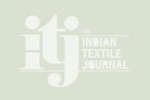
Cut-resistant fabrics
Cut-resistant fabrics are gaining popularity in the field of protective fabrics. Recently developed cut-resistant fabric products such as gloves and aprons have many advantages over the conventional materials,
Cut-resistant fabrics are gaining popularity in the field of protective fabrics. Recently developed cut-resistant fabric products such as gloves and aprons have many advantages over the conventional materials, say MY Gudiyawar and Saloni Sharma
Cut-resistance of fabrics is an important attribute for some special technical applications. Cutresistance is defined as the ability of a material to resist damage when challenged with a moving sharp edge. Cutting, which involves a normal and a sliding movement, is strongly controlled by friction between the blade and cut material. It is the total energy required to propagate a cut and strongly depends on the coefficient of friction between the cutting edge and the material. However, this coefficient of friction depends on both the nature of the blade and nature of the cut material, especially its surface roughness.
The conventional means of protection were wire mesh steel gloves, leather gloves and gloves made of some alloys. Many of them were uncomfortable and provided little protection. After the invention of high performance polymers and materials, considerable research is focused on personal safety equipment.
High modulus high strength polymers such as p-aramid, PBI, and ultra high density polyethylene have been introduced in personal protective devices in the form of fibres, yarns, fabrics or composite reinforcements. Their performance encouraged the technologist to design and engineer innovative personal safety equipment for protection against fire, ballistic, chemical, biological, nuclear, fall and cut injury. High strength to weight ratio of these fibres is the major advantage over the conventional metals of steel, and alloys. Most of these fibres are pliable, flexible and exhibit textile characteristics making them easy to fabricate and ideal to wear. Todays market for cut resistance gloves requires rising protection in combination with higher comfort levels.
Cut resistance is the property that hinders the penetration of the cutting edge entirely through material, when a material or a combination of materials is exposed to a sharp-edged device. Increased cut protection can be achieved with the use of high performance fibres and use of composite yarns made with varying combinations of stainless steel, fibreglass and high performance materials. The level of cut resistance provided by the reinforcing yarns depends on the way in which they are incorporated in the textile substrate. Metal ring meshes are traditionally used for cut protection in food industries such as meat processing, and have been incorporated into some stab resistance vests.
Textile reinforcements have been widely used as they provide flexibility, comfort and protection as cut resistance materials. For the construction of flexible cut resistance materials, high performance fibre such as aramid and ultra high molecular weight polyethylene are preferred due to their inherent mechanical properties.
These fibres can be manufactured into fabrics by weaving, knitting or nonwoven technologies. There are number of commercial stab-resistant fabrics available under brand names such as Argus (Barrday Inc), Kevlar MTP (DuPont), Twaron SRM (Teijin-Twaron).
Mechanism of cut resistance fibres
The cutting process, which is referred to as the moving of fibre material away from the fibre/blade contact point, involves the application of mechanical forces in the direction transverse to the fibre axis. A sliding sharp edge penetrating material is one of the most dangerous cases of cutting because it requires the smallest applied load. In practice, cut resistance of a material is contributed by the intrinsic strength of material and the frictional distribution.
Two types of frictional distributions are involved in cutting: a macroscopic friction induced by the gripping of the mate