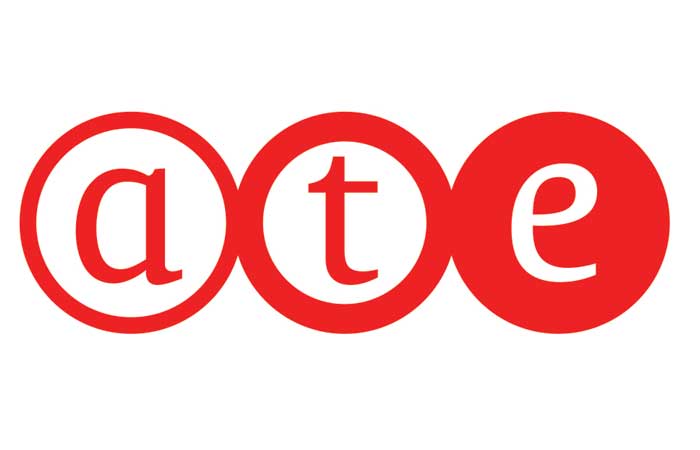
Balkan Tearing Line Converting textile waste into value
The final output of Balkan’s tearing lines is bales of highly processable fibre.
Trützschler & Balkan Textile Machinery has collaborated to become the first full-service provider in spinning preparation for recycling of textile waste.
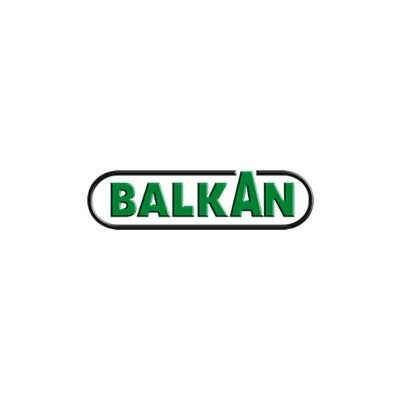
Textile Hard Waste
This waste is collected from various sources as listed below:
- Households: Used clothes
- Retailers and brands: Unsold inventory, defective and returned items
- Manufacturing and production: Scraps, offcuts, and defective products from textile factories and garment manufacturers
- Hospitals and hotels: Used uniforms, bed linens, towels, and other textile products
- Recycling centres and donation bins: Non-profit organisations, charities, and recycling companies have established designated collection sites where individuals can conveniently dispose of unwanted textiles
- Special events and drives: Organised events specifically for collecting textiles for recycling or repurposing
- Second-hand stores and thrift shops: Items that are not sold or are deemed unsellable
- Commercial and industrial sources: Textiles from businesses such as restaurants, gyms, and spas
Balkan machines are renowned for their high-efficiency performance in cutting, blending, and shredding textile hard waste to create fibre tufts, which are subsequently compressed into bales of secondary fibres.
Process & machine flow guide

Guillotine Cutters: The first stage involves the cutting of the textile hard waste, where the raw material is cut into small fabric pieces using two guillotine cutters. The first cutter DTA61 is fitted with a metal detector, while the second cutter DTA62 is positioned at a 90° angle to ensure consistent fabric pieces are produced.

MAGNET – B69: This machine contains 252 neodymium magnets. It is capable of effectively separating heavy parts such as unopened clips, fibres, buttons, and zippers.
Pipe Lubrication System – B84: The stainless-steel tank is equipped with a pump that has a spray capacity of 70 litres per hour, with a storage capacity of 750 litres.
Boxroom – DT82: This advanced “Blending Bin System” is highly suitable for the blending of various staple fibres such as cotton, polyester, and RG fibres with recycled fibre. It ensures a uniform blend, which enhances the quality of mixing parameters. The blending bins have a storage capacity of up to 3000 kg, depending on their size. The multiple blending bins allow for continuous feeding and processing of various blends, significantly reducing material mix change stoppages.
Feeding Unit – DT71: The cutting material is sourced from the DT82 boxroom via the DT90 fan. The feeding unit facilitates the consistent and uninterrupted supply of the cutting material to the tearing machine.
Mega Tearing – DTB 30: The feeding unit DT71 supplies the cut material to the tearing line DTB 30. This machine is equipped with 6 cylinders, each with an increasing number of needle pins, which gradually open the textile hard waste into fibre tufts. The speeds and distances can be adjusted according to the material being processed. After passing through the tearing machine, the fibre tufts are then extracted and compressed into bales using a bale press.
Super Thread Separator B53 with Feeding Unit B31: The feeding unit B31 supplies fibres to the mega-tearing machine, where they are then separated by B53 into unopened parts and small parts. The small parts are gathered in the filter bag, while the unopened fibres can be recycled back into the tearing line DTB 30. As a result, B53 effectively conserves raw materials and minimises waste.
Condenser B26 and Bale Press SDT251: The B26 condenser facilitates the transfer of material from the preceding machine to the subsequent machine while simultaneously removing dust from the fibre. SDT251 will compress 6 bales per hour, weighing 220-230 kg each.
The final output of Balkan’s tearing lines is bales of highly processable fibre. These fibres can be seamlessly incorporated into the yarn production process using Trützschler machines. Customers can thus benefit from a well-calibrated, reliable, and consistent operation.
With this combined machinery expertise and technological know-how, our customers can produce yarns of the highest quality and effectively convert waste into value. Together we can make a significant impact on addressing the critical issue of textile waste on a global scale.
To know more, contact:
A.T.E. Enterprises
Tel: +91-22-6676 6100
Email id: spinning@ategroup.com
Website: www.ategroup.com
(Communication provided by the management of the company)