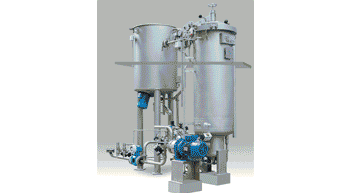
Ecology & energy factors hold sway in processing
Energy saving, ecology protection and effluent reduction are very much at the heart of the changes happening in the dyeing and processing industry
Energy saving, ecology protection and effluent reduction are very much at the heart of the changes happening in the dyeing and processing industry. Joseph S paints a picture of the emerging scenario against a background of some recent innovations.
Dyeing and other processing segments in the textile industry have undergone a sea change since the last two decades. Today, the eco concerns have virtually gripped the textile industry, which has been named one of the worst polluters among various industries. The Three Es—Effluent Control, Ecological Protection & Energy Reduction—are playing a greater role, and this was very much evident during the recently-concluded ITMA 2015 at Milan in Italy.
In textile processing, the amount of energy spent to dry the fabric and unspent dyestuffs remaining in liquor are also huge adding to the woes of processors, making processing the weakest link among the entire textile chain. Textile wet processing consumes huge amounts of energy. The present-day scenario in the textile processing calls for the conservation of energy or usage of low amount of energy.
There was a great deal of interest at the ITMA 2015 for sustainable and energy-saving products. For instance, BRÜCKNER offered beside the new and efficient stenter concept POWER-FRAME ECOLINE mainly innovations in the field of coating technology. It presented the new application unit ECO-COAT, which has been developed particularly for minimum applications. This unit allows impregnations as well as applications on one and on both sides of the fabric. The minimum application quantities require in the following drying processes clearly less water evaporation which has a positive effect on the energy requirement at the respective dryer.
Besides, the new software tool ECO-MATIC, which was enthusiastically received by the customers, supports the user and leads to a more efficient handling of the machine and the resources. The result of the optimisation shows in a significant saving of resources and cost. This software functions not only in new machines and leads to a clearly better understanding of the relation between machine technology and finishing process by the users.
Buyers of dyeing and processing industry today have understood that in most cases the investment in high-quality machines turns out to be profitable because the consumption of energy and spare parts as well as the maintenance over the lifetime of the product are clearly lower. It was sometime in the middle of 2015 EURATEX, the European textile and apparel confederation, and VDMA Textile Machinery signed a MoU to join efforts in the campaign “Energy Made to Measureâ€. It is focussed to strengthen synergy effects, in order to increase energy efficiency in small and medium enterprises of the textile and apparel industry. Regina Brückner, the owner of Germany’s Bruckner, said, “Sustainable development has become a competitive factor. On account of the volatile prices for commodities and energy as well as the increasing responsibility for work safety and workplace design the textile industry pays highest attention to all aspects of sustainability. For these reasons resource efficiency is one of the premium targets of technical development.â€
Speaking on Ecological concerns and ETP concepts, S Rajendran, VP (Textile Engineering, Processing, ETP & Utilities) of Mumbai-based A.T.E. Enterprises Pvt Ltd, “First of all, ETP needs were not taken care of by the textile industry in the past. In the south because of compulsion and rules, the industry towed the line. But what I see as a trend happening across India is the growing awareness for effluent treatment. A.T.E. Group always has been at the forefront of eco concerns and effluent treatment. We have a separate division, Envirotech Pvt Ltd, which already has ove