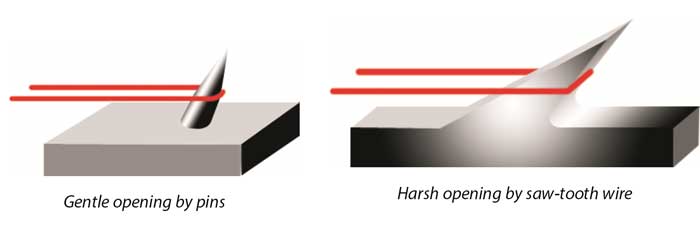
Basant’s Advanced Solutions for Spinning Recycled Yarns
Basant has focused on developing Gentle Fibre Opening Solutions to achieve high quality yarns from short and trashy fibres, while improving production and reducing process waste.
In the current market conditions, spinners are increasingly using recycled fibres both to reduce their cost of production and to meet the market demand for recycled fibres. But the challenges are many – high trash and micro-dust, short staple length, inconsistent fibre mix, fibre rupture during the waste tearing and fibre preparation processes, high level of contamination, among others. After extensive research and experiments, Basant concluded that the best way to address all these problems is to ensure better opening and cleaning while ensuring minimum damage to the already weakened fibres during the process of fibre reclamation and spinning.
Basant Fibertek enjoys a 60 years old chequered history as a market leader and innovator in pins and pinned products for textile spinning and recycling. Given the enormous opportunities and challenges in recycling textile waste, Basant has focused on developing Gentle Fibre Opening Solutions to achieve high quality yarns from short and trashy fibres, while improving production and reducing process waste. Through its expertise, Basant has been able to resolve many challenges for recyclers and spinners by designing custom solutions using the Gentle Opening Action of Basant Pins.
Choice of machine clothing
The above graphic will illustrate how pins provide gentle opening action as compared to the harsh action by saw-tooth wire. Pins have a smooth spherical ball-point tip which imparts a very gentle opening or untangling action on the waste or fibres, thus minimizing rupture. In contrast, the knife edge of sawtooth wire initiates a cutting action to open the fibres, thus rupturing them and thereby generating not only a lot of dust but also shorter and weaker fibres.
The main principle adopted by Basant is to prevent further weakening of already weak recycled fibres in order to produce a better quality yarn at higher productivity. Another very significant advantage of pins is that it provides a de-dusting action to the fibres (similar to slapping your fingers on a dusty cloth), enabling the trash and dust to be easily separated from the fibres.
Basant has provided solutions to a wide range of waste recycling and recycled fibre spinning – be it recycled cotton from pre or post consumer waste, recycled polyester or other synthetic fibres, recycled PET fibres, silk, wool, linen or acrylic fibres or regenerated synthetic fibres. Each mill has its unique challenges, depending upon the machinery available, machinery condition, fibre mix used, yarn counts produced, and quality parameters. Hence, it is important to audit the process before designing solutions and then to handhold the client through the trials and validation. Besides product design, optimization of machine settings is critical in achieving the desired improvement in quality and productivity. Since most recycled yarns are produced through the open-end spinning process, Basant has developed solutions for the whole value chain, including waste tearing, fibre preparation and rotor spinning. We shall breifly describe what we do in each of these processes:
Waste recycling
In the Tearing Machines, the reclaiming of fibres needs to be done in a gradual and gentle process to minimize fibre damage, while ensuring good opening. This is achieved by carefully designing the pin population in each cylinder and ensuring proper cylinder speed and gauge setting. Pins also give a very long life when compared to wire because the ball shaped tip wears out slowly and forms a new tip as the pin length reduces, since wear is happening all around the tip. In contrast, the knife edge of wire becomes blunt very rapidly and the opening action reduces rapidly. Our lags have successfully opened yarn waste, rags, carpet waste, jeans and other clothes, laminated felts and other forms of textile and nonwoven waste. The optimized heat treatment of Pins ensures long life whereby the pins don’t break or bend easily due to high load of waste material and contaminants. Many international recyclers and OEMs are our clients. We have developed a proprietary design named Excalibur Lags, wherein the design ensures no pins fall out from the lags during operation.
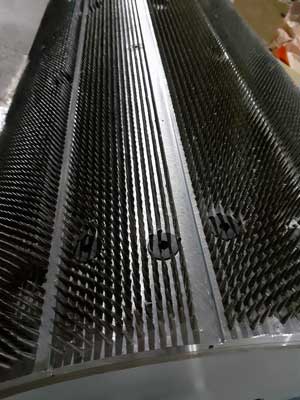
Pinned cylinder
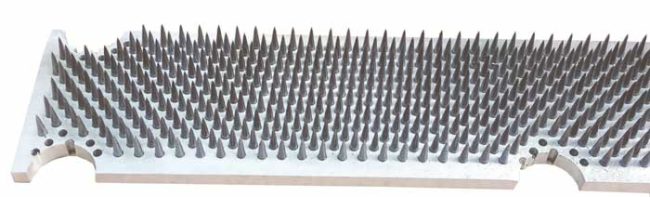
Pinned lags

Excalibur lag
Fibre preparatory
Beaters in the Blowroom and Chutefeed, as well as the Card Licker-in, play a crucial role in achieving a high quality of well-opened, clean and strong card sliver, the basis of producing a good yarn. Using the right design of Pinned Beaters and Licker-ins ensures a consistent quality of well opened and cleaned sliver as well as lower fibre waste. The higher the opening efficiency, lower is the waste, lower is the sliver trash, better is the yarn strength and the more and less ruptures are the fibres, lower will be the Neps in the yarn produced. A strong and lower neps sliver also ensures lower breaks during the spinning process and lower cuts at winder, thus further improving production and reducing waste. Basant advises most clients, who are facing challenges in their spinning, to focus on optimizing their fibre preparation to minimize their problems at the spinning stage.
Basant designs the pin pattern in their Beaters as per the demands of the raw material mix used in the process. Factors like pin diameter, pin population, pin angle, pin height and pin hardness have a role to play in achieving the optimum results. Through Basant’s extensive experience over many decades and execution of numerous successful projects, the company has mastered the art of designing gentle fibre opening solutions. They have more than 15-25 pin patterns developed for each type of Pinned Roller to specifically meet certain process requirements. Hence, they can provide guaranteed solutions for virtually any type of fibres and for any count (Ne) of yarn.
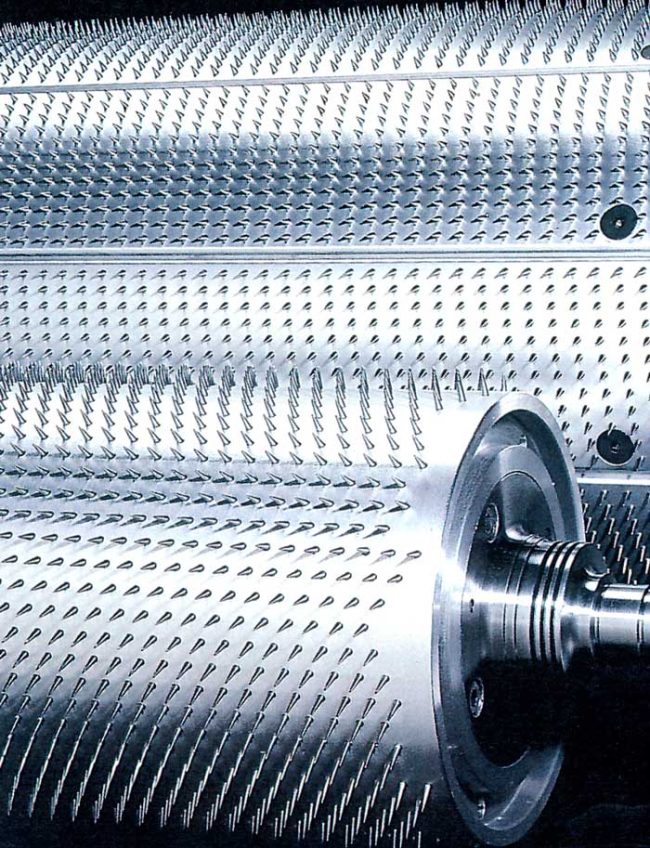
Pinned beater
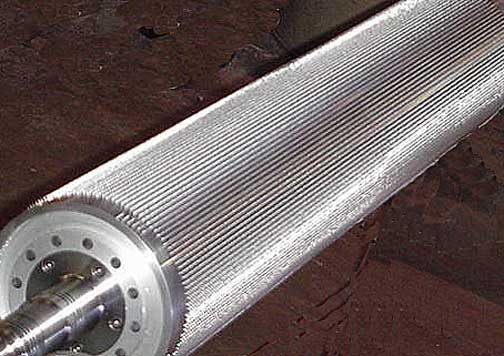
Pinned licker-in
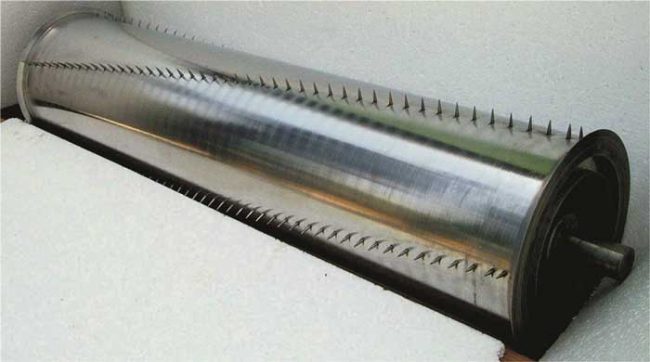
Chute feed roller
Open-end spinning
Basant has always believed in providing cutting edge technology solutions and many options to our clients, such that they can get optimum results in both quality and productivity at an economical cost. Recycled or regenerated fibres tend to be highly abrasive. This reduces the life of the clothing of the Opening Rollers as well as presents a stiff challenge in achieving good, consistent fibre opening.
Basant has addressed these challenges by developing and providing a wide range of opening rollers & clothing rings as well as rotors for all leading makes and latest models of rotor spinning machines and to serve any kind of requirement of to their clients. A wide range of high-performance hard coatings are available to achieve the best price to performance ratio in the highly competitive Rotor Spinning market for the clients. The company has developed several innovative designs and introduced many new-age cost effective coatings for this purpose. Basant has advised its clients on the selection of the right type of clothing (wire as well as pins) and coating for the opening rollers and also the right diameter and groove of Rotors. The company also offers opening rollers with the patented, hard coated clothing that’s very well received by the market.
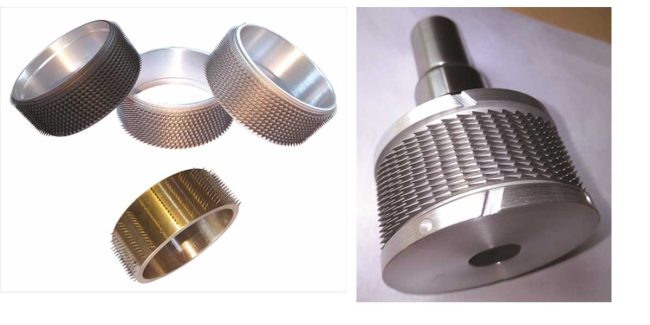
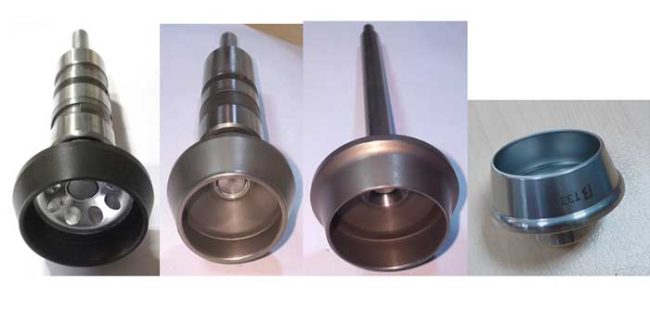
Basant takes pride in their ability to meet the challenges their clients face when producing recycled yarns and in their focus on promoting the recycling and circularity of textiles by introducing viable technological options to achieve the desired quality and cost parameters required for this initiative to scale and prevent the increasing problem of waste dumping. Basant is committed to contribute towards building a sustainable world and thereby a better future for humanity.