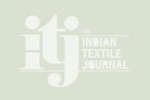
Hard waste control in automatic cone winding
Ensuring a high cop content for a given package size and avoiding use of damaged cops in ring frames are a few of the some important measures needed to control hard waste in automatic cone winding,
Ensuring a high cop content for a given package size and avoiding use of damaged cops in ring frames are a few of the some important measures needed to control hard waste in automatic cone winding, emphasise D Shanmuganandam and J Sreenivasan.
Waste management is always a serious issue for many spinning mills. Though generation of wastes during fibre to yarn conversion process is inevitable, nevertheless, when it exceeds the stipulated level, it would result in a monetary loss to mills. Therefore, every effort must be made to optimise the generation of various types of wastes. At the same time, mills should try to fetch a maximum possible sale value for wastes in order to minimise loss due to generation of wastes.
The extent of generation of various types of wastes depends upon a number of factors such as quality of raw material, yarn quality requirement, type of machinery and their condition and work methods of operatives. Nevertheless, their incidence could be controlled to a maximum extent without affecting the machine productivity and yarn quality, by exercising a good control over the process, maintenance of machines, workers efficiency, etc.
The following wastes are being generated by the cotton spinning mills:
- Saleable wastes: Blow room droppings, licker-in droppings, flat strips, comber waste (noil), hard (yarn) waste, sweep waste, fan/suction wastes and gutter/filter waste.
- Useable wastes: Lap bits, sliver bits, roving ends, pneumafil waste and roller wastes.
Except hard waste, incidence of other wastes happens at different stages of yarn manufacturing. The hard waste occurs mostly at the final stage, ie, in post spinning process which means that it carries almost entire conversion cost besides raw material cost. Considering the fact that the price fetched for the hard waste is only about 25 per cent of yarn selling price, any quantity of hard waste more than that normally permitted would result in a significant financial loss to a mill.
This article covers hard waste particulars pertaining to automatic cone winding as well as the price realised for hard waste that were furnished by the mills in the 29th CPQ (Costs, Operational Performance and Yarn Quality) study covering April – June 2013 data. Measures to reduce hard waste are also included in the article.
Hard waste
The hard waste (%) data pertaining to automatic cone winding have been compiled for some popular counts and given in Table 1. Data relating to three important process parameters in automatic cone winding, viz, clearer cuts, cop rejection, and repeaters, which have a detrimental effect on the incidence of hard waste, are also given in Table 1.
The following observations have been made on the data given in Table 1.
Average hard waste in automatic cone winding with round magazine cop feed was high at 0.68 per cent which is more than 2 times the SITRA standard of 0.30 per cent. Between counts, the average waste level ranged from 0.60 to 0.80 per cent.
Between mills, the incidence of hard waste showed a mindboggling variation of 2 to 5 times in various counts.
Major reasons for the high hard waste are discussed below:
Inadequate maintenance of machinery
Poor maintenance and upkeep of ring frames would result in vibrating spindles, spindles out of centre, soft cops, improperly built cop bottom, etc, all of which have a detrimental effect on clearer cuts, slough off and cop rejection in automatic cone winders which in turn would increase the hard waste. Inadequate maintenance of automatic cone winders would also affect the pr