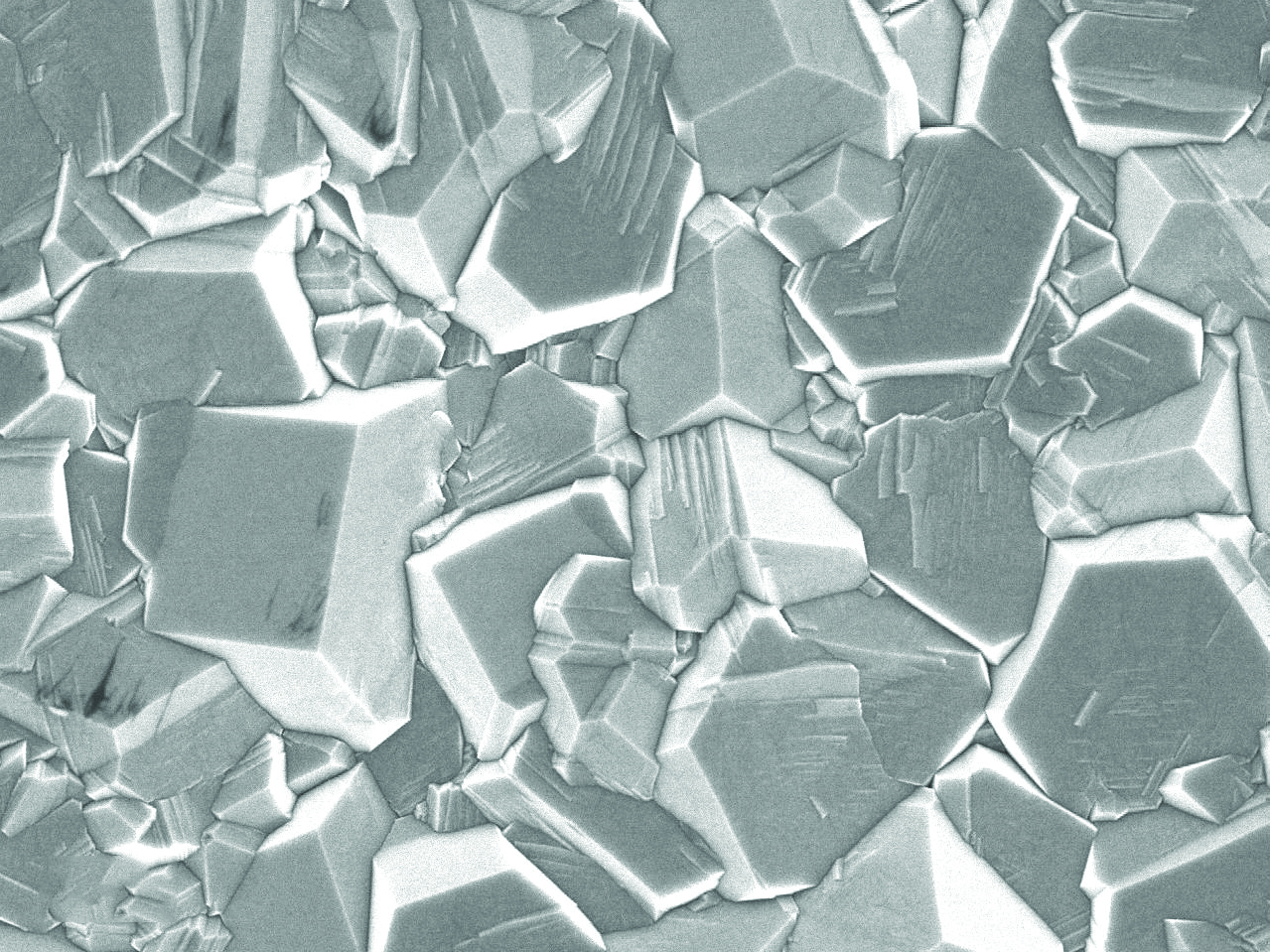
Development of a cost-effective diamond coating process
It increases the service life of thread guides in textile technology.
The processing of spun-dyed and industrial yarns in the textile industry leads to considerable abrasive wear on machine elements, depending on the yarn. For example, an abrasively worn thread guide can affect product quality in downstream process stages. The ‘DiaTex’ research project is therefore developing an economical and cost-efficient CVD diamond-coated yarn guide that leads to a significant increase in service life. This is being achieved by developing a two-part thread guide consisting of a bearing base body and a highly wear-resistant contact zone that is coated with CVD diamond using a direct process. The technology is expected to reduce reject rates, minimise set-up times, increase productivity and improve yarn quality. It can be extended to other applications, which increases the competitiveness of the German textile industry.
Issue
Due to their abrasiveness, spun-dyed yarns and technical fibres cause a high level of wear on machine elements in textile production and pro-cessing. A particularly abrasive processing method is false-twist texturising, where the high production speed of up to 1,500 m/min leads to heavy abrasion on the inlet thread guide of the twisting unit, so that in extreme cases the thread guide wears out within a few days. A worn thread guide leads to increased frictional forces and damage to the yarn, resulting in reduced product quality. Damage to the yarn sometimes only becomes visible in subsequent process stages (e.g. during weaving), meaning that entire batches have to be declared as waste.
This issue is exacerbated by the increasing production speeds and the associated higher temperatures on the surface of the thread guides. One approach to increasing the abrasion resistance of thread guides is the use of diamond coatings, which are deposited directly on the components by chemical vapour deposition (CVD). Diamond coatings are characterised by extreme hardness and wear resistance, which are comparable to natural diamond and have already been successfully established in other areas of application, for example in toolmaking or for highly stressed machine components. In contrast, the use of diamond coatings in the textile industry has not yet become widely accepted, particularly due to the high cost pressure.
Aim and approach
Within the scope of the “DiaTex” research project, an economical CVD diamond-coated thread guide is therefore to be developed, which increases the service life of this critical machine element in textile production by a factor of 20 to 100 and is also cost-efficient. To reduce costs, the thread guide is constructed from two components, consisting of a bearing base body and a highly wear-resistant thread-guiding insert (Figure 1). The multi-part design enables the economical diamond coating of a replaceable con-tact zone designed to be suitable for coating and application. At the same time, research is being conducted into an economical coating process for market-acceptable component costs in order not to exceed a target cost limit of approximately 10 € per component.
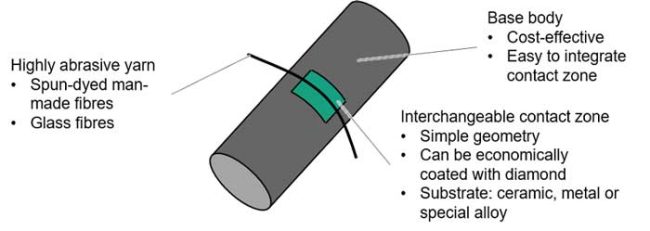
Figure 1: Schematic representation of a two-part thread guide consisting of a cost-effective base body and a CVD diamond-coated, thread-guiding contact zone.
Solution
Firstly, the technical requirements for the base body and the exchangeable contact zone are defined. Based on this, the tribologically adapted thread guide is developed, which is divided into the research of the application-adapted coating process, the new design of the thread guide with ex-changeable contact zone and the tribological evaluation of various diamond coating systems. The developed coating systems are then validated in the application environment of a texturing process in order to iteratively adapt the coating system to the load case. At the same time, the coating process is scaled up to enable economical coating and reduce unit costs. Finally, the knowledge gained is transferred to a second, highly abrasive application (e.g. glass or rayon fibres) and an economic evaluation is carried out.
Economic significance & benefits
By reducing wear on thread guides in general and on the inlet thread guide of the twisting unit in particular, the aim is to reduce reject rates and minimise set-up times, resulting in a significant cost reduction in the textile process chain. In addition, the quality of the processed yarns is improved, as the thread guide wears more slowly and thus causes fewer subsequent defects along the textile process chain. The technology can be extended to other fields of application, such as the processing of comparatively cost-intensive high-modulus fibres such as glass and carbon fibres. Here, wear-resistant machine elements are also crucial for production efficiency. The targeted increase in service life through CVD diamond-coated thread guides can reduce downtimes and lower production costs, thereby increasing the turnover, productivity and competitiveness of the German textile industry. This is a major economic lever for the price-driven textile industry and helps German and European companies in particular to compete with textile producers in low-wage countries.
Acknowledgement
The IGF project No.: 23095 N of AiF Projekt GmbH, Berlin is funded by the Federal Ministry of Economics and Climate Protection within the framework of the Industrial Collective Research Programme (IGF) on the basis of a resolution of the German Bundestag.
About the author:
Lukas Lechthaler, Lukasz Debicki, and Thomas Gries are from the RWTH Aachen Institute of Textile Technology.
Sarah Baron, Christian Stein, and Markus Höfer, are from the Fraunhofer Institute for Surface Engineering and Thin Films.