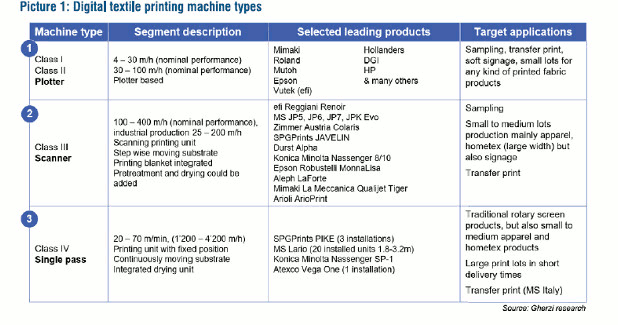
Digital printing market in upswing
Gherzi Consulting Engineers has identified four different fields of totally 37 indirect cost parameters, influencing the digital textile printing activities related to: sustainability, speed, flexibility and new business models.
Gherzi Consulting Engineers has identified four different fields of totally 37 indirect cost parameters, influencing the digital textile printing activities related to: sustainability, speed, flexibility and new business models.
Digital textile printing equipment is available since more than 20 years. Today it is the fastest growing segment within textile machinery. Gherzi conducted a global study to identify the main reasons for investments into digital textile printing. The growth still is not driven by direct cost advantages (against traditional textile printing technologies), but by several indirect parameters underlining the advantages of digital textile printing such as: a) speed to market b) design flexibility and c) new business models. Further increase of market penetration will also lower direct printing costs and therefore continuously increase the share of digital within textile printing (today ca. 3 per cent volume vise).
Digital textile printing equipment
Digital textile printing equipment can be segmented into three different types of machines:
- Type 1 – plotter type machines: Based on digital printing equipment originally designed for graphical application. In the field of textiles, they are used for sampling, for transfer print, for soft signage and small lots of any kind of printed fabric products. Production speed is limited, applied inks could be dye-based inks (reactive, acid, disperse) but also pigment based inks.
- Type 2 – scanner type machines: Equipped with a printing blanket. It is the most important machine type for textile applications so far, used for sampling, small to medium production lots mainly for apparel and hometex products (widths are available up to 320 cm) and also soft signage. Within industrially printed textiles, it is the most spread machine type.
- Type 3 – single pass type machines: This is the latest type of textile printing equipment, which allows (for the first time) production speeds in the range of traditional rotary screen printing equipment. That’s a first important comparison parameter to fuel a substitution of traditional textile printing technologies.
Substrates are moved continuously, the position of the print-heads (grouped in printing bars) is stable. Print quality to be achieved is always depending on the successful combination of substrate, pre-treatment, design, colour coverage, ink, print-head, machine, post-treatment and process speed.
Pre- and post-treatment
Successful digital textile printing still asks for an industrial environment with access to wet- and dry finishing equipment for the pre- and post-treatment. Processes cannot yet be standardised since treatments depend on type of substrates, type of inks, print penetration and type use of the final product. The importance of an adequate pre- and post-treatment and its influence on the print quality is often under estimated by involved parties.
Inks
Dye based inks dominate digital printing for textile applications, however a pre- and post-treatment is always requested.
Print-heads
Currently, Kyocera is the most spread print-head for scanner and single pass type digital textile printing machines. For none of the print-head suppliers, digital textile printing is the key focus of their business activities. Product leadership is fast changing with each new generation of print-head offered for digital textile printing.
Print-heads are perceived as one of the most critical component in a digital textile printing machine. The printing performance of a machine depends on the number of print-heads installed. Lifespan of a print-head is depending on the quality and type of ink in use, by the printing machine itself (especially electronics) and the physical construction of the head itself (multiple thin metal layers or solid silicone block). Even with most suitable inks life span of print-heads currently is between one and two years what results in an elevated maintenance and replacing cost. The print quality of a print-head is changing over its lifetime what challenges the print lot allocation to machines in a digital textile printing mill (that’s at least the experience of printers having thin layer heads like Epson or Kyocera in use).
Reliability of print-heads is one of the major requests for future improvements in digital textile printing. Machine manufacturers are aware of this issue and partly offer support to their clients to share the risk of failure.
Print cost calculation
Taking into consideration the pure print cost, digital textile printing in most cases is more expensive than traditional textile printing. The real cost advantage is limited to the fact, that with digital textile printing no screens are needed. Since for every colour in use, one screen is needed with traditional textile printing, more colours are used, more attractive the digital printing is in direct comparison with traditional.
With an example of a printed 100 per cent co substrate, rotary screen printing has cost advantage, the cost structure of digital does not differ strongly in the analysed geographical markets. In addition to the number of colours in use, the batch length to be printed is the second cost parameter to be taken into consideration for a direct cost comparison of digital textile printing with rotary screen printing. Following example shows the classical break even calculation.
The graph shows that the break even for a one colour print is at about 200 m, for a two colour print at about 700 m, for a three colour print at about 1,200 m and for a four colour print at about 2,000 m. Obviously, that’s not the only driver in favour of digital textile printing. More important are other parameters identified by Gherzi, which are difficult to quantify directly in monetary values but there is a direct correlation with the demand of digital textile printing.
Indirect cost
Gherzi has identified four different fields of totally 37 indirect cost parameters, influencing the digital textile printing activities related to: sustainability, speed, flexibility and new business models. Gherzi positioned the parameters in a grid with the relative awareness of textile printing companies against the relative impact on total cost of ownership.
- Sustainability: At textile printers, sustainability issues are not perceived as the main driver criteria for digital textile printing with the exception of low dye consumption and the reduced waste of printed fabric. However, facts as reduced freshwater consumption and wastewater charge, reduced consumption of chemicals and reduced consumption of energy compared to classical textile printing technologies are a fact even if carbon footprint and green image are no issue for the majority of textile printers (at least in combination with digital textile printing).
- Speed: peed related parameters are the main positive drivers in favour of digital textile printing. The advantage of no need for screens results in shortened lead times from defined design to printed fabric. A style installation on machine is basically a software issue since a graphic file is fed directly to the printing machine. Sampling activities could be accelerated, further the quality of printed samples are equal to the production quality as long as it is printed on the same type of machine. The ongoing trend for fast fashion in combination with more collections and shorter lots also favor the digital textile printing technology.
- Flexibility: Digital textile printing is a very flexible production process. It allows more collections, more colours, more design features (even different ones than traditional textile printing) and very easy colour variations. Warehousing became nearly unnecessary. Production quality can be expected similar to sample quality. Further the production even of short lots became much more attractive.
- New business models: The digital textile printing technology itself offers the potential of a variety of new business models. The direct interaction via web opens new possibilities of communication and interaction between involved parties (brands, designers, retail, printers, consumers), the single pass machines further allow unique opportunities of large production lots in very short time after order.
Single pass digital textile printing
With the market introduction of the Lario in 2012, MS Italy presented for the first time a digital textile printing machine offering similar production performance as a traditional rotary screen printing machine. In the meantime, beside MS Italy also SPGPrints (PIKE), Konica Minolta (Nassenger SP-1) and Atexco (Vega One) have sold and installed single pass digital textile printing machines in the industry.
The market for this type of equipment is limited so far since an interested investor has to rely on an industrial environment (pre-treatment and finishing equipment) and has to have an annual production volume of more than 2 million running m to be produced on the single pass machine. In theory, there are many potential customers around the world however main challenge for them is that they simply don’t know how to sell the added value of digital, thus cannot achieve a volume of minimum 2 million m that are necessary to justify the investment in single pass. A single pass digital textile printing machine has to be operated 24/7 in order to be profitable.
Advantages
- Capability to produce important quantities in a very short time (lead time advantage)
- Fast style change (design, colours) with nearly no installation time
- Production speed as rotary screen printing
- Nearly unlimited flexibility
Disadvantages
- Limited market so far
- Fast developing technology
- Heavy investment
- Lifespan of print-heads
- Quantity of suitable orders to fill capacity
- Industrial environment (pre- and after-treatment necessary)
Unique opportunities are offered by this type of machinery in terms of reaction speed and the potential to produce large quantities in very short time. Style changes can be prepared while the machine is still producing. There are nearly no limitations in quantities of colours and complexity of designs. Once the technology is mature, production cost are further lowered and the reliability of print-heads is given (what is a question of time) there is the potential to replace an important part of installed rotary screen printing capacity.
Pigment inks
As of today, digital textile printing with dye-based inks ask for an industrial environment with highly sophisticated pre- and after-treatment equipment. This fact limits the spread of machines towards garmenting mills, brands, designers, retail or other parties. In traditional printing pigment based printing paste is the solution found for the requirements ‘simple process’, ‘low cost’ and ‘acceptable quality’. In digital printing pigment inks cannot fulfill any of these three criteria so far. In order to find a solution to meet those goals, the industry should search for another chemistry/solution than pigments. The industry wants to have a solution for these issues, but nobody has ever seen it.
Several market players are working hard on bringing pigment based inks to the market. However, there is no solution so far available, which allows a high quality textile printing without any pre- and after-treatment. Market prices of pigment-based inks are still very expensive compared to dye based inks, further the all in one ink solution is not yet available.
Future requirements
Digital textile printing will continue to grow and increase its share within textile printing. It has to be understood as a chain of processes from preparation to finishing which so far is not standardised. An accelerated spread of digital textile printing could be expected as soon as there are price attractive reliable printing solutions available, which don’t ask for an industrial environment and allow also high quality prints at brands, retail and design organisations. They will opt for plotter type and scanner type of digital printing machines, single pass technology will remain limited to industrial printers due to the huge production output.
Single pass digital textile printing
With the market introduction of the Lario in 2012, MS Italy presented for the first time a digital textile printing machine offering similar production performance as a traditional rotary screen printing machine. In the meantime, beside MS Italy also SPGPrints (PIKE), Konica Minolta (Nassenger SP-1) and Atexco (Vega One) have sold and installed single pass digital textile printing machines in the industry.
The market for this type of equipment is limited so far since an interested investor has to rely on an industrial environment (pre-treatment and finishing equipment) and has to have an annual production volume of more than 2 million running m to be produced on the single pass machine. In theory, there are many potential customers around the world however main challenge for them is that they simply don’t know how to sell the added value of digital, thus cannot achieve a volume of minimum 2 million m that are necessary to justify the investment in single pass. A single pass digital textile printing machine has to be operated 24/7 in order to be profitable.
Advantages are capability to produce important quantities in a very short time (lead time advantage), fast style change (design, colours) with nearly no installation time, production speed as rotary screen printing, and nearly unlimited flexibility.
Disadvantages are limited market so far, fast developing technology, heavy investment, lifespan of print-heads, quantity of suitable orders to fill capacity, and industrial environment (pre- and after-treatment necessary).
Unique opportunities are offered by this type of machinery in terms of reaction speed and the potential to produce large quantities in very short time.
Style changes can be prepared while the machine is still producing. There are nearly no limitations in quantities of colours and complexity of designs. Once the technology is mature, production cost are further lowered and the reliability of print-heads is given (what is a question of time) there is the potential to replace an important part of installed rotary screen printing capacity.
Pigment inks
As of today, digital textile printing with dye-based inks ask for an industrial environment with highly sophisticated pre- and after-treatment equipment. This fact limits the spread of machines towards garmenting mills, brands, designers, retail or other parties. In traditional printing pigment based printing paste is the solution found for the requirements ‘simple process’, ‘low cost’ and ‘acceptable quality’. In digital printing pigment inks cannot fulfill any of these three criteria so far. In order to find a solution to meet those goals, the industry should search for another chemistry/solution than pigments. The industry wants to have a solution for these issues, but nobody has ever seen it. Several market players are working hard on bringing pigment based inks to the market. However, there is no solution so far available, which allows a high quality textile printing without any pre- and after-treatment. Market prices of pigment-based inks are still very expensive compared to dye based inks, further the all in one ink solution is not yet available.
Future requirements
Digital textile printing will continue to grow and increase its share within textile printing. It has to be understood as a chain of processes from preparation to finishing which so far is not standardised. An accelerated spread of digital textile printing could be expected as soon as there are price attractive reliable printing solutions available, which don’t ask for an industrial environment and allow also high quality prints at brands, retail and design organisations. They will opt for plotter type and scanner type of digital printing machines, single pass technology will remain limited to industrial printers due to the huge production output.