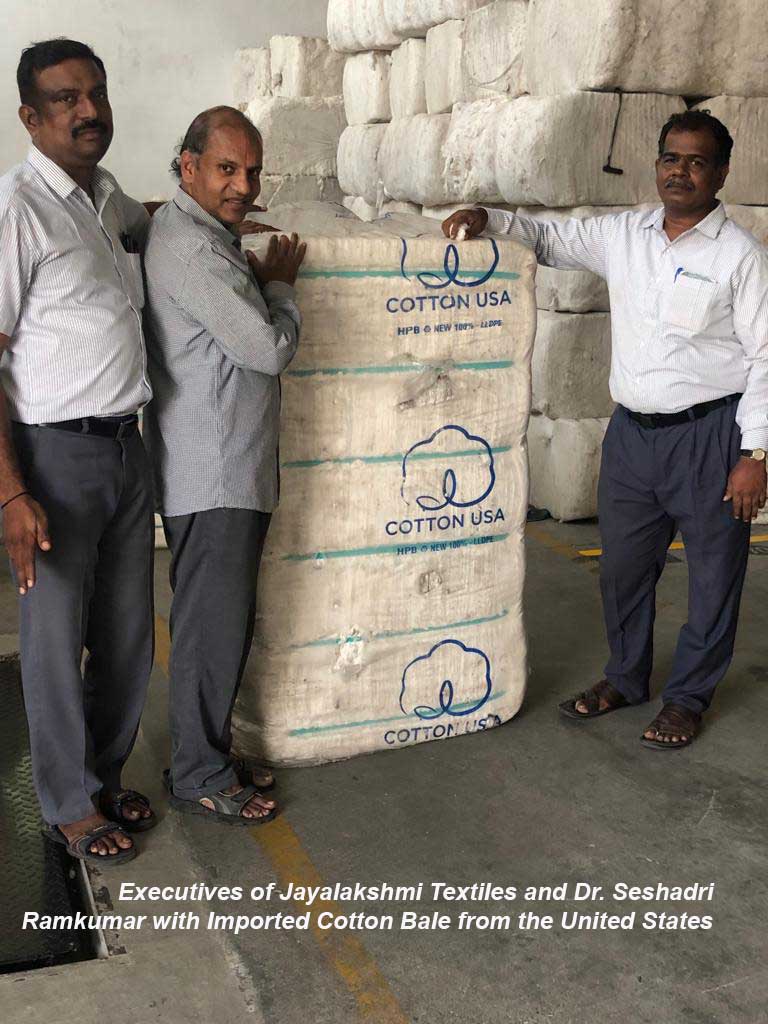
Cotton fibre sector development is urgently needed
Seshadri Ramkumar Professor Texas Tech University, USA, emphasizes state and national agencies to interact regularly with farmers and the end-users during the planting season to have better handle on the data, weather, and agronomical aspects.
Cotton fibre is gaining attention globally and in the mainstream media in India in recent times due to high volatility in the market.
Spinning sector in India and globally are witnessing severe price squeeze due to high price and less demand. Within a year since July 2021, cotton price has shot up by 50 percent. For example, last year about this time, MCU-5 cotton was selling at Rs 59,000/Candy, while the price is about Rs 89,000/Candy. One candy is about 355.62 Kgs.
Today, I had the opportunity to visit Jayalakshmi Textiles in Aruppukottai to witness firsthand the situation in a spinning industry.
In a candid discussion with Shanmugam Velmurugan, General Manager of the 70,000-spindle mill, it became evident that the cotton sector from the farm level must gear up to meet the challenges faced by the spinning industry.
Firstly, yield improvement must be immediately enhanced stated Velmurugan. India although having largest acreage dedicated to cotton, it has the lowest productivity/hectare, about 462 Kgs/hectare as against the United States at 1000 Kgs/hectare. This necessitates seed improvements with latest biotechnology traits to counter issues from drought and pests.
Second aspect is focusing on the variability within the region in terms of fiber quality. Seed companies, state and national level agricultural agencies, and industry must collaborate with farmers in planting uniform variety to have better control on fiber variabilities. Velmurugan states that when doing bulk purchase of cotton by mills, variation in varieties from field to field causes issues regarding quality. Farmers have to be better engaged so that some control on regional variations can be achieved.
Third aspect is focusing on contamination at farm and gin levels. In addition to machine clearing at blowrooms in spinning mills, the industry has to have manual inspection and cleaning to have better contamination control. Normally 4 to 5 people are employed per shift for this operation. Contamination arises due to packaging materials made using plastic and jute, food packings and other materials due to manual handling of fiber. Awareness creation is needed to counter these issues in addition to machine level interventions.
Another aspect for the development is to focus on enhancing fiber quality. Indian industry has so far focused on length, micronaire, strength and color. Jayalakshmi Textiles has recently started focusing on other properties such as elongation. This necessitates the importance of HVI testing of fiber at mills. Mills in India normally do 20% testing of bales using HVI. Jayalakshmi Textiles consumes 40,000 bales and so, only about 8,000 bales are evaluated using high volume instruments using HVI and AFIS.
“Since we started purchasing cotton from the United States, we pay attention to fibre elongation,” stated Velmurugan. Fibre elongation is important for fibre performance in spinning and weaving with reduced breaks. Even a 2% increase in fibre elongation matters, adds Velmurugan. Cotton breeding should focus on fiber quality and not only on yield.
During my recent trip to India, I have been promoting the use of quality testing and the availability of reliable and timely data. Stakeholders must first create the awareness on the importance of timely and reliable data involving production and quality. State and national agencies should interact regularly with farmers and the end-users during the planting season to have better handle on the data, weather, and agronomical aspects.
Cotton revolution in India should begin at farm level with input from stakeholders such as end-users, say apparel makers and brands. The current high volatility situation opens-up opportunity to focus on long-term planning for the cotton sector from fiber to fashion supply chain.
About the Author:
Dr Seshadri Ramkumar is the Professor, Nonwovens & Advanced Materials Laboratory, at Texas Tech University, Texas, USA. Email: s.ramkumar@ttu.edu, or http://www.tiehh.ttu.edu/sramkuma