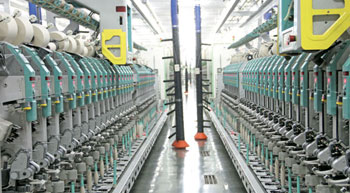
Cost control in spinning mill
For the best working of a spinning mill, we have to keep everything ideal, based on industry norms, benchmarking with the best technical study by an independent research institute and our own achieved figures, feels SB Agarwal.
For the best working of a spinning mill, we have to keep everything ideal, based on industry norms, benchmarking with the best technical study by an independent research institute and our own achieved figures, feels SB Agarwal.
Let me explain: Cost control does not mean cost reduction only, in fact cost increase may also result in cost reduction. We have to find what is the ideal cost. If expenses are lower than ideal we may have to spend more.
Raw material: There is always a tendency to reduce mixing cost with lower quality cotton polyester, waste, etc. Mixing cost may reduce but the losses in speed, productivity, wastage life of rings, cots, aprons, breakages and realisation rate, and quality may be three times than the cost saved. Little increase in mixing cost may give better results and may offset higher cost with better quality and better realisation. One has to find by different trials an ideal mixing. A better mixing will definitely reduce wastages, machine breakdown, and will improve quality and realisation.
Power: Maximum power is consumed in the air conditioning and humidification plants. Generally, mills tend to reduce power supply, reduce power cost, by reducing air supply to fans but this may result in bad working, more breaks, more waste, workers discomfort, etc. and losses will be more than the gains. Ideal conditions suiting to the raw material and workers comfort must be maintained.
Store Consumption: In one mill we tried to reduce consumption of stores and spares parts by extending the life of ring spindles, cots and aprons. This resulted in lower consumption and saving but started reflecting in more breakdowns, bad working, more wastage and more consumption of stores and spares. We got the store consumption study done by Atira and report clearly showed our stores and spares consumption was 113rd of the ideal.
Labour: Number of labour and workload. Very interesting subject keeping higher than ideal workload would mean negligence by worker resulting in idle spindle, more bonda and waste, higher breakages, poor housekeeping, etc., further resulting in all round losses.
Inventory level and interest on inventory: In our anxiety to reduce number of days of inventory, we had introduced Kanban system like Japan but failed badly because of the logistics problem and poor supply chain management. Many a time we faced shortage of raw material, dyes and chemicals, stores and spares, etc., which affected the production adversely. We were unable to deliver goods to customer off the shelf and on time.
Overtime: This is the biggest evil in the industry and many people are reconciled to overtime system assuming there will be labour shortage during marriage and harvesting season, and any other festival. Many a time the lower management also gets involved and click is formed between junior staff and workers and they oblige each other. There are many mills which have no labour shortage only because of their better policies. There can be many ways to control this evil by brain-storming and learning from bench mark mill.
With regard to staff cost and other general expenses, mills should invest in systems and computers and reduce spending on number of staffs as they can leave and can fall ill, but the system is safe from all this. All other expenses are directly or indirectly related to staff only.
Conclusion: But this is the modified side. For the best working we have to keep everything ideal, based on calculation industry norms, benchmarking with the best, technical study by independent research institute and our own best achieved figures. Be it inventory raw material cost, power cost, labour cost, stores and spares cost and all other cost. This will give us best working. This is a tried & trusted system and every unit has to fix up its own norms.
SB Agarwal (author) has been working in textile industry for last 50 years holding senior-most position in Aditya Birla Group.