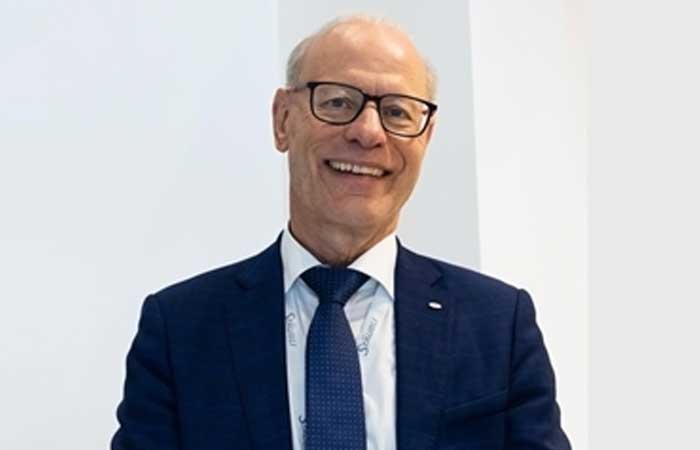
Fritz Legler: Automation ensures the production of quality materials at reduced time and cost
Stäubli provides technological solutions with four dedicated Divisions: Electrical Connectors, Fluid Connectors, Robotics and Textile. They serve customers who want to increase their productivity in many industrial sectors worldwide.Fritz Legler, Global Head of Marketing and Sales WPS for Textiles and Textile Divisional Marketing Officer, Staubli AG, Switzerland, discusses with Divya Shetty the significance of integrating automation in the textile machinery industry and how his company is implementing it.
Given the current uncertainty of the Indian textile industry and global industry in general, how can automation help mitigate this challenge?
The global textile industry, including India, faces multiple supply chain challenges. Irregular market demands make it difficult for weaving mills to maintain stable fabric production year-round. Rising energy prices and per-unit costs, along with increasing raw material prices, exacerbate these issues. Consequently, Indian weaving mills struggle with limited productivity, inefficiencies, and reduced manpower, hindering their ability to meet market demands. From weaving preparation, frame and Jacquard weaving, to carpet and technical weaving, Stäubli offers innovative machinery systems and solutions that ensure precise and high-quality textile production. These machines help weavers improve workflows and control production costs, enabling them to stay competitive in the textile market.
How does automation help in increasing the productivity and reducing the losses? How is your company benefitting with the automation?
Automation ensures the production of quality materials at reduced time and cost due to its adaptation that makes machines function in line with the users’ needs. At Stäubli, our expertise revolves around easing the challenges of every customer. By inserting automation in our solutions, our customers have been able to reduce operational costs by minimizing errors and waste. Our SAFIR PRO automatic drawing-in machines provide our clients with very high and error-free drawing-in rates, quick and easy style changes without tampering with the quality of their products. Thanks to the TIEPRO warp-tying machines quality warp beams and perfectly tied warp threads are achieved ensuring improved and reduced manual operations during the weaving process.
What challenges exist in integrating automation into textile manufacturing? Do challenges such as a shortage of skilled labour, MSMS’s limited expenditure, and rising plant maintenance costs contribute to the challenges?
Integrating automation into textile manufacturing presents several challenges, including high initial investments, technical complexity, and the need for customization and adaptability of new machines. The rising demand to reduce production costs in all areas contributes to these challenges. Therefore, weaving mills should invest in reliable and operator-friendly machines like Stäubli TIEPRO warp-tying machines, which help reduce costs and achieve long-term objectives. The TIEPRO offers fast and efficient warp tying with minimal operator intervention, making it ideal for manufacturers facing a shortage of skilled labor.
How is Industry 4.0 (like AI, IoT networks, robotics, etc.) changing the landscape of textile manufacturing?
Industry 4.0 is an advanced technology that responds to the present demands of textile manufacturing. This advancement is game changer as we can now manufacture efficient, durable and intelligent weaving machines granting easy access to optimized yarn handling, real-time data analysis and predictive maintenance of machines. The MyStäubli customer portal is equipped with Industry 4.0 solutions that provide customers with these advantages. Customers have easy access to maintenance records, training materials, and support services, ensuring effective equipment management and minimized downtime. Thank to this, rising challenges in the textile manufacturing sectors can be easily addressed at an optimal rate.
Lastly, what are the future trends in automation in textile industry?
Automation in the textile industry is fast advancing with multiple trends such as AI-driven weaving systems, and sustainable manufacturing of textiles. AI powered systems allow for real-time consumer data analysis, predictive maintenance, as well as trends prediction and preferences, enabling manufacturers to produce customized and personalized products more cost-efficiently. Stäubli has set a new generation yarn management standard with its SAFIR PRO automatic drawing-in machines. Equipped with Active Warp Control 2.0, they ensure optical, non-contact recognition and measurement of yarn properties to produce innovative, outstanding and unique designs. These advancements will contribute to the improved manufacturing of high-quality fabrics and the easy maintenance of machines, both of which are crucial for the future that the textile industry aims to achieve.
NEWS SNIPPET
Technosport unveils Duracool+ Technology with KARL MAYER & A.T.E. at open house
Technosport, a leading Indian activewear brand, recently hosted a successful open house event at its Perundurai mega-facility in collaboration with Karl Mayer and A.T.E. TechnoSport is committed to delivering high-quality, accessible apparel while prioritising sustainability and global recognition. To further this mission and expand its market reach, Technosport has recently invested in cutting-edge Karl Mayer HKS-3M Tricot warp knitting machines.
Karl Mayer is proud to recognise Technosport as the first customer in South India to leverage tricot machines for active and sportswear production. Over 100 industry professionals from Tirupur, Erode, Coimbatore, and other regions attended the event
Attendees witnessed live demonstrations of three HKS 3M machines, coupled with a DS-Warper, showcasing the production of specialised warp-knitted fabrics for active and sportswear. The event featured a welcome address by Navin Agrawal from A.T.E., followed by an insightful presentation on warp knitting technology by Mark Smith. Franseska Guth and the A.T.E. sales team further engaged the audience with displays of warp-knitted fabric samples and finished garments.
The open house culminated in a dynamic demonstration of all three machines operating at speeds up to 2800, producing fabrics for activewear.
Talking about the significance of the event, Sunil Jhunjhunwala, Co-founder of Technosport commented, “We are very proud to partner with Karl Mayer and bring such technology to India. Given the growing demand for synthetic materials in both domestic and export markets, we expect interest in warp knitting technology to gain significant momentum in the next few years. By partnering with A.T.E. and Karl Mayer and hosting such events, we hope to further solidify that interest.”
This strategic partnership with Karl Mayer Germany has enabled Technosport to launch its innovative ‘DuraCool+’ warp-knitting technology, utilising Karl Mayer HKS-3M machines. Building on this advancement, Technosport plans to introduce versatile, functional, and durable all-day pants, combining the robustness of woven trousers with the comfort and flexibility of knitwear.
Mark Smith, Deputy Vice President of Karl Mayer stated, “We extend our sincere appreciation to Sunil Jhunjhunwala and the entire Technosport team for their invaluable support in making this Open House a resounding success. We also commend the A.T.E. Coimbatore team for their dedicated efforts in organising and executing this impactful event. We hope to conduct more such events in the future to expand warp knitting capabilities in India”
By embracing cutting-edge technology and focusing on sustainability, Technosport is poised to redefine the standards of activewear globally. As the brand continues to expand its market reach and product offerings, it remains committed to making high-quality sportswear accessible to everyone, inspiring a healthier and more active lifestyle for all.