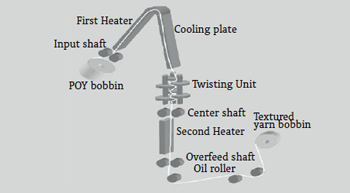
Effect of D/Y ratio on draw texturing yarn
During texturing, with the increase of D/Y ratio, yarn denier and tenacity decrease while the breaking strain increases, find Dhavale AJ and Sarda NR. Texturing is the process of imparting the comfort characteristics such as voluminousness, luxuriousness, bulkiness, good dimensional stability, etc.
During texturing, with the increase of D/Y ratio, yarn denier and tenacity decrease while the breaking strain increases, find Dhavale AJ and Sarda NR.
Texturing is the process of imparting the comfort characteristics such as voluminousness, luxuriousness, bulkiness, good dimensional stability, etc., into the continuous filament yarns by introducing permanent waviness, loopiness and curliness.
Texturing of filament yarns
One of the main disadvantages of man-made fibres is the flat geometry and smooth surface. The fibre waviness or crimp increases volume, resilience, moisture absorption, etc. Texturing methods have been developed to overcome this problem.
I. False twist texturing
II. Air texturing process
False twist texturing is the most widely used technique, in which the filament yarn is twisted, heat-set and untwisted to produce crimped yarns. False-twist texturing method is the most common process. False-twist texturing process can be investigated based on three main parameters, which are called 3t: tension, twist, and temperature. The properties of the textured yarn can be altered by changing these parameters. Draw ratio, D/Y ratio, and heater temperatures are the main process parameters to change 3t. The ratio of the disk surface speed to the yarn speed is usually referred to as D/Y ratio. D/Y ratio is calculated as follows:
D/Y = Circumferential speed of disks (m/min)
Throughput speed of yarn (m/min)
If D/Y ratio is low, the yarn tension before twisting unit will be low and the tension after the twisting unit will be high. This situation can cause yarn damages. Draw ratio is the ratio of centre shaft speed to the input shaft speed and is calculated as follows:
Draw ratio = Center shaft speed (m/min)
Input shaft speed (m/min)
Polyester fibre use is growing very rapidly because consumers prefer silk-like, soft, light, drapeable fabrics. For this purpose, a considerable amount of work is being done to modify the existing polyester fibre.
Figure 1
Advancements in spinning (extrusion) technology and improvements in the quality of polymers has made it possible to reduce the denier per filament (dpf) to less than 1.0 to achieve the fineness of natural silk, its soft feel, and its lustre. Microfibre polyester fibres have given a new dimension to fashion, offering consumers innovative fabrics. The fibres are being textured to overcome deficiencies in bulk and handle associated with flat filament fabrics. Texturing microfibre polyester yarn is a challenge because of the many problems faced during the process.
Subhas Ghosh and John Wolhar observed that the resultant properties of the textured yarns are determined by the interaction effects of more than one process variable. Heater temperature, disc spacing, and draw ratio showed considerable influence on the yarn properties in the friction-twist-texturing process. The effects of D/Y ratio on the yarn properties, while significant, were not as pronounced.
Figure 2 shows the effect of draw ratio and D/Y ratio on crimp contraction. Yarn crimp contraction has decreased by approximately 6 per cent for the range of draw ratios studied. The effect of D/Y ratio on crimp contraction showed very little physical significance, even though the effect was statistically significant.
Kenan Yildirim PhD, Sule Altun PhD, Yusuf Ulcay PhD2 studied the effects of draw ratio and D/Y ratio on some properties of the false twist textured PET yarn were studied. Draw ratio and D/Y ratio, together w