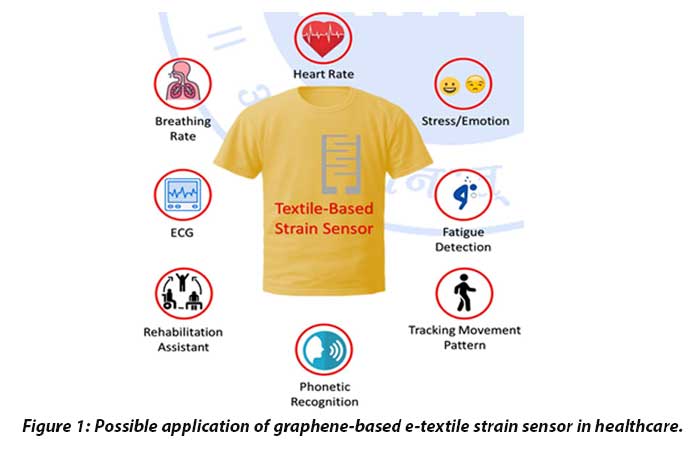
Graphene-based e-Textile strain sensor for monitoring health
Achieving graphene-coated fabrics with both strong interfacial strength and washability remains a challenge, informs Partha Bairi and Tanmoy Gangopadhyay
Electronics textiles, or e-textiles, are textiles integrated with electronic components such as sensors, actuators, conductive thread, energy storage, energy harvesting devices, and microcontrollers. Third-generation e-textiles represent a significant advancement, wherein the textile itself serves as an electronic component or device. Third-generation e-textiles offer several advantages over first and second-generation counterparts, where separate electronics devices are either attached to or embedded within the garments. Third-generation e-textiles boast properties such as lightweight, high flexibility, air permeability, improved performance, and a high degree of freedom for integration into garments. Moreover, they significantly broaden the scope of applications in various fields. To develop third-generation e-textiles, the first step is to introduce electrical conductivity to non-conductive fabric. Then, various functionalities can be incorporated into the fabric to suit specific applications. However, challenges remain, particularly in ensuring that conductive fabrics are washable, biocompatible, suitable for mass production, cost-effective, and aesthetically pleasing. Despite these challenges, third- generation e-textiles hold enormous potential in diverse fields such as healthcare, energy storage and harvesting, sensors, and electronics.
E-Textile Strain Sensor
In this article, we will focus on fabric-based strain sensors or e-textile strain sensors and their potential applications in the healthcare industry. A strain sensor is capable of detecting the deformation or displacement of an object due to applied stress, which alters its electrical properties, such as electrical resistance. In healthcare, strain sensors can be utilised for monitoring vital signs like heart rate, breath rate, facial expression, pulse, and human motion (Figure 1). Beyond healthcare, these sensors find applications in sports, defence, robotics, security systems, structural health monitoring, entertainment, and transportation. Consequently, there is significant demand for third-generation textile-based strain sensors in both industry and society. E-textiles and strain sensors hold substantial future market potential, with the projected global market value for e-textiles and smart clothing reaching approximately $ 15 billion by 2028 and $ 2.5 billion for strain sensors by 2029, respectively. Conventional semiconductors like silicon and metal-based strain sensors are unsuitable for wearable technology due to their rigidity, low sensitivity (gauge factor), low resolution, higher cost, and high density. Wearable strain sensors must possess specific characteristics such as high flexibility, sensitivity, wide range of working strains, linear response, elasticity, good electrical conductivity, low hysteresis, biocompatibility, and durability. However, producing suitable textile-based strain sensors fulfilling all these criteria for e-textile applications is extremely challenging.
Role of graphene in E-Textile Strain Sensor
Recently, graphene-based strain sensors have emerged as promising candidates for e-textile systems. Graphene, a two-dimensional single- layer sp2-hybridized carbon framework, exhibits exceptional physical and chemical properties. Its electrical conductivity can reach up to 108 S/m, and thermal conductivity can reach 5150 W/mK. With an extraordinarily high Young’s modulus of approximately 1 TPa and tensile strength of around 130 GPa, graphene can sustain up to 25 per cent in-plane tensile elastic strains, whereas silicon typically breaks at strains of around 1.5 per cent. Graphene exhibits excellent piezo-resistive properties. The likelihood of alterations in the electrical properties due to changes in the electronic band structure increases when a strain induces considerable elongation in graphene. Consequently, a noticeable coupling between the electrical and mechanical characteristics of graphene is expected to occur. Moreover, graphene has many structural varieties that aid in the surface modification of textile fabrics and fibers through covalent bonding, facilitating the development of washable and stable e-textiles.
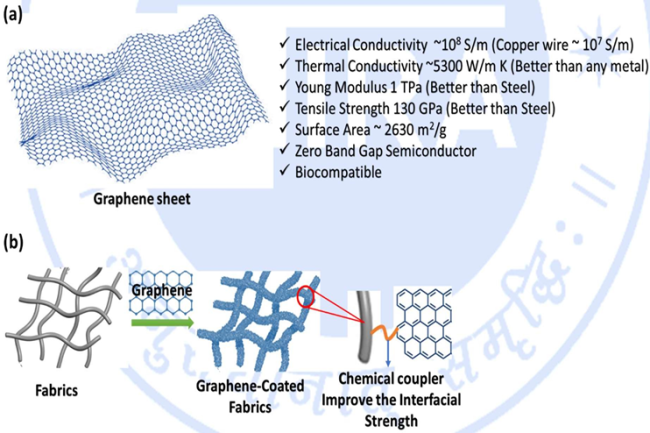
Figure 2: (a) Schematic image of graphene sheet and its promising properties and (b) Schematic presentation of the graphene-coated fabrics and possible method for improving interfacial strength between graphene and fabrics to developed washable third generation e-textile
Recent development of E-Textile at ATIRA
Nevertheless, achieving graphene-coated fabrics with both strong interfacial strength and washability remains a challenge. This limitation hinders the long-term usability and practical application of graphene-modified textile-based strain sensors. By integrating graphene into suitable fabrics or yarns with robust interfacial strength, it becomes feasible to create wearable strain sensors capable of effectively monitoring slight deformations resulting from bodily functions such as pulse, respiration, facial expressions, and speech. In response to this challenge, ATIRA has developed graphene- modified various washable fabrics, fibres, and yarns with manipulable and high electrical conductivity. These advancements have led to the creation of graphene-modified fabric- based strain sensors with a high gauge factor, capable of operating across a wide range of strains from 0 to 200 per cent. Currently, efforts are also underway to develop graphene-coated fabrics for fatigue detection and electromagnetic interference (EMI) shielding applications. The developed graphene-modified fabrics offer numerous potential functionalities, including antimicrobial properties, thermal heating and cooling capabilities, biochemical sensing abilities, materials for human-machine interface, energy harvesting and storage for self- sustainable e-textiles, body temperature monitoring, smart gloves, and various other wearable technologies.
Future development
Product realisation of third generation e-textile is very challenging especially wearable products. There are various opportunity to develop new third-generation e-textile-based wearable products with potential applications. Therefore, ATIRA is actively seeking collaborators and partners from academia and industry to engage in joint development of a specific e-textile product for healthcare, technology transfer, as well as collaborative high-quality research in this cutting-edge field.
References
- A. Libanori, et. al., Smart Textiles for Personalized Healthcare, Nature Electronics, 2022, 5, 142
- R. F. Service, Electronic Textiles Charge Ahead, Science, 2003, 301, 5635
- M. Dulal, et. al., Toward Sustainable Wearable Electronic Textiles, ACS Nano, 2022, 16, 19755
- S. Bhattacharjee, et. al., Graphene Modified Multifunctional Personal Protective Clothing, Advanced Materials Interfaces, 2019, 1900622
- L. Wang, et. al., Application Challenges in Fiber and Textile Electronics, Adv. Mater. 2019, 1901971
About the author:
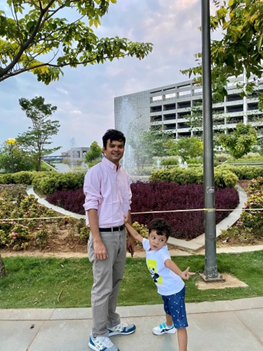
Dr Partha Bairi is a Senior Scientific Officer at Ahmedabad Textile Industry’s Research Association (ATIRA), India. He previously worked at Shinshu University & NIMS in Japan, NTU in Singapore, and Jadavpur University in India. He holds MSc in Chemistry from IIT Madras and PhD in Polymer Science from IACS/Jadavpur University.
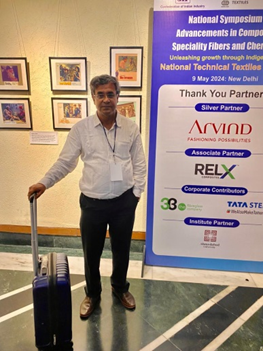
Dr Tanmoy Gangopadhyay is a Deputy Director at Ahmedabad Textile Industry’s Research Association (ATIRA) since 2015. He has 28 years of work experience in industry including 17 years in Reliance Industries. He holds M.Tech and PhD in Plastics & Rubber Technology from the University of Calcutta.