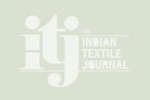
Development of leno carpet
A simple model loom fabricated to produce leno pile carpet at the laboratory stage may provide an alternative to the carpet industry for producing plain carpet on mass scale on which further designing can be done by embossing
A simple model loom fabricated to produce leno pile carpet at the laboratory stage may provide an alternative to the carpet industry for producing plain carpet on mass scale on which further designing can be done by embossing, reveal SK Pal, Anubhav, Suchitra and Deepak.
Carpets are pile structures on a firm base. The pile provides smoother feel and the base provides dimensional stability to the carpet. Loop and cut piles of varying heights give different texture to the carpet. Out of various techniques used to produce pile, handlooms are also used for producing carpets with stripes effect using different colour warp or weft.
On handlooms woollen pile carpets are produced on coarse cotton warp (6/6 Ne – 12/20 Ne) called stuffer ends. They are heavily tensioned to provide dimensional stability to the carpet while coarse woollen yarn (2 – 4 Nm) form the loop pile on the surface by insertion of wire in the pile shed. Two to three coarse waste cotton weft called thari per one row of pile is interlaced across the warp to produce the base of the carpet. Two well known pile shapes used in handloom pile carpet are V-weave and W-weave structures.
In V-weave structure warp constitutes coarse cotton (stuffer ends), fine cotton (chain warp) and low twisted coarse woollen (pile ends) coming from three separate beams and the warp ends are controlled from three heald frames. Two waste cotton weft threads per unit of weave repeat along with stuffer ends and chain warp ends remain in the base of the capet. The pile ends interlacement forming loops on the surface of the carpet with the aid of wires of various size and shape, which are then cut to produce cut pile structure. Each row of pile requires two wefts in consecutive sheds. V-weave structure has poor tuft withdrawal force and the loops are susceptible to be pulled out easily. It therefore requires latexing in order to improve tuft binding within the base of the carpet.
W-weave structure on the other hand has only two sets of warp ends, viz, stuffer and pile ends coming from two separate beams. Each row of pile loops are followed by three weft interlacements per repeat of weave. Thus the warp ends bind the loops securely within the base of the carpet. It therefore provides good tuft withdrawal force (3 – 4 times than that of V-weave structure) without any additional latexing. But one row of pile loop is produced on every four pick cycle. This reduces the rate of production as compared to V-weave.
A new technique of leno weave-based carpet weaving(1) has been evolved, which produces stable pile loops similar to W-weave structure at the same time giving higher production.
Principle of leno weave
It involves two sets of warp ends, viz, standard ends and crossing ends supplied from two separate beams. The crossing end forms the shed on either side of standard end on alternate pick (called plain leno) as shown in Figure 2.
By means of a special mechanism, crossing pile end is raised once on the open shed side and on next pick it crosses the standard end and forms shed on cross shed side as shown in Figure 2. Crossing generally is preferred to take place from below the standard end. Thus the standard end is always over the crossing end and below the weft. The crossing end is always above the weft. Thus it forms a knot-like structure at intersection of warp and weft. This provides stability to the pile loops which are then cut to produce cut pile carpet. Normally, leno weave is used for open structures from finer yarn. But in carpet coarse woollen yarn used as pile ends provide higher friction at the intersection. Though it increases the resistant force needed to pull the cut pile from the carpet termed as tuft withdrawal force but during weaving special care need to be taken.
CATEGORIES Allied Equipment and Accessories