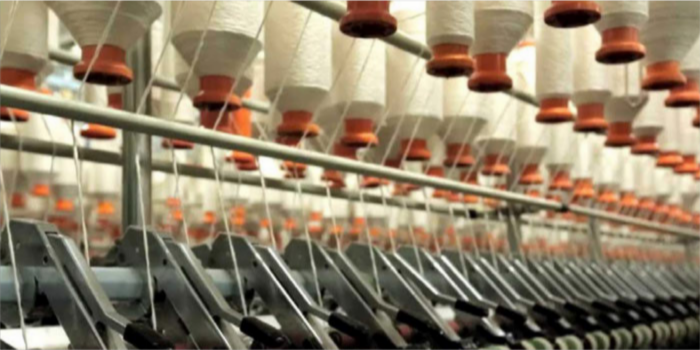
Approaches for cleaner production in spinning mills
This article from Jeyaraman Anandha Kumar emphasises the environmental effects of textiles in detail and contributes to cleaner production and sustainability in the textile spinning industry.
This article from Jeyaraman Anandha Kumar emphasises the environmental effects of textiles in detail and contributes to cleaner production and sustainability in the textile spinning industry.
Spinning is a vital operation process that consumes more power and massive investment. Unlike other industrial segments, spinning mills are a big concern due to the moderate net profit of 5 per cent. The primary export of yarn to neighboring countries has seamlessly reduced the profitability in recent times. The price determination of world cotton is dependent on cotton sourcing whereby the type of single dependency occurs for a secured source, and it seems a big threat for the spinning sector. It must reassure the diversified source and sustainable robust growth in order to avoid direct collapse of the total textile supply chain if it lacks the above sources. Such a competitive price and so challenges increase in the mills to produce quality yarn using average cotton. Perhaps finding out the cotton import arena and their capacity utilisation can bring a great deal of success. Despite that, inadequate gas supply due to unavailability of gas mills or captive generators, production cost per unit and the cost for alternative sources of power are driving up even higher. Originally, sustainable business relies on the increase in profitability with respect to quality tasks, consistency, and fast supply of products.
The extraordinary expansion of the global economy in recent years has also caused the explosion in consumption. While some of this growth in consumption is necessary for people to continue their lives, the rest is not. Like richness, consumption is also showing uneven distribution. Even though consumption of per person has risen in large areas of the world, these increases are not the same for everybody, and the differences between the increases are huge. Today, the expenditures of 100 million people living in industrially developed regions correspond to the consumption of more than one billion people living in underdeveloped regions of the world, just to meet fundamental requirements. This case is problematic because it has two contradictory appearances and both of them put great pressure on the global environment.[1]
Advanced production technologies, which are used to meet increased consumption demands, have also made production activities important to the global environment. The developing technology brought about the problems like pollution of the environment, air, and water, thinning of the ozone layer, a decrease of green areas. In response, however, a public opinion has emerged, especially in developed countries that are sensitive to these problems. New precautions have begun to be considered both to maintain industrialisation and to protect the environment. It has been shown that cleaning up after the pollution is more costly than cleaning up before the pollution, and it is not possible to restore the degraded ecological balance after pollution.[2]
Along with the technological developments in recent years, developments in the textile sector as well as in many sectors have played a major role in the increase of environmental problems. The main environmental impact in the textile industry is manifested by the discharge of high amounts of chemical loads into the receiving environment. Other important elements are high chemical and water use, energy consumption, air pollution, solid waste and odor formation.
Environmental issues related to textile and garment sector; it starts with drugs that are used in the cultivation of natural fibres and the emissions in the production of synthetic fibres. From this moment on, a series of processes are being carried out in which thousands of different chemicals, tons of water and considerable amount of energy are used to treat the fibres to reach the final textile product. In this review study, the environmental problems that textile has emerged have been examined and it has been explained that solutions for the problems can be made within the scope of sustainability and cleaner production. The concept of cleaner production has also been discussed in detail and the relationship with sustainability has been put forward.[3]
Following steps to be followed for betterment of spinning processes:
Process optimisation: Continuous improvement in productivity level, quality, utilisation and yarn realisation is very important for efficient working of operations. Optimisation of process can be done after proper analysis of processes. Due to poor process engineering at preparatory processes and adverse conditions of humidification plant, to be imparted in ring frame for better working performance. Step by step action plan is required for optimisation of processes from blowroom to ring frame.Machine and process settings are required to be fine-tuned, so as to match with required quality level with controlled wastage. Technology like roving individual monitoring system helps in controlling waste level in terms of less fly generation and less pneumafil waste.
Technological upgradation: Rapid improvement has been done by textile machine manufacturers to simplify the work practices and to achieve higher productivity level. Few technologies can also be implemented in old machinery as well. Selection of right technology for the product is very essential to gain maximum output. Up gradation in technology helps in reducing man power, increase productivity, lower power consumption, and lesser maintenance cost etc. Manufacturing of special yarn requires retrofit arrangement, additional attachment, sourcing of material etc. which needs proper planning and execution. With the help of upgraded technology, new product can be efficiently manufactured on old machinery as well.
System and processes: Extensively labor is involved in different processes of textile industries. Developing system and follow them perfectly is the biggest task. Many industries are following traditional systems over the years and struggles to retain them. Standard operating procedures (SOP) must be followed regularly in such a manner to maintain productivity and make processes more efficient. Regular monitoring of current processes and establishing new systems as per current requirement is very essential to seal the gap. Bypassing of systems and rules create hurdle in maintaining standardisation of the process. Time to time audits can help in cross checking systems and processes.
Power saving: Many steps can be initiated for improving power cost by smart engineering. Based on analysis of individual machinery or plant, corrective actions can be initiated to improve power consumption. High efficient bearings with suitable grease used for smooth running of shafts to reduce load on motors. Timing belts, Servo drive or Variable frequency drive, modified circuits, etc. has been developed and successfully implemented in many spinning industry to reduce power consumption. Humidification plant also contains large scope of improvement by regular checking of compressed air pipeline, supply air and return air maintenance.
Corrective actions can be initiated after identifying the area of scope. Further, power cost factor has been taken in consideration and mechanical mechanism has been modified with electronic and electrical system controlled by Programmable logic controller (PLC) for new machines. Scope of power saving increased drastically with latest technology. Machine manufacturers are also providing separate kits for power saving purpose.
IT focus: Centralised data monitoring system not only helps in making database of the processes, it helps in achieving higher efficiency and improved quality of production by regular tracing. Management Information System (MIS) and Enterprise Resource Planning (ERP) are widely used monitoring system for spinning industries. Data monitoring at regular interval helps in quick identification of trouble creating part and rectify the same at the earliest. More data collection helps management in decision making for continuous improvement and value addition.
Skill development: Right skills for the right operations are very essential for effective utilisation of man power. Sorting in maxing, sliver and waste handling in preparatory, cleaning of machines, and creeling of material in different stages, piecing in ring spinning, gaiting and doffing in ring frame. These type of practices must be trained to workers for better handling of machine operations and functions. Class room training and field training of workers in order to enhance skill level of the operators. Do’s and Don’ts must be trained to workers for reducing human errors. Achieving Operational Excellence in textile industry has become imperative to sustain the growth India has achieved. It is a path in which organisations continually develop and evolve to deliver extraordinary performance in its operations and management thus leading it on a path to success.
Cleaner production
The concept of cleaner production, which is often used, has evolved into the concept of sustainable production in the last 10 years in order to prevent possible future bigger catastrophes. Sustainable production has become widespread with the cleaner production concept used by many organisations. Cleaner production has been applied as for production processes; protection of raw materials and energy, removal of poisonous substances and accordingly abatement of toxic emissions and waste of products, for products; preventing or reducing the adverse effects of a product throughout the life cycle, for services; including environmental anxiety to design and distribution services. In summary, cleaner production; continuous implementation of an environmental protection strategy integrated with processes, products, and services.[4]
Cleaner production applications can be classified into three main categories:
- Reduction of waste and reduction of resource consumption,
- Reuse and/or recycling,
- Product modifications.
Practices for waste reduction
Administrative prevention: It is one of the simplest methods of cleaner production and it is not costly because there is no investment and it can be put into practice immediately after determining the possibilities. Examples are the prevention of water, energy and other source losses such as keeping the water vents closed, optimising chemical dosing, wasting equipment, etc. Moreover, focusing on the management and training of employees can also be done under this heading.
Better process control: Within this heading; temperature, time, pressure, pH, process speed etc. are to be checked to see if they are optimum in terms of welding consumables, production, and waste production, and to make appropriate changes if necessary. This part requires more complex monitoring and management than administrative measures.
Material substitution: This means that the productivity of the production is increased by the use of a higher quality material without compromising quality and cost. In addition, material substitution also means replacing existing materials with some more environmentally friendly materials. For example, replacing a hazardous chemical with an environmentally friendly one means that the purification requirements and costs that would be caused by the hazardous chemical substance are either eliminating or falling down.
Equipment modification: Equipment modification is the development of present equipment to produce fewer waste and to ensure more efficient production processes. Examples include setting engine speeds, optimising tank volumes, isolation of hot pipes, and so on.
New process technology: Because this method involves the use of more modern and efficient technologies, it requires a higher initial investment cost than other methods. However, with the developments of quality and savings the investment can be repaid in a very short-dated and with this application the company can more easily switch to more up-to-date and modern production processes. Such applications also provide improvements in product and production quality.
Reuse/recycling: Reusing rinse water from one process to another cleaning process is an example of on-site recycling or reuse. It involves collecting waste and reusing it in the same or different parts of the production. Non-preventable wastes can be recycled or vend as an offshoot. This includes the creation of by-products, the sale of waste to consumers or other firms after collection of waste. For example; waste yeast, which is released in the brewery, can be reused as animal feed, fish production and food additive substance.
Product modification: One of the basic headings of cleaner production to reduce the pollution caused by products is to change product characteristics. Changing the product requires that the product and its requirements be reviewed again. Reducing the weight and the thickness of the products, designing that allows the product to be more easily recycled, changing the packaging are examples of this approach. The main point of view in the change of packaging is that the protection of the product is guaranteed by the minimum amount of packaging material.
Tools & methods for cleaner production
The choice of which tools are used to determine the use of cleaner production opportunities according to their application areas depends on the problem in operation and the work to be done. Single or multiple tools can be used based on nature of the problem.[5]
Environmental Impact assessment (EIA): This is a procedure, which provides that environmental effects are taken into account before making decisions. EIA includes identification of the positive and negative effects of the planned projects on the environment, determination of the measures to be taken to forestall and decrease these negative effects, and monitoring the implementation of the projects.
Environmental Management system (EMS): It aims at the management of activities that are linked to each other, have an environmental impact or have potency. Phases of this system; environmental policy, planning, implementation and operation, control and correction process, management inspection. It provides a mechanism to firms for thinking about the environment, deciding what to do and planning how to do it, actually applying it, and correcting deviations in the plan.[6]
Lifecycle assessment (LCA): It also named life cycle analysis, life cycle approach, cradle to grave analysis or eco balance, includes an assessment of aspects of a product system that are generally relevant to the environment at entire phases of its life cycle. In other sense, it is the cluster of means and methods that have emerged to aid in environmental management for sustainable development. The LCA can be used to systematically analyse and to prevent/mitigate negative impacts on the environment caused by the goods and services from production to disposal, and to determine resources used throughout their lifecycle and to improve opportunities.[7]
Environmental Technology Evaluation: Environmental impact assessments of various plants and projects involve the discharge of the use of various technologies and the determination of the risks of these technologies on human health and environmental values using qualitative and quantitative methods. In summary, it examines the effects of a specific technology on human health and natural systems and resources.
Chemical evaluation: In this context, the toxic effects and quantities of the chemical substances used in the production phase are analysed to evaluate jeopardy on the health of human and the environment. It also includes methodologies for hazard and exposure assessment.
Waste inspection: Input/output inventories of processes, source, quality and quantity of wastes generated, efficiency and weak points of the current process, waste minimisation targets for cleaner production are determined with waste control. Thus, losses are reduced/prevented to increase process efficiency.
Environmental inspection: It is the most commonly used and most important application tool of cleaner production. Its scopes to specify the quantity and character of the waste from the production process/services and to make decisions about what needs to be done to reduce the pollution. Because it is a very effective tool, there are types developed for different purposes such as waste, energy and risk monitoring.
Eco-label/environmental labeling: An eco-label indicates that a product or service is sensitive to the environment in a particular category. Ecolabelling is implemented worldwide and is a voluntary method for certificating environmental performance.
Industrial symbiosis (IS): The principle behind industrial symbiosis is quite simple; instead of being thrown away or destroyed, surplus resources generated by an industrial process are captured then redirected for use as a new input into another process by one or more other companies, providing a mutual benefit or symbiosis. Working together via industrial symbiosis, companies look for gaining competitive advantage through the barter of energy, materials, water, by-products, waste or common usage of logistics, specialty etc. In this way, they can increase operating efficiencies, save money, reduce their environmental impact, share knowledge, encourage eco-discovery and longtime culture alter.[8]
Water footprint: For a single process or product, it measures the volume of clean water consumed and/or contaminated by humanity. It may also indicate how much water is consumed from a particular river basin or aquifer from globally/country.
Carbon footprint: The carbon footprint that comes to mind with the climate change problem is described as the sum amount of greenhouse gasses which spread by an institution, person, activity or product. The carbon footprint is a measure of the exclusive total amount of carbon dioxide emissions that is directly and indirectly caused by an activity or is accumulated over the life stages of a productâ€. CO2 equivalents or Global Warming Potential (GWP) was described as how many other greenhouse gasses have the same heat holding capacity in the atmosphere compared to the same amount of CO2 for a given period of time. With this unit, the effect of all greenhouse gasses can be collected and expressed in a common unit.[9]
Risk assessment: The risks to be caused by a specific event on sanitary of human and the surrounding and the precautions to be taken about these risks are determined by this method. Policy instruments applied to encourage cleaner production may include legal legislation, voluntary standards, economic instruments (taxes and penalties, state aid, financial mechanisms, etc.), information and technical assistance.
Sustainable strategies for cost effective spinning
Spinning is the vital operation process in textile sector. Usually it requires massive investment. The sector is the primary industry supporting yarn to the export oriented market. The following strategies are to be implemented for cost effective spinning.[10]
Mixing quality and cost: Our spinning Mills are totally depended on natural raw material that has no consistent properties. In order to provide consistent quality with competitive price, efficient purchase of cotton and right formulation of mixing is inevitable for us to meet up the required buyer’s demand. Application of modern technology and machineries for cotton evaluation can ensure the consistent quality of yarn.
Energy cost optimisation: Power or energy is the most critical cost factory in the spinning mills. With recent hikes in gas and power prices, the spinning mills are suffering for productivity shortage. Increasing efficiency and eliminating wastage in spinning mill is the key to remain competitive. In modern spinning mills there is no scope to allow any energy loss. Reduce, reuse and recycle should be the strategy not only in case of materials like cotton and yarn, it should be the approach of gas and power consumption as well.
Almost 99 per cent percent spinning industry is run by captive energy, which uses gas-based generator that produces huge amount of heat and affect the environment drastically when the heat is exhausted with the flue gas. Factories that are enriched in technologies running their chillers using the flue gas of the captive power plants. Reusing the exhaust heat is reducing environmental impact and the chillers on the other hand improving the working conditions of the spinning floors. Right control of the humidity and temperature of the spinning floors increase productivity and quality.
Automation can change the whole scenario of spinning sector in Bangladesh. Automation increases the machine efficiency and productivity. Energy efficient machinery and processes should be selected. Usually Bangladesh spinning mills have state-of-the-art machinery. But still there are some old units having inefficient machinery, running such machinery in modern age means increasing loss. Proper study is needed to replace them or to improve energy efficiency of that machinery.
Product diversification: In spinning industries, not only produce cotton yarn, a lot of diversified yarn such siro, mélange, spandex, core spun, gray melange and inject yarns are being produced. In spite of being less production rate of diversified yarn than cotton yarn, profit margin is drastically high It is time for us to rethink our ability and focus on capacity utilisation and diversified yarn production
Yarn quality improvement: Yarn quality requires improving further to keep pace with time. Buyers are becoming more conscious than before. Therefore, ensuring desired quality with less price is the challenge of spinners. Cotton market is too volatile to get consistent quality cotton with competitive price and so challenges increases in the mills to produce quality yarn using average cotton.[11]
Conclusion
Sustainability is much more than a trending word at a certain time. The three key elements of sustainability are; economic and social development, environmental protection, and each one each one should be considered in relation to the others. Sustainability is very crucial because it maintains people quality of life with protecting diversity and ecosystems in the world with various ways; protecting natural resources, providing energy savings, decreasing waste quantity, investment in the future and economy with recycling/reusing. Namely, it ensures the existence of species.
A contemporary and secure business environment is created by respecting human rights, securing the social justice and protecting the working rights within the scope of sustainability. Cleaner production is not just a buzzword, but also one of the basic approaches to sustainability. It is a systematic approach that involves identifying pollution-causing processes and technologies that lead to the inefficient utilise of energy and raw materials, revealing points that need improvement, and implementing cleaner production opportunities. The lifelong ecological impacts of textile products are affected by the raw materials, their origin and the durability of the product, in addition to the production methods. In this sense, the concept of sustainability has become a matter of concern in the textile spinning Mills.
Acknowledgement
As Author of this paper, would like to thank the management of GRG Institutions for their continuous encouragement and motivation to do this kind of research. The author would express his gratitude to Dr.A.Sankarasubramaniam, Principal, GRG Polytechnic College for his continuous support to do this work.
References
1. Fletcher K. Systems change for sustainability in textiles. Cambridge: Woodhead; 2009.
2. Babu BR, Parande A, Raghu S, et al. Textile Technology An overview of wastes produced during Cotton Textile Processing and Effluent Treat¬ment Methods. The Journal of Cotton Science. 2007;11:141-153.
3. Glavic P, Lukman R. Review of sustainability terms and their defini¬tions. Journal of Cleaner Production. 2007;15:1875-1885.
4. Fresner J. Cleaner production as a means for effective environmental management. Journal of Cleaner Production. 1998;6:171-179.
5. Moore SB, Wentz M. Eco-labeling for textiles and apparel. Woodhead Publishing; 2009.
6. Jaganathan V, Cherurveettil P, Chellasamy A, et al. Environmental pollution risk analysis and management in textile industry: A preventive mechanism. European Scientific Journal. 2014;2:480-486.
7. Chavan RB. Indian textile industry-environmental issues. Indian J Fibre & Textile Research. 2001;26(1-2):11-21.
8. Kumari P, Singh SSJ, Rose NM. Eco-Textiles: For Sustainable De¬velopment. International J Scientific & Engineering Research. 2013;4(4):1379-1390.
9. Sharma S. Energy Management in Textile Industry. International J Power System Operation & Energy Management. 2012;2(1-2):45-49.
10. Muthu SS, Li Y, Hu JY, et al. Carbon footprint reduction in the tex¬tile process chain: recycling of textile materials. Fibers Polym. 2012;13(8):1065-1070.
11. Shaikh MA.Water conservation in textile industry. Pakistan Textile Journal. 2009; 48-51.
Jeyaraman Anandha Kumar is Lecturer with the Department of Textile Processing, G.R.G.Polytechnic College, Kuppepalayam, Sarkar Samakulam, Coimbatore, South India. He can be contacted at: anna_781@rediffmail.com