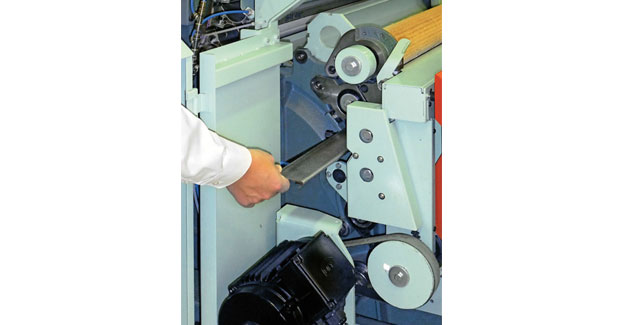
C 70 Card Smart innovations
True to the motto ´standstill is a step backwards´, a successful card model such as the C 70 will also be further improved. Further development is based on customer and market requirements as well as the technical progress of the technology and machine components.
Perfect quality of the card sliver ´ uniform batt and reduced thick places´ that is the result of the latest innovation push with the Rieter´s C 70 Card.
True to the motto ´standstill is a step backwards´, a successful card model such as the C 70 will also be further improved. Further development is based on customer and market requirements as well as the technical progress of the technology and machine components.
The basis for a successful carding system
The C 70 card is currently the most successful wide carding system. The proven system rests on three pillars:
- 1.5 m working width
- Largest active carding area ACI (Active Carding Index)
- Precision of the carding gap
The combination of these three factors is the foundation for the high production of the carding system, the quality of the yarn produced and thus also for the economic success of a spinning mill.
1.5 metre working width
All well-known card manufacturers have in the meantime completed the change from 1 m to cards with a greater working width, at least for part of their product range. A confirmation of the accuracy of the course adopted by Rieter 15 years ago. More than 7,500 C 60 and C 70 cards sold with 1.5 m working width attest to Rieter?s technological lead in modern carding.
Largest active carding area ACI
Decisive for the yarn quality on the cards is the number of the card flats in contact across the working width. The C 70 with 32 flats and 1.5 m working width has the largest active carding area and thereby differs significantly from its competitors (Fig. 1).
Precise carding gap
Decisive for the carding result is the precision of the carding gap over the whole machine width. The carding gap is set according to the production and the raw material processed. The exact tolerances and the material combination cast-iron plate with cast-iron cylinder allow an exact setting of the carding gap, that also remains constant during the production period.
New ways with batt formation
The specially-developed pressure control (patent pending) in the card chute is one of the features of the present C 70. This functions by giving a precise batt weight at the card feed, taking into account the raw materials and their characteristics. The result is a minimal variation of the batt weight and thus a lower CV-value. A convincing impression is conveyed by a comparison with the previous system which operates with a light barrier (Fig. 2). For C 70 cards already producing in the market and the last generation C 60 cards the pressure control in the card chute can be retrofitted via Rieter Parts from January 2015.
Quickly removable web bridge
Man-made fibres with strongly lubricating fibre finish or cotton with honeydew are difficult raw materials. Here the web bridge must be frequently cleaned to maintain the quality level. The solution for this time-consuming undertaking is the new web bridge (patent pending). In the shortest possible time, it can be removed, cleaned and reinstalled (Fig. 3). If there is an appropriate replacement component in the spinning mill, the downtime can be reduced to a few minutes.
The new web bridge allows a pefect, uniform web and ensures continuous operation of the card. Thick places are substantially reduced and consequently the imperfection rate improved.
Special areas of use for web application
Due to the working width, the C 70 card system is predestined for web applications. The excellent carding is demonstrated by a perfect uniformity of the resulting web.
Two major applicat