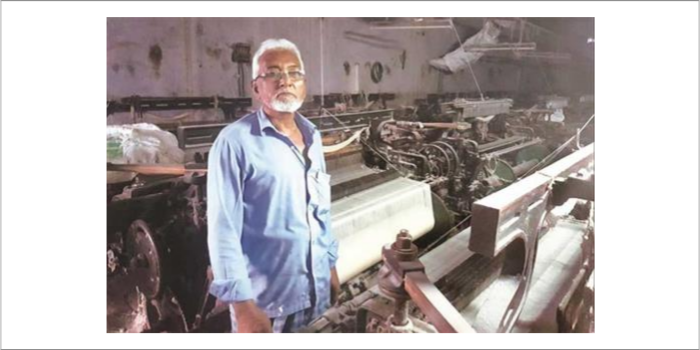
Crisis in Bhiwandi powerloom sector
Bhiwandi has approximately 6.5 lakh power looms, which is 33 per cent of country’s total power looms. Out of 6.5 lakh, about 15-20,000 looms are automatic and mostly China made rapier, writes B Basu.
The role of the Bhiwandi powerloom sector in relation to the mass and cheap cloth production and massive employment especially of the medium to low qualified people cannot be ruled out. It is one of the oldest decentralised powerloom sectors in India. Being nearer to the Bombay textile market and port, it has gained its importance and fame.
Today 40 per cent of the powerlooms are closed and there is very much uncertainty is prevailing. GST, demonetisation, etc. are added fuel to their ever-lasting crisis. Old machinery, lack in technical knowhow and commercial knowledge, hunger for the loans and subsidies, fluctuating yarn prices are the root causes to swell out the crisis in larger way. On the other hand, those who are quality producers having Auto looms are not unhappy except that of high-power tariff and poor infrastructures. Proper support and technical advices by the TRA’s would have improve their sustainability to a great extent.
Brief history of Bhiwandi textile industry
The factors affecting the progress
Yarn prices: The manufacturers in Bhiwandi are plagued with cheap Chinese products. Traders have to pay a duty on ready-made stock produced in Bhiwandi whereas Chinese products are exempt from it. The Indian cloth became costly due to vacillating polyester yarn prices with 12 per cent GST, high electricity charges and duty imposed by the government. Chinese manufacturers are at an advantage as China provides material at low prices. About 35 per cent looms in Bhiwandi have closed down and more than 2.5 lakh people have migrated to other places in pursuit of their livelihood. The prices as well as the supply of yarn should be balanced or reshuffled on a regular basis (fortnightly), and then there could be some relief. The GST for the cotton is 5 per cent but both the cotton and polyester should be equal.
Intekhab Alam Ansari, a labourer associated with a power loom, said that his forefathers were also associated with the power loom sector and claimed that 15 years ago the price of yarn was changed monthly but now there was no control over the price of yarn. Alam said that there was no fixed price, quantity or quality mark on the boxes of yarn and yarn traders had been given a free hand to change prices at any time. The loom owners had no option but to follow prices and sell products in the market with the rate fixed in advance by ready-made purchasers.
Suhail Ansari, President of Panchpeer Islampura Quresh Power Loom Association (PIQPLA), said that price of yarn should be fixed, and price changes cannot be made more than once in a month. Faizan Azmi, president of the Maharashtra Power Loom Federation, said that black marketing in cotton and cotton yarn supply badly hit the industry. For years they had been demanding the government to assess the situation but neither the previous nor the current government had shown any interest in the matter.
The powerloom owners claim that ups and downs in the yarn prices were a gamble and they incurred enormous losses. Such unstable economic situations make it difficult for them to pay salaries on time.
Bad working condition: They reduced the workforce in order to tackle some of the losses they incur on a daily basis. Nothing much can be done, since decline in the local textile industry augmented problems.
Sensing inhuman work conditions in the looms, the young generation has shied away from taking up employment in these units. Educated young people take up jobs in corporates and various organisations and earn in a month what their parents were earning in a year. The youths who are less educated were looking for other businesses rather than thinking of joining looms. A mass of them are shifting to the newly built warehouses at nearby areas with higher wages and better working atmosphere.
A federation of various smaller organisations of loom workers, working under the banner of “Sangharsh Samiti” is trying to address the issues faced by the power loom industry. One hopes that the authorities will take heed to improve the financial and social condition of this industrial town and protect the livelihood of the many labourers who depend on the power loom industry. Poor infrastructure, bad roads, haphazard way for growing the loom shed, tremendous traffic chaos in the city, unhealthy working situations brings the youths Not to take up a job as a weaver in the loom shed.
Silence of the looms: The power loom sector in Bhiwandi, Maharashtra, bleeds from demonetisation and GST. If India Inc has been reporting losses and its head honchos have been speaking out against Goods and Services Tax (GST) and the after-effects of demonetisation, it does not take much to imagine the situation of small businesses. Backed by financial and technical resources, big businesses have managed to roll with the punches and are likely to land on their feet, but small businesses have had to deal first with the sudden shock of demonetisation and then the red tape of the world of GST. In Maharashtra, the plight of Bhiwandi encapsulates what demonetisation and GST have done to small businesses.
The nightmare of demonetisation as experienced in the rest of the country kept snowballing until finally in December 2016, Bhiwandi’s looms were switched off: there was a paucity of workers, and a cash crunch ensued because of no-sale, no-purchase. The situation was bad enough for Union Textile Minister Smriti Irani to visit Bhiwandi and assess the situation, after which work resumed.
The power loom industry had been on a downward spiral for some years. About 30 per cent of the looms had shut down over a two-year period because of unstable yarn prices, high export duties and competition from China. But “never once did we think Bhiwandi’s future was dark,” says Mohsin Mohammed Tarir, who owns about 100 power looms, “but this time we have doubts about the survival of the entire industry.”
Power cost: The power cost in cluster is around Rs 8.25 to Rs 8.30 per unit. However, the government provides a power subsidy of Rs 3.00 per unit so the net power cost to the company is about Rs 5.25 – Rs 5.30 per unit. Till now it is limited to the dyehouses. They have the allegations that it requires to grease the palm of the concerned officers to get the subsidy.
Modernisation: The Ordinary power looms are as old as 50 years and most of the Auto looms are second hand and also the older. Hardly anyone is having Humidification Plant to run the Looms efficiently. To compete in the global market, it requires good mc. Good raw material, and skilled manpower. The owners expect incentives for the modernisation. The TUF though implemented but the weavers say that they are yet to get the refund (survey as on August 2019). The office of the *Commissioner of Textile who take care of the TUF say that the fund is ready but because of the incomplete Data, it is taking time to process.
The weavers say that the Banks are not coming forwards in support of them. The *TC office says that Bank loan etc can be granted subject the proper feedback and clear records.
Skill workforce not available: To operate the looms especially the Auto looms, it requires skilled operators which are not available. The power loom service centres were not capable to train the labour force properly. ISDS was not the successful mission at all. (the author was the man behind the setting up of the ISDS at the Power loom service centre hence well aware of the facts). More service centres are required to strengthen the Power loom sectors as the weavers conclude.
Non availability of the special yarn: For any new Product development, it requires special yarn supplied by the polyester Yarn manufacturers (say for example: 1200 denier Micro, or FD of 108 filaments), but they do not supply any small quantity. Hence, it is demanded by the weavers to have R& D centres for the new Product developments.
The less export potentiality: Some prominent weavers say that they are capable to do exports as they are quality producers having automatic looms. As on today, hardly any one directly exports to any country. The Exporters purchase the quality fabrics from the weavers and send to various countries. They are mostly the traders and the producers do not get any profit share.
The prominent power loom owners say that there is no proper modern Dye House in Bhiwandi who can give proper finishing on the fabrics that can be exported. The Present Dye Houses are not well equipped nor follow the Pollution norms strictly.
The Garment manufacturers are also in the opinion that because of the huge incoming of cloths from Bangladesh, China (via Bangladesh), they are suffering a lot.
The local Administration: There is a good demand among the prominent owners that there should be good labour laws so that they can be retained after gaining good experiences. The Factory owners also expect good pollution control system at Bhiwandi area.
The road ahead
The problems and the worries at Bhiwandi powerloom sectors are ever remaining since the inception and time to time the problems enhance and reduce also. There should be regular meetings with the Loom owners, Yarn suppliers, State Administrators, municipality and Textile Commissioner Office to resolve the problems on priority basis than to blame each others.
Strength:
Weakness:
Opportunities:
Threat:
Survey report that indicates crisis
We have collected the feedback from the College of Management, Bhiwandi after doing a survey in collaboration with the loom shed owners of medium size.
Sufferings of Bhiwandi powerloom sector
Sr. No Factors affecting % Yes % No
1 High cost of production 82% 18%
2 High cost of raw material 70% 30%
3. Facing market competition 41% 59%
4. Management not willing to 53% 47%
run the industries and
like to
convert in more
lucrative industry
5. Labour unrest 59% 41%
6. Financial crisis 94% 6%
7. Not getting proper support 88% 12%
from Textile Ministry,
bank
8. Not modernised 70% 30%
9. No new product developments 53% 47%
10 No R&D 82% 18%
11. Unprofessional management 76% 24%
12. Unskilled/untrained workforce
65% 53%
14. High power cost 88% 12%
15. Poor marketing strategy 76% 24%
16. Poor mission/vision/strategic
82% 18%
Planning
Some suggestions received:
(i) Union is too rigid
(ii) Bad road condition damage the raw material and finished goods
(iii) Torrent Power is charging high and no proper services/facilities are provided
(iv) Labours demand high salaries time to time
(v) Needs to produce quality materials.
(vi) There should be more export
(vii) Some feels that salary of the labours is to be increased
My conclusions: (i) It is just a guideline how the Bhiwandi Power Loom Industries are sufferings (ii) More elaborate studies can be conducted by Combine efforts of the college and myself (iii) Then this paper can be published in International journal. (iv) More suggestions, guidance’s can be taken from the Commissioner of Textile. (v) Financial help to conduct this Project can also be taken from the Ministry of Textile.
Conclusions
References
(i) Tales of Bhiwandi ( economic and political weekly, journal » Vol. 51, Issue No. 16, 16 Apr, 2016 » Tales of Bhiwandi) Trouble in the Power Loom Town
(ii) Front Line, 13th Sept Rs.19 By Lyla Bavadam
(iii) Victims of New Economy and Crisis in powerloom Sector (Bhiwandi Nizampur Municipal Corporation). Gazala Bhoje (Assistant Professor, Department of Sociology, K.M.E. Society’s G.M. Momin Women’s College, Rais High School Campus, Bhiwandi Dist, Thane.
Footnote:
B Basu is a visiting faculty at VJTI, Mumbai. He can be contacted at: Email: Bibekananda.basu1502@gmail.com | Tel: 09867682084.