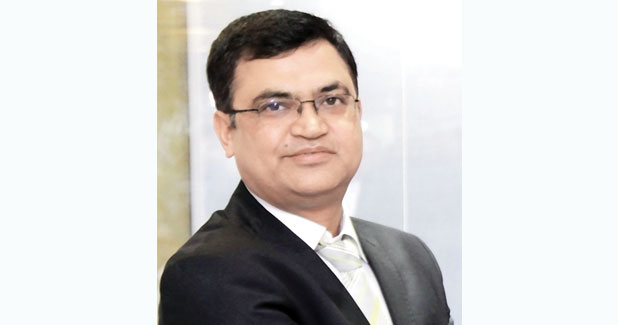
Continuous investment in R&D is Rieter’s forte
Incorporated on August 1, 1995 as a wholly owned subsidiary of Rieter Group, Switzerland, Rieter India Private Limited is one of the leaders in the market for textile spinning machines, and is recognised as a supplier of entire spinning systems from a single source, complemented by its reliable and proficient customer service. Rieter India provides sales, service and technical support from the branch offices at Coimbatore, Chandigarh, Ahmedabad, Bhilwara and Guntur. Rieter India manufactures its spinning product range from its manufacturing facility at Wing, Satara.
Incorporated on August 1, 1995 as a wholly owned subsidiary of Rieter Group, Switzerland, Rieter India Private Limited is one of the leaders in the market for textile spinning machines, and is recognised as a supplier of entire spinning systems from a single source, complemented by its reliable and proficient customer service. Rieter India provides sales, service and technical support from the branch offices at Coimbatore, Chandigarh, Ahmedabad, Bhilwara and Guntur. Rieter India manufactures its spinning product range from its manufacturing facility at Wing, Satara.
Prasanta Deka, Vice President – Sales and Marketing, Rieter India Private Limited, speaks on Rieter’s and Rieter Components’ experience at India-ITME 2016, and its machines for the spinning industry.
Excerpts…
In less than two decades, Rieter has made commendable progress in India, please trace the developments since its beginning in India.
Rieter’s close association with Indian spinning industry is more than 60 years now. With economic liberalisation in India in 1990, Rieter started supplying spinning equipment to all 100 per cent export oriented units which continued until the year 2000. Being user of latest innovations and machinery, India spinning industry continued buying Rieter equipment under various schemes like EPCG.Rieter already had in place successful sales and aftersales service set up in India since 1995. To get closer to our customers and as a part of global foot print programme, Rieter started manufacturing in India in 2007. Starting with draw frames and ring spinning machines from the local manufacturing units, other products like combers, compact spinning, blow room and cards were added in the local portfolio.As Rieter offers same technology worldwide from its different manufacturing sites, customers were happy and supported by buying equipment from us.
How has the Rieter Components section been doing in India?
The products from Bräcker, Graf, Novibra and Suessen were very well received throughout all Indian spinners. Titan rings, ring travellers, as well as Berkol machines from Bräcker are setting benchmarks in regards to production speed, lifetime as well as flexibility. The new launched BERKOL® multigrinder, is the only grinding machine in the market which enables customers to process the entire range of top rollers and cots used in an spinning mill on one single machine.
Graf card clothings and combs are appreciated as the best value for money products in the industry. With the introduction of the EasyTop generation of flat clothings, Graf is able to provide card clothings in the established and reliable quality for all known types of flat cards from one source irrespective of either raw material, further processes or production rate. EasyTop is suitable for aluminum flat bars with magnetic adhesion technology from all manufacturers. The application of the well-known and proven Graf flat clothings is thus assured on all flat bars, irrespective of the mode of attachment.
With the newly-launched X-Comb, Graf is tapping into the market of exchangeable combing segments with well-known Graf technology for economical combing result. The exchangeable combing segments are suitable for all conventional combs requiring this technology. In combination with the straight-forward and quick installation as well as the possibility to exchange individual segments this can result in an improved cost-efficiency.
LENA (Low Energy Noise Absorption) spindles from Novibra are reducing energy consumption on ring spinning machines by up to 6.5 per cent.These figures were measured in mill and confirmed by leading spinning factories in India like: Mohan Spintex India Limited, Sportking India Limited, Nagreeka Group, Nahar Spinning Mills Ltd.member of Nahar Group. We would like to take the occasion to thanks all the above-mentioned companies to allow us to do the trials and public the achieved results. In addition to LENA spindles, Novibra owns in her product portfolio the only 100 per cent underwinding free spindle system CROCOdoff, which works independent from the ring spinning machine control unit and can be used in any type ring spinning machine.
Last but not least, the compacting system of Rieter and Suessen. Without any doubt Com4® and EliTe® are synonymous for ring compacting systems worldwide and with a large extension in India. On the occasion of the last ITME, these two systems have celebrated their 15 million running spindles worldwide. A celebration which was attended by many leading spinners in India and sustained by BK Patodia, Chairman and Managing Director, GTN Group; Sudhakar Chowdary, Managing Director of Mohan Spintex; BB Sharma, CEO (Textile Projects), Sintex; and other key customers with the senior management team of Rieter and Suessen.
How was the Rieter and Rieter Components’ experience at India-ITME 2016?
India ITME is one of the important exhibitions for India and also for South Asian countries. India ITME 2016 was a successful exhibition for us both in terms of visitors and showcasing our successful technology and products. We received and attended very high number of investors, promoters, entrepreneurs and technical level dignitaries from the spinning industry not only from India but also from countries like Bangladesh, Iran, Pakistan and Sri Lanka.
All four companies are looking back to a very successful ITME despite the pre conditions (demonetisation) we experienced just a few days before exhibition started. Besides fruitful meetings during the exhibition, many projects discussed are now being concluded.
Which are the particular machines which have made inroads into the spinning industry in the recent times? What are their USPs?
India today has expertise on cotton ring spinning with 90 per cent of the capacity installed for ring spinning and cotton being 75 per cent of the total fibre consumed. Eventually most of machines coming into the market recently are for cotton ring/compact spinning. The share of compact spinning has increased recently with increasing demand for compact yarns from the end user.
There are also modernisation programmes where old draw frames and combers are under modernisation. Customers prefer to adapt modernisation programmes with investments in draw frames and combers that guarantee unrivalled quality and first-rate raw material utilisation.
Today customers look for long term value of equipment they buy. Long term values are derived from consistent productivity and quality in the long run, lower energy consumption, longer life time and equipment which are ready for upgrades in future to match new technology. In addition, customer looks for very strong after sales service support. Rieter is able to offer all the above making it a win win situation.
For Rieter Components, first of all, compacting technology in ring spinning was a breakthrough and our contribution to the success were essential by launching and introducing Rieter K 42 compact spinning machine and Suessen EliTe®Compact Spinning Systems. Spindles from Novibra together with rings and travellers from Bräcker enabled customers for the first time to reach spindle speeds above 20 000 rpm. Graf wires continue to set standards in fibre yield within the carding and combing processes.
How has the compact spinning doing in India since its introduction?
As mentioned earlier, compact spinning is doing very well in India. Rieter offers K 42 compact spinning machines locally from Indian manufacturing plant and Suessen EliTe® compacting system suitable to any make of ring spinning machines. As the compact yarn segment is growing at a fast speed, Rieter is able to provide customers an integrated solution by offering our compact spinning system. Large quantity of compact spinning spindles have been supplied to the Indian spinning industry in 2015 and 2016.
Suessen EliteCompact set is claimed to have fared very well in the Indian market. What are the factors behind its success?
Suessen has made considerable investments in continuous R&D, combined with applied research that is directly carried out at our customers’ mills. This ensures that the company is able to further develop its technical and technological components in an uncompromising and resolute manner. In particular, Suessen has been focusing on universal applicability, improved yarn quality, increased service life, reduced maintenance and proven reliability in industrial application.
What are the facilities and aftersales Rieter offer in India? Give some details.
Rieter has production facility in Pune, Maharashtra. Sales and after sales services are provided from our offices and residential offices located in Pune, Chandigarh, Coimbatore, Mumbai, Ahmedabad, Bhopal, Bhilwara and Guntur.
Rieter offers complete compact spinning system from the local manufacturing unit in Pune. It also offers Ring Spinning machines with sliver preparation process from this plant. After sales service team provide installation and commissioning services, parts and technology services, mill assessments, customer training and yarn engineering services.
How does Rieter Components tackle competition from domestic manufacturers and cheap imports?
We aim to be always a step ahead in regards to product innovations and customer services. Customers who buy cheap do not buy the most favourable economic package.
What are the future plans of Rieter in India? Will there be investment in production sites sites or any other such plans?
Production site in Pune has already developed the capacity required for Rieter to cater to the Indian market. All planned investments have been executed. It is always a challenge to foresee how the industry will develop in future. Any additional investment into Indian production will depend on the market need in future.