few moving parts are quite sturdy
- •Saves fabric printing process time – no downtime due to pump failures
Looking at the clear benefits of the AODD pumps, Royal Classic is quite happy with its decision to stop using gear pumps. General Manager at the company appreciates the solution provided by A.T.E. and says “We found A.T.E. to be a very reliable flow technology solution provider. We are very happy for the solution provided with Yamada’s AODD pumps over gear pumps for transferring of colour on to screens, which is helping us in smooth fabric printing.â€
For further information:
A.T.E. Enterprises Private Limited
Tel: +91-20-3088 1100 | Email: flowtech@ateindia.com
Web: www.ategroup.com