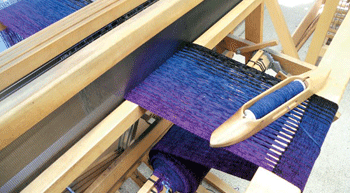
Art of weaving: The inevitable paradigm shift
The practice of weaving traces back to the Neolithic period and even before the actual process of weaving was discovered, the fundamental principle of weaving had been applied to interlace branches and twigs to produce fences, shelters and baskets for protection.
The practice of weaving traces back to the Neolithic period and even before the actual process of weaving was discovered, the fundamental principle of weaving had been applied to interlace branches and twigs to produce fences, shelters and baskets for protection. Plaited arrangements of fibres and narrow parts of plants, blades of grass, feathered palm leaves, split stalk of plants were used as the fabric, in earlier days, to protect humans from adverse ambient conditions. The earliest evidence of weaving dates back to the Egyptian civilisation and the process has undergone a phenomenal change in terms of process and machines used for making fabrics.
Fabric formation essentially involves the conversion of fibres or yarns into two or three dimensional structures using any one of the processes from weaving, knitting, braiding, lace making, netting and lately through what is called nonwoven processes. Today, there are a range of looms available for making fabrics of different sorts, right from the simplest handloom to the most sophisticated air-jet looms.Handloom weaving which is very ancient, requires a very skilled workforce and it takes anything from an hour to weeks to produce one square meter of fabric, depending on design and the delicateness of fabric desired. Notwithstanding this low productivity, many of the traditional fabrics are produced using handlooms even today. India there are 2.4 million handlooms, engaged in manufacturing of traditional items.Very low productivity due to very weft insertion rates, coupled with a shortage of skilled labour makes the handloom process very unattractive.In spite of these odds, handlooms will find their niche and the government is doing its best to protect the cultural and ethnic values with GI tagging.
The invention of the fly shuttle in 1733 by John Kay, was an important milestone in improving productivity.Later, mechanisation of the primary motions of the loom led to further improvement in productivity.
A major breakthrough in weaving was the introduction of a unique method of selecting warp yarns for shedding designed by J.M. Jacquard in 1801. In the 1830s, there were as many as 100,000 shuttle looms operating in England alone, all driven by electric engines. Subsequent innovations focused on automation to reduce the dependence on manual labour, less stoppage, production of novel designs and development of newer fabric formation techniques. The shedding and beat up operations in the loom have undergone limited changes, while the picking mechanisms has witnessed disruptive innovations, leading to improvement in productivity and quality; from using heavy shuttles to light weight projectiles to the weightless air-assisted weft insertions, i.e. shuttleless looms. Development of shuttleless weaving machines assumes the sequence in the order of projectile, rapier, air-jet, water-jet and multiphase weaving.
Projectile looms, commercialised in 1950s, though able to produce all type of fabrics up to 10m wide, are slowly being used increasingly in the manufacture of technical textiles.Rapier looms can produce all types of fabrics including multi-coloured fabrics with up to 16 colours and types of weft. Air-jet weaving today is very popular for weaving cotton fabrics, with weft insertion rates up to 2500 meters per minute.Water jet weaving machines, made with stainless steel to avoid rusting of components, use low energy per pick compared to other weaving techniques, are effectively used for synthetic yarns. Multiphase weaving machines, introduced to achieve very high weft insertion rate up to 3500 meter per minute finds limited applications.Today´s weaving machines are capable of producing almost all varieties of fabrics, of widths up to 10m with computer controlled shedding assisted by digital image processing techniques that can rapidly produce new designs.
Modern weaving machines are designed and produced with online monitoring systems, linked to a co