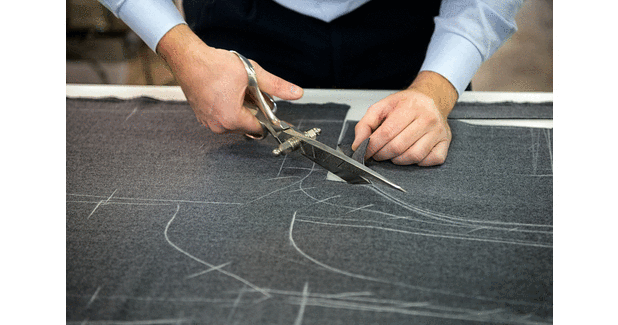
How to save time and cost in cutting room
By responding faster to make a product as per customer demand, the company can capitalise less money and more savings, say Rhea Sinha and Padma Priya.
By responding faster to make a product as per customer demand, the company can capitalise less money and more savings, say Rhea Sinha and Padma Priya.
The growing demand of apparels and the fast-changing fashion is creating a challenging atmosphere for the manufacturing units to complete the demand. Generally in an industry more focus is given on profit. Though there are different costs involved in cost reduction internally spent by an industry through finding wastages, avoiding and improving faulty work would end in vast reserves. Non productive activities designate that the customer does not ponder as adding value to his product. One of the ways to decrease wastages can be elimination of non-productive activities that can result in drop in time, cost, and lead time. As it is acknowledged that time is money, if additional time is mandatory in a product or service extra money is involved. By responding faster to make a product as per customer demand, the company can capitalise less money and more savings.
For any industry, cost and time related to production and quality management or wastages reductions have important impact on overall expenditure. Internal cost spent by an industry made by eliminating internal throughput time or redraft or any type of surpluses are important for management to keep the industry economically sound and safe. Emphasising on it steps has been taken to investigate and eliminate wastages, that is, non-productive activities in production process in order to save time and cost and lessen internal process time. The outcome of this observation would reflect that an industry may gain higher productivity and profitability by eliminating non value added activities.
Taiichi Ohno defines waste as: “Anything other than the minimum amount of equipment, materials, parts and working time absolutely essential to productionâ€. Chethan Kumar CS, NVR Naidu, illustrated the importance of using the lean principles to eliminate non value added wastes in garment industry. “a value stream is the sequence of activities an organisation undertakes to deliver on a customer request.†(Martin and Osterling, 2013).Martin and Osterling summarised the benefits of value stream mapping. In the work of Rother and Shook (2003).provided the first way to “see†the value streams that Womack et al. introduced. In the study conducted by Hines and Rich (1997), seven new tools were presented regarding the seven wastes.
Based on the analysis of the existing system at X Exports Pvt Ltd and studies done, the industry plans to improve production rate with less wastages. Generally these wastes are overproduction, correction (rework), transportation, waiting and inventory of the manufacturing product where it ploy to increase the productivity of the industries alongside it tries to reduce the wastages of the manufacturing and lead time to manufacture the products.
Objective
Methodology
Process study
This process study includes time study and method study. A through time study of each operation such as has been a complete hand movement of the operator is done with time to find out the non-value added activities through a method study.
Identify waste: The wastes are identified, which creates hindrance in production with the time through non-value adding (NVA), necessary but non-value adding (NNVA), value adding (VA). Total Time involved in all the activities: 836.48 minutes.
Identify the problems: The problems should be identified and studied so that solutions can be suggested
Inventory-related issues
Waiting in cutting room, high inventory in cutting room, WIP kept in aisle space resulting in higher transportation time, trolleys filled with rolls left for waiting in aisle space and hindrance in trolley movement.
Shrinkage sticker is put on fabric rolls manually:
Fabric rolls are stored on the spreading table:
Different width of the fabric used in lay
Fabric rolls are opened before spreading
Three people involved in spreading and cutting process
The third operator was not fully utilised during the process. For cutting, two people are sufficient as one will cut and the other would tie the bundles and the same person will carry the bundle for the next operation. In this way the third operator will be utilised in other group.
No prior allocation of table
Shifting of lay from one table to another
Prespreading
Per minute cost of the company: Rs 3.26 Cost saved from eliminated activities 31.39 x 3.26 = Rs 102.33 Per month (30 days) salary of one manpower (semi-skilled worker) = Rs 7,980 30 days = 240 working hours at eight hour per day = 14,400 minutes Per minute salary of one manpower = Rs 0.55 Salary saved from eliminated minutes (22.41 minutes) = Rs 12.32 So, salary saved from two manpower = Rs 24.65 Cost saved from the pre-spreading process = Rs 126.98
Spreading
Cost saved from eliminated activities 15.08 x 3.26= Rs 49.16 Per month (30 days) salary of one manpower (skilled worker) = Rs 12,500 30 days = 240 working hours at eight hour per day = 14,400 mins Per minute salary of 1 manpower = Rs 0.87 Salary saved from working minutes (2:11.37 minutes) = Rs 114.29 Cost saved from the spreading process = Rs 163.45
Cutting
Cost saved from eliminated activities 47.23 x 3.26 = Rs 153.96
Per month (30 days) salary of one manpower (skilled worker) = Rs 12,500 30 days = 240 working hours at eight hour per day = 14,400 mins Per minute salary of 1 manpower = Rs 0.87 Salary saved from working minutes (21.54 minutes) = Rs 18.74 Cost saved from the Cutting process = Rs 172.70
Pre-fusing
Re arranged (These activities to be carried out simultaneously with the fabric spreading process and not after the cut blocks are received Fusing paper spreading (1:50.41) Fusing Paper cut according to the requirement (4.48) Fusing machine setting (5.04) Time saved: 2:0.33 Cost saved from pre-fusing process 120.33 x 3.26 = Rs 392.27
Ticketing of blocks
Combined process (Storage of the parts after receiving the bundles from cutting is not done and the process happening after fusing was combined)
Fusing
Recutting
Auditing
Conclusion
This study is an attempt to improve the process flow and reduce the non-value added activity’s time in cutting department. The number of non-value added activities in cutting room is reduced to 8 from 19 after the implementation and travelling distance per lay is reduced to 148 m from 252 m. This study also shows the improvement in the process reduced time and manpower and save cost of the company. The total time saved from one lay in cutting room is 235 minutes and the total manpower saved from one lay in cutting room is four then the total cost saved from one lay in cutting room is Rs 922.52.
References
Rhea Sinha is Student, Department of Fashion Technology, National Institute of Fashion Technology, Chennai. She can be contacted at: Email: sinharhea28@gmail.comPadma Priya is Assistant Professor with the Department of Fashion Technology, National Institute of Fashion Technology, Chennai. She can be contacted on: Email: padmapriya.m@nift.ac.in