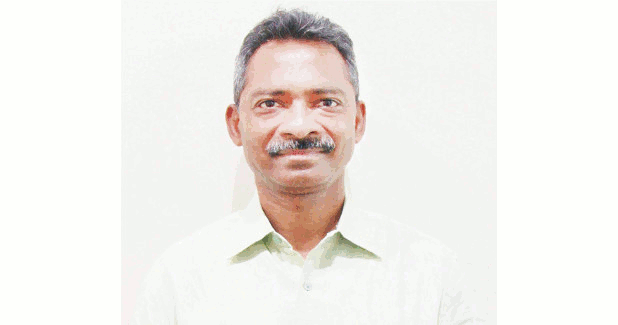
Biotech, a sustainable solution in textiles: Edward Menezes
Rossari Biotech Limited, one of India’s leading manufacturers and exporters of textile chemical auxiliaries, enzymes, polymers and animal health care products, is a brainchild of the two founding partners – Edward Menezes and Sunil Chari.
Rossari Biotech Limited, one of India’s leading manufacturers and exporters of textile chemical auxiliaries, enzymes, polymers and animal health care products, is a brainchild of the two founding partners – Edward Menezes and Sunil Chari. Edward Menezes, Director, Rossari Biotech Limited, speaks on biotechnology in textile industry, and the company’s products ranging from pre-treatment to finishing. Excerpts…
Biotechnology in textile industry. What is the global experience, and how far has it been successful in other countries? What is India’s experience so far?
Biotechnology has impacted the textiles industry through the development of more efficient and environmentally-friendly manufacturing processes, as well as enabling the design of improved textile materials. Applications of biotechnology in textile wet processing opens up a new horizon towards environmentally-friendly technology.
Biotechnology has been used in the textile industry for over 100 years, since amylase enzymes from malt extract were first used to degrade starch-based sizes for cheap and effective desizing. In the last 30 years, however, a dramatic rise in biotechnology innovations is leading to an escalating number of low-cost and effective biotechnology solutions in textiles processing. Also it leads to explore exciting new fabrics and finishes to meet the ever-changing demands of the fashion and design industry.
Application of enzymes in textile processing, novel fibre source, improvement of plant varieties for fibre production, bio-based waste management are some of the recent key developments. These are not only helping to replace harsh chemicals from wet processes but also leading industry to greener path. Similarly use of microorganisms is on the increase in the effluent treatment area however as far as India is concerned it is slowly but steadily establishing in industry.
Rossari talks about its products ranging from pre-treatment to finishing. What are the major products? And what are their unique characteristics?
We are India’s largest manufacturer of textile auxiliaries and an important partner of many textile processing industries for more than two decades owing to our customer-oriented product developments, broad, innovative product range, high level of supply capability and outstanding technical service. As an organisation, Rossari Biotech has stayed true to its philosophy of “Making you more competitive†by constantly trying to work collaboratively and ensure that our efforts lead to the betterment of our stakeholders.
We offer a comprehensive range of chemicals for pretreatment, dyeing and finishing processes of textile materials. Besides performance, we also provide sustainable solutions to help our customers to reduce their environmental impact. We increasingly provide products and process solutions to our customers which contribute to a sustainable development. Rossari is one of the leading suppliers in the Textile industry who provides a unique combination of sustainable chemistry and biotechnology products.
Our dedicated Green Series products offer better textile processing solution to textile industry. These not only perform as per customer needs but also help to reduce utility consumption viz. time, water, energy which means more sustainable textile processing.
E.g. Our Greensoda series helps to overcome TDS related problems during dyeing where as Greenboost offers eco-friendly pretreatment. Greenhydro 400 Pdr. eliminates disadvantages of Hydrosulphite and Caustic soda in polyester dyeing. Greenacid is now generic name in textile processing due to high reduction in BOD and COD. What are the various facilities of Rossari for servicing the Indian textile industry? A brief account of its journey in India – from beginning to till today.
We started as the manufacturer of textile chemicals including pretreatment, dyeing and finishing. Throughout these years of development, we have increased our product range from textile chemicals to other chemicals of various industries like animal health nutrition, polymer and cleaning chemicals.
In keeping with our company policy for technology development and deployment we have extensively invested in ultra modern R&D facilities located at head office in Mumbai and at our Plant in Silvassa with over 1,40,000 MT per annum capacity.
Manufacturing facility is well equipped with reactors of various capacities 1KL to 16 KL, advanced packaging machines, huge storage area. These facilities makes it possible for us to have a vast store of application and technical know how that is regularly accessed by our clientele as well, imparting clear edge in the market place.
We produce world class textile chemicals in the most efficient and environmental friendly way which satisfies our customers and empowers our suppliers and employees. Despite our growth, we have remained steadfast in our commitment to provide high-quality, cost-competitive products. We deliver our products and services with speed and agility that is often unmatched by MNC manufacturers. As leaders at the forefront of our industry, we are also dedicated to providing innovative technology and solutions. Our state-of-the-art research capabilities allow our customers to meet the demands of today and create the products of tomorrow. Our ability to deliver innovative products in a very short time from idea to market has catapulted us as the number one supplier in India today.
At a time when sustainability is growing stronger day by day, how do you think biotech can contribute to this movement through Rossari?
The use of biotechnology in the textile chemical processing is rapidly gaining global recognition because of their non-toxic and eco-friendly characteristics with the increasingly important requirements for textile manufacturers to reduce pollution in textile production. At Rossari, we are constantly working to provide a sustainable solution to the industry.
Cellulase based products have now substituted pumice stones in the garment washing process and prevents the damage to washing machine and garment. It also eliminates the need for disposal problem of stones and improves the quality of wastewater. Bioscouring enzymes work under mild conditions, save water and reduce BOD and COD drastically. Enzyme based soaping off process has opened up a new field for the development of soaping process. These removes unfixed dye in the dye and dye hydrolysis during soaping and improves fastness index than traditional soaping. Also it can help to reduce soaping time, amount of sewage discharge and cost of wastewater treatment.
Denim bleaching with Laccase enzymes has provided new dimension to bleaching process where it has made it possible to get rid off the chlorine-based bleaching process. Also with this system, the process is very much controlled than hypochlorite. Traditional alkali deweighting causes enormous damage to the environment due to wastewater with heavy chemicals in the effluent. Esterase treatment can provide a clean and efficient way for polyester modification with much-improved fabric wicking, as well as greatly improved oily stain removal performance.
Today, in many cases immobilised enzymes have revealed highly efficient for commercial uses. Compared to free enzymes in solution, immobilised enzymes are more robust and more resistant to environmental changes. More importantly, the heterogeneity of the immobilised enzyme systems allows easy recovery of both enzymes and products, multiple re-uses of enzymes, continuous operation of enzymatic processes.
Hybrid enzymes are designed to improve or alter the enzymological properties and/or increase purity and yield. Various novel enzymes are now been used in biofinishing of textile substrate like wool, nylon, polyacrylonitrile. Biological decolorisation is now the most common and widespread technique used in textile effluent treatment. The ligninolytic enzymes like lignin peroxidase, manganese peroxidase, and laccase are now used as an alternative to the conventional effluent treatments. They are able to oxidize a large number of different compounds, and therefore they have been intensively used in the textile wastewater treatment. Such solutions can offer complete destruction of the dyestuff, with a co-reduction in BOD (Biochemical Oxygen Demand) and COD.
Apart from the domestic market, has Rossari developed export markets also? If so, give us some details.
Export market demands sustainable products and we are one of the best brand in it. Because of this it was easy for us to enter global market. In Bangladesh we are among top suppliers of textile chemicals. With strong field team we are able to establish our self with small span of time. Beside this we have extended our footprint beyond India in Pakistan, Sri Lasnka, Singapore, Thailand, Latin-Central America, Egypt, Vietnam, Turkey, Mauritius and other global countries. With the help of a dedicated export team we are expanding Rossari’s reach globally. Our distributors are locals, meaning they know their home market and how to use our products in specific product types.
What is the scope of biotech for Rossari? What are the future plans – expansion and diversification?
Since 1997 We are engaged in continuous improvement of products and processes to enhance the quality of production and cost competitiveness in order to build value for our customers. In keeping with our company policy for technology development and deployment we have extensively invested in ultra modern Biotech R & D facilities located at head office in Mumbai and at our Plant in Silvassa. Our organization has been conferred with R & D recognition from the Government of India for in-house research and development units at Mumbai and Silvassa. We are also associated with various Government funding agency like BIPP, BIRAC, TIFAC for various Industry oriented biotechnology related projects.
Techniques and experience achieved with such projects helped us develop infrastructure at our factory. And now we have purchased new land in Gujarat where we have planned to set up plant dedicated to bioproducts like enzymes. Huge fermenters with capacity of 10 KL 50 KL will be installed to manufacture bioproducts with developed techniques during projects. Speciality enzymes like serratiopeptidase, Bromelain, Papain are also planned to manufacture for their use in Pharma industry. Our knowledge of Biotechnology is being used to revive the environmental trend in textile processing and we will continue to work harder.
In this time of globalisation and also while India is experiencing a revival of textile industry, what are your suggestions to the industry and the Government to promote biotech for the benefit of textile industry?
Biotechnology implementation and ‘Business’ are not words that have typically gone together. Its a costly venture from manufacturing point view as well as application. Due to which many SMEs hesitate to enter in it. Financial encouragement from government will be highly appreciated. More Industry and academic collaborative work in the form of funded projects. This will not only help to develop new technology but also create skilled manpower who take such technology further on commercial scale.