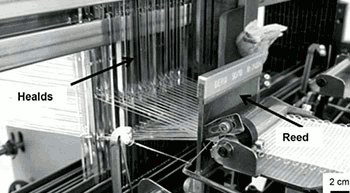
Can SRPC be made of single biopolymer family?
Self-reinforced polymer composites (SRPC) consist of highly oriented reinforced polymer fibres and a low melting fraction of the same polymer family as matrix, write Marie-Isabel Popzyk, Sangeetha Ramaswamy, Volker Niebel, Thomas Gries, Linde De Vriese, Kristel Beckers and Lien Van der Schueren.
Self-reinforced polymer composites (SRPC) consist of highly oriented reinforced polymer fibres and a low melting fraction of the same polymer family as matrix, write Marie-Isabel Popzyk, Sangeetha Ramaswamy, Volker Niebel, Thomas Gries, Linde De Vriese, Kristel Beckers and Lien Van der Schueren.
The principles of SRPC (self reinforced polymer composites) were defined about 20 years ago, but the industrial interest is nowadays expanding fast [1, 2]. SRPC fibres and matrix are made of the same polymer family. SRPC do have better mechanical properties in comparison with conventional polymer plates because they keep their polymer orientation in the final product. Because fibres and matrix are made from the same polymer family the product can be easily recycled after its end of life. Also, the interest in bio based polymers is growing fast [3] and in particular Poly (lactic acid) (PLA) finds interesting applications in e.g. packaging foil or nonwoven applications like cleaning cloths or agro textiles. Bio based polymers such as PLA are still in their infancy and high value end products are needed to bring these materials to full maturity.
The Institut für Textiltechnik of RWTH Aachen University (ITA), Germany, develops with two Belgian project partners, Centexbel and Sirris, bio based SRPC in the project ?Bio-SRPC?. The goal of the project is to develop and to evaluate processes and SRPC products of renewable polymers. The standard industrial PLA (Grade A) which is used in commercial applications such as packaging and textiles is PLLA with minor amounts (0-2 per cent) of D-lactic acid units. The crystallinity of this product is high and the melting temperature is in the range of 170°C. Further addition of D-lactic acid units (2-5 per cent) to this composition (Grade B) disturbs the polymer structure and reduces the crystallinity and melting temperature (120-160°C). These polymers are used commercially for melt bond applications. The D-lactic acid content can further be increased to achieve an amorphous polymer. On the other side, a pure PDLA would also have the same structure and properties as pure PLLA. Interestingly, when PDLA and PLLA are combined in equimolar amounts (Grade C), a stereo-complex structure is formed with a much stronger intermolecular interaction and therefore, a high melting temperature (220°C), E-modulus and mechanical properties (Figure 1). Although, this PLA grade is also commercially available in the market (Synbra, Futerro, Teijin), the prices are rather high.
ITA further processes the multifilaments into nonwoven, hybrid yarns like comingled and rovings, woven fabrics and non-crimp fabrics for investigating various blending methods and the different fibre orientations. Following this, these intermediate products are processes into SRPC and tested by Sirris.
Materials and processing technologies
At ITA, fibres, textiles and processing methods for SRPCs are developed using PLA. Table 1 shows properties of PLA multifilaments that are produced by Centexbel, Belgium. The filaments of two PLA grades are cut into staples fibres and blended with different methods. With these methods, various procedures for blending are investigate and different fibre orientations can be adjusted. For woven and non-crimp structures processing of monofilaments has also been investigated.
Nonwovens: The project also focuses on the manufacture of nonwoven structures composed of PLA fibre blends. Nonwovens are fabrics of non-orientated staple fibres. In this project, needle punching is used for stabilisation. The stages of the production of blended nonwoven from PLA filaments are cutting of the multifilaments, fibre blending, web laying and consolidation. The parameters of the web formation process which influence the composite properties are fibre orientation, porosity and thickness. Fibre webs with isotropic orientation are produced with the aerodynamic web forming process on the Air-laid machine at ITA. Fibre webs with unidirectional orientation are produced with a mechanical web formation process on the lab-scale card at ITA. To provide dimensional stability to the nonwoven structure, they are consolidated with the lab-scale needle punching machine LMB 6 by Dilo Machines GmbH, Eberbach, Germany. The porosity of the nonwoven is optimized by varying the thickness of the fibres and degree of consolidation. A 33 design of experiment is employed to find parameters (fibre length, needle depth, needle punches per unit area) most suitable to process the PLA fibres. The tensile properties are characterized according to the DIN EN ISO 29073 norm. Furthermore the thickness is characterized according to the DIN EN ISO 9073-2 norm and specific weight of the nonwovens is characterized according to the ISO 9073-1 norm.
Commingling: The first method for blending the PLA grades is with a commingling set-up. In this method, both components are fed simultaneously to an air jet nozzle (Figure 2). Due to the air jet, forced vibrations are initiated into the yarns. These provide a hybrid structure with a random distribution of the different components in the cross-section. This process is commercially attractive due to the higher production rates of producing blended component filaments. However, the load bearing reinforcing fibres are distributed randomly and not parallel to the yarn axis.
Rovings: PLA filaments of both grades are cut into staple fibres, blended and further processed into a sliver. On a Stirolab by Mesdan, Puegnago Sul Garda, Italy, the sliver is drawned and a low twist is inserted (Figure 3). These rovings can be used for winding.
Woven structures: Woven fabrics consist of warps (in production direction) and weft yarns (90° towards warps) that are located alternately in a certain rule above and under the warp yarns Additionally the PLA filaments are transformed into flat precomposite structures. To facilitate the formation of composite material coupons for testing, narrow fabrics are woven to small coupon plates (Dog-bone specimens). Here the fabric structures are made on narrow looms. As warp threads PLA filaments of grade A and B are alternating arranged and as weft threads PLA filaments of grade A are applied with 18 ends per inch (Figure 4).
Non-crimp structures: In addition non-crimp fabrics are produced. These fabrics consist of yarns in a 0° direction and yarns in a ? 0° direction. The structure is fixed by a sewing thread. All fabrics are tested for mechanical properties, thickness and porosity. Finally multicomponent pre-composites are thermal consolidated into SRPC plates. Afterwards the SRPC plates are further thermoformed to 3D structures by compression moulding.
Results
When cutting the filaments into staple fibres with a defined length only a low spindle frequency could be adjusted. At higher frequencies the processes was interrupted by fibre breaks as well as by wrapping of the filaments around the cutting unit.
PLA nonwovens could successfully be produced with the aerodynamic web forming process. In Figure 5, processing steps for PLA airlaid nonwoven and in Table 1 properties of fibres, needle punching and nonwovens are shown.
Grade A and grade B PLA fibres are successfully processed to yarns by commingling and to rovings by using a Stirolab. Higher yarn tenacity can be achieved using crimped fibres. Also woven structures were successfully produced (Figure 6).
When using multifilaments with a higher tenacity process stability was as good as using standard materials like polypropylene or polyamide. The PLA multifilaments have a count of 1,100 dtex for the high melting multifilaments and 600 dtex for the low melting multifilaments. The reinforcing fibre volume fraction was around 75 per cent for the high melting filaments.
Conclusion
Pre-pegs for self-reinforcing polymer composites were successfully developed at ITA from PLA filaments. The structures that have been developed are needle punched nonwovens, commingled yarns, roving yarns, woven fabrics and non-crimp fabrics. The structures are developed into composites, tested and validated by Sirris Leuven-Gent Composites Application Lab, Belgium.
The properties of the newly developed composite materials are comparable or higher than CURV, also taking into account the density of material. Moreover, since two PLA types are combined with difference melting temperatures, the material has an interesting processability, whereby a wide processing window is reached. Applications of these self-reinforced composites can be in semi-structural applications.
Finally, self-reinforced composites made from PLA are very interesting and promising materials. These new insights and knowledge were transferred to the industrial target groups and will be circulated. The positive feedback, the cooperation of the companies during the meetings of the user committee and the One-to-one meetings that were organised after the end of the project, already showed the clear interest of the companies that self-reinforced PLA technology will be used and applied in their industries.
Acknowledgement
Grateful acknowledgement goes to the research association Forschungskuratorium Textil e. V., a branch of the German Federation of Industrial Research Associations (AiF), for the financial funding ? through AiF-CORNET ? of the research project AiF-No 90 EN Bio-SRPC.
References
1.Deng, M.; Shalaby, W.; Self-reinforced ultra-high molecular weight polyethylene composites. GB 19910004781, Publication date 02.03.1995
2.Hot Compaction of Woven Poly(ethylene terephthalate) Multifilaments. Jl of Applied Polymer Science, Vol. 91, 2004.
3.Growth in PLA bioplastics: a production capacity of over 800,000 tonnes expected by 2020; NOVA-institute market study 2012.
* The authors ? Marie-Isabel Popzyk, Sangeetha Ramaswamy, Volker Niebel, Thomas Gries ? are with the RWTH Aachen University, Faculty of Mechanical Engineering, Institut für Textiltechnik of RWTH Aachen University (ITA), Aachen, Germany.
* Linde De Vriese is with Sirris Leuven-Gent Composites Application Lab, Heverlee, Belgium.
* The authors ? Kristel Beckers and Lien Van der Schueren ? work for Centexbel, Gent, Belgium.