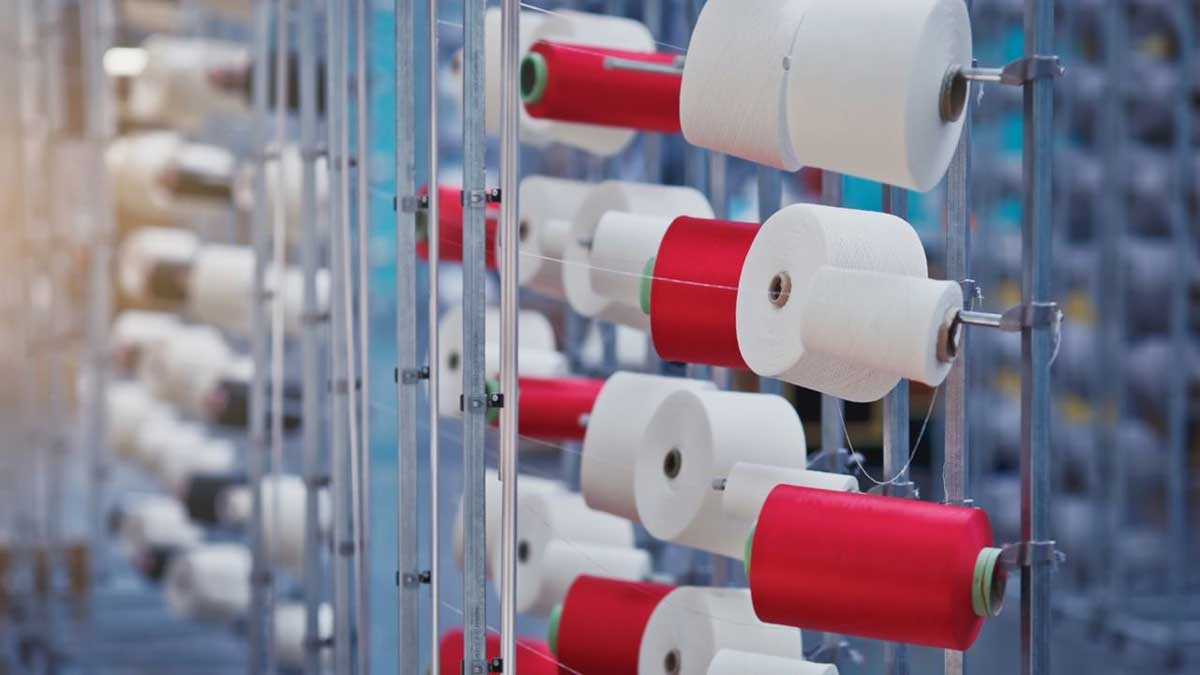
Automated textile evolution
Amidst volatile raw material costs, shifting market trends, workforce scarcity, and intense global competition, Divya Shetty examines how automation is emerging as the key solution to address these challenges both presently and in the future.
The textile sector is amongst the most energy-intensive industries globally, with energy expenses constituting a substantial portion of its production outlay. The industry is facing several challenges, like the adoption of automation technology, sustainability and waste reduction, quality control and consistency, and adaptability to market uncertainties. However, with the emergence of automation and advances in technology, textile manufacturers are now able to cut costs and consume less energy.
“Automation has a proven track record of making operations productive and efficient. It not only transforms complex, repetitive tasks into streamlined operations, but also helps to reduce waste and make manufacturing operations more sustainable. This leads to better-quality products and improved safety for workers as well. All in all, automation can overcome uncertainties and make the textile industry future-proof,” says Praveen Vaidya, Head – Automation Engineering, Competence and Development Centre, Manager – Key Accounts, B&R Industrial Automation.
Automation enables real-time data monitoring and analytics and can help forecast demand and optimise inventory management. By integrated automation technologies, the Indian textile industry can enhance its competitiveness in the global market and mitigate the challenges associated with mentioned uncertainties effectively. Automation undoubtedly increases productivity by streamlining workflows, largely reducing errors. By minimising manual operations, it enhances operational efficiency. Automation optimises resource utilisation, reducing losses due to inefficiencies.
“Automation lends itself to support textile manufacturers to achieve quick turnarounds thus becoming very responsive to market requirements within the supply-chain. Repetitive work is very well suited for automation offering high quality, timely supplies year in, year out. Stäubli is very active with automation solutions in India,” Fritz Legler, Textile Marketing Officer, Stäubli.
Key technologies driving automation
Industry 4.0, also known as the fourth industrial revolution, is fundamentally changing the landscape of textile manufacturing by introducing advanced technologies and digitalisation across the entire production process. Industry 4.0 enables the development of smart factories where interconnected machines, sensors and device communications collaborate with each other in real time.
“Many industries have already implemented Industry 4.0 solutions, and the textile industry is also reaping its benefits. When we talk about automation and robots, they are increasingly used for tasks such as cutting, stitching, and material handling. They improve efficiency, reduce labour costs, and advance product consistency. Using IoT, data from various levels of operations is collected to control and take the right decisions, and this also helps in predictive maintenance of the systems, improving their overall performance,” explains Vaidya.
Industry 4.0 technologies such as AI, IOT networks and robotics are revolutionising textile manufacturing by enhancing efficiency, flexibility and quality. AI-driven predictive analytics optimise production processes, OTT networks enable real-time monitoring with control. Robotics automate repetitive tasks, reducing labour costs and improving precision. These advancements help in data-driven decision making, enabling the textile manufacturers to adapt to the changing market demands swiftly while making competitiveness.
“Textile manufacturers can leverage data analytics and AI to optimise production efficiency, predict equipment failures, improve product quality, and identify opportunities for process optimisation. Automation and robotics play a central role in Industry 4.0 by automating repetitive and labour-intensive tasks in textile manufacturing with minimised flaws. Digitalisation creates virtual replica of physical manufacturing systems and process, allowing textile manufacturers to simulate, monitor and optimise production in real-time. Overall, Industry 4.0 is revolutionising the textile manufacturing industry by driving digital transformation, increasing automation, enhancing efficiency and productivity, improving product quality, and enabling greater flexibility and customisation to meet the demand of today’s rapidly evolving market,” states Ashok Juneja, the Director of Sales & Service, Saurer Textile Solutions.
One of the most important elements in industry 4.0 is Artificial Intelligence (AI). AI helps predictive maintenance anticipates equipment failures, reducing downtime and saving on maintenance costs. By analysing sensor data, AI predicts the material requirement for maintenance, preventive cost.
IoT implementation into textile manufacturing process is somehow becoming a standard nowadays due to fast adaptation of requisite customer demands, also in case of certain customised solutions etc.
In order to stay ahead in this competitive market, companies are incorporating all these driving technologies. “Luwa offers the integration of IoT technology into its products and solutions, enabling real-time monitoring, data analysis, and remote support for our clients. The Digital Solutions technologies not only support operational efficiency but also facilitate predictive maintenance and productivity improvements, aligning with the latest industry trends,” comments Ulf Mattisson, CEO, Luwa Group.
“Benninger is coming up with the BEN-Cloud customer portal. This will significantly simplify communication between customers and After Sales, provide a 360° view of all relevant information and, for the first time, offer e-shop and IoT / Industry 4.0 functionalities. At present we are finetuning the system for a future release,” informs Rolf Erik Schoeler, Global Head of Sales and Marketing, Benninger Group.
In a nutshell, the future trends for automation in textile industry are very promising with substantial growth into various applications right from understanding the market needs and delivery the adequate requirement within least timespan. It can be foreseen gradually becoming as a standard with increased integration into various segments of textile industry.
Supply chain optimisation
Businesses nowadays can use warehousing and AI-driven inventory optimisation to look at past data and predict things like what clients might buy and when they might buy it. This is why textile manufacturers need enterprise software that covers everything.
When they can see all their data in one place, businesses can figure out smart things like how to market their products better, decide on deals and discounts, and tweak prices. Having these tools helps companies plan out how much stock they need and makes their whole supply chain run smoother, which means more money in the bank.
Challenges and opportunities
Although automation presents numerous advantages to the textile market, there are several challenges to integrating it, such as;
Insufficient capital investment: The initial expenses associated with automation, such as acquiring machinery, integrating software systems, and training staff, can be massive. This upfront investment might present a challenge for small and medium-sized enterprises (SMEs) with restricted capital resources. Additionally, integrating advanced technology in textile factories involves varying expenses, from installing affordable sensors on existing machines to purchasing specialized equipment with Industry 4.0 integrations. Despite these options, industry leaders often hesitate to invest due to doubts about the potential benefits. Moreover, a lack of skilled workers in the textile field can hinder the effective use of these technologies. Even if individuals possess the necessary skills to operate advanced technology, they may resist change or find the transition challenging.
Lack of training: Despite the thriving textile industry, training facilities for advanced technology are insufficient, hindering industry growth. Some textile factories don’t reward employees based on performance, which demotivates them. Additionally, there are limited training programs geared towards advanced textile technology, leaving employees with inadequate skills and proficiency. This lack of specialized training prevents them from embracing new technologies and adapting to industry advancements.
Uncertain market: Post pandemic, the textile industry is witnessing a lot of ups and down leaving manufacturers in dismay whether to invest in advanced technologies or not. Juneja adds, “Presently, the Indian textile spinning industry is facing uncertainty due to fluctuating raw material costs, evolving market demand, and global competition.”
However, just as every coin has two sides, automation also presents opportunities to the textile industry.
Increased productivity: In the textile industry, each product requires specific machine operations. “Tasks that are complex and repetitive in nature can be easily transformed using automation systems. This helps in reducing manual errors, which are major causes of material waste and insufficient quality. Automatic machines outperform humans in many processes, boosting productivity and minimising material waste,” informs Vaidya.
Less reliance on human labour: The Indian textile industry, like many others, perceives the shortage of skilled labour as the primary impediment to India’s ascension as a global textile leader, impacting production timelines and quality. However, with the advent of automation, manufacturers are increasingly dependent on it, particularly for executing repetitive tasks. “Sources for errors coming from manual labour are eliminated; resp. labour can be upgraded to levels where automation does not render positive results. Automation is actually a panacea for lack of skilled labour becoming more and more a burden within our industry,” opines Legler.
Reduction in operational cost: With automated machinery and systems, tasks that were previously done manually can be completed faster and with greater precision. This reduces labor costs, as fewer workers are needed to operate the equipment. Additionally, automation can optimize resource utilization, such as energy and materials, further driving down production expenses.
Emerging automation trends
The textile industry will undergo a significant transformation thanks to upcoming automation technologies. These advancements will streamline production, increase productivity, and satisfy changing market needs. Some key trends include; advanced robots, integration with the IoT, AI, machine learning, automated quality control, energy-efficient technologies, connection with supply chain technologies like RFID tagging and ERP systems As automation progresses in this industry, it will become more connected, intelligent, and responsive, fostering innovation, effectiveness, and global competitiveness.
In the future, automation will transform the textile industry by enabling advanced apparel production through energy-efficient and fast processes using Computer-Aided Programming (CAP). Additionally, artificial intelligence (AI) and machine learning algorithms will be further integrated for proactive maintenance and quality assurance. Collaborative robots (Cobots) will play a larger part in working with human operators, enhancing both efficiency and safety. Advanced sensing technologies will allow for more accurate material handling. Sustainability will remain a focus, with automation playing a crucial role in reducing energy use, waste, and environmental impacts throughout the textile production process.