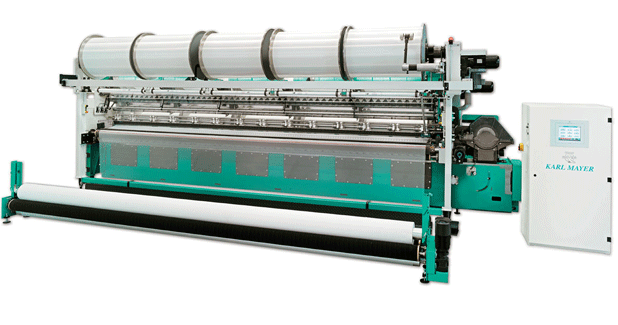
CFRP use in warp knitting cuts energy consumption
For a long time now energy-saving machine concepts have been the key aspect of KARL MAYER´s R&D work. Energy has different functions in the operation of a warp knitting machine: mainly the drive of the knitting elements but also the cooling of the components
For a long time now energy-saving machine concepts have been the key aspect of KARL MAYER´s R&D work.
Energy has different functions in the operation of a warp knitting machine: mainly the drive of the knitting elements but also the cooling of the components which must perfectly meet the specific requirements within a certain temperature range due to their material-conditioned features. Nowadays the consumption of energy is an important ecological aspect as well as an expense factor.
KARL MAYER reduces the energy required in warp knitting by using machine components made from temperature-stable carbon fibres – this is the commitment of the Obertshausen-based textile machinery manufacturer to the sustainability initiative entitled ¨Blue Competence¨ organized by VDMA (German Engineering Federation). It was already in May 2011 that Fritz P Mayer, the company´s CEO at that time, put his signature to the document confirming Karl Mayer´s participation in the activities of the German Engineering Federation.
Limited performance due to metals: For a long time now energy-saving machine concepts have been the key aspect of KARL MAYER´s R&D work.
The machine parts of warp knitting machines should be solid and sturdy because they must withstand different effective forces. This is the reason why in the past the component design mainly focused on metal. But some of the material properties of metals considerably restrict the freedom of mechanical engineering. In particular the weight of the metal bars and the thermal expansion of the material as well as its limited stiffness restrict the machinery builder´s possibilities increasing the rotational speed of the machines for obtaining higher textile productivity.
An alternative in this respect is carbon fiber reinforced plastic, so-called CFRP. This innovative composite is increasingly employed as lightweight construction material by users in future-oriented growth markets, and also by KARL MAYER. A few years ago the pioneer in this area also discovered the advantages of CFRP for the manufacture of components intended for his own warp knitting machines.
CFRP means more output and less energy consumption: Due to its mechanical properties, CFRP clearly stands out from other plastics and metals. This efficient composite offers a high tensile strength and stiffness as well as extremely low heat expansion along with a density of only 1.55 kg/dm³ – in other words: an excellent performance which makes it the ideal material for many applications, for example for the manufacture of bars. Components made from CFRP have six times higher stiffness and up to eight times higher strength than aluminium, and this with the same weight. In this way, it is possible to reduce the component weight, at the same time achieving a high material rigidity and strength.
As far as the KARL MAYER machines are concerned, CFRP offers minimum thermal expansion, the capacity to reduce the bar weight as well as high material stiffness and strength. These features ensure a considerable increase in productivity, the rotational machine speed could be increased by 30 per cent.
This material also has a previously unequalled temperature stability, thus, offering the chance to extend the temperature tolerance range to 14°C whilst ensuring a trouble-free operation. Temperature fluctuations-which formerly resulted in machine stops or in adjustments of the rotational speed, thus, leading to increased energy consumption-can now be ignored thanks to the CFRP technology.
Last but not least, the vibration damping feature of CFRP ensures a consistently high quality of the products, a fact that is of particular importance to customers. Other important advantages resulting from the use of this innovative composite are 16 per cent less investment costs and 26 per cent lower energy consumption of the air-conditioning system.
PVA creates right chemistry be