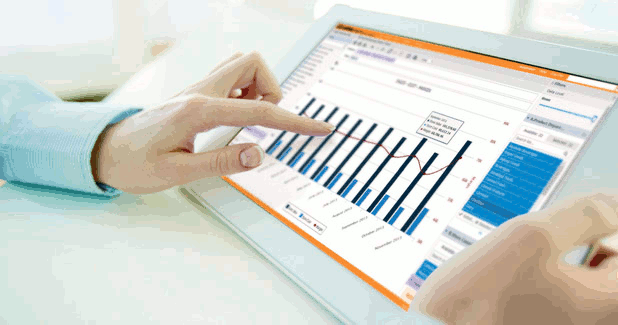
Advanced automation to drive better results
APROL system from B&R satisfies all the requirements of brownfield as well as greenfield sites with flexible and modular solutions without neglecting the high demands on availability and data consistency.
APROL system from B&R satisfies all the requirements of brownfield as well as greenfield sites with flexible and modular solutions without neglecting the high demands on availability and data consistency.
Advanced automation technologies are changing all areas of textile industry right from machine building, supply chain, raw material processing to finished products. Textile industry is looking at automation and digitalisation as an enabler for quality improvement and cost competitiveness. This has prompted the use of connected assets using advanced automation technologies in various areas such as yarn production, fabric production, finishing, production management, inventory management and other areas.
Benefits of advances in technology
Automation has been used in Indian labor-intensive textile Industry for many processes such as cotton picking, ginning, spinning, weaving, processing and even to some extent in garment making. Commonly attributed advantages of automation includes higher productivity, efficiency, better quality, more customised products, improved safety and reduced lead times. Higher degree of automation lowers cost and increases quality offering greater speed and higher throughput. However, human and machine safety, energy savings, less maintenance, self-diagnostics and predictive maintenance to increase machine and plant uptime are some of the challenges textile industry is facing. Cutting-edge automation solutions and technologies help tackle these challenges, achieve excellent performance and stay ahead of competition. New trends are not only reshaping manufacturing processes but also helping plants and factories become smarter, connected and more efficient. Adoption of these developments in textile industry ensures high return on investments and helps Indian machine builders and factories leapfrog global competition.
Machine building made faster
In textile industry where competition is fierce and margins are tight, digitisation helps reduce time, increase efficiency and provide flexibility for both, a textile manufacturer and textile machinery builder. Owing to various benefits, the use of virtualisation is becoming increasingly important in machine building.
Digital Twin provides a complete digital footprint of machines, enabling machine builders to detect physical issues sooner, predict outcomes more accurately, build better machines with superior quality and reduce time-to-market and costs. Virtualisation is very powerful allowing visibility of machine operations as well as large interconnected manufacturing systems. By making virtual representation of product or process, Digital Twin is helping textile machine builders to save cost and time involved in building machines and software development.
Meeting productivity & efficiency benchmarks
Fabric preparation involves a variety of machines. A series of coordinated movements are required between the bale opening, cleaning, mixing, blending and carding machines. To control and manipulate how the fiber is aligned and carded, precision is highly important.
Combing machines and draw frames are used to improve the quality of the sliver from the card, separate the good long fibers from any dirt or undesired particles and regulate card thickness. High drive dynamics and rugged controls are required to achieve optimum results and maximum efficiency. There are many different methods to make yarn from textile fiber depending on the material and the desired output.
A new way of textile inspection
The competitive nature of the textile industry increases pressure on manufacturers to deliver high quality textiles at low costs. Hence, quality control at every stage right from the start of production until the final product packaging is essential to building a successful business. This has put an increased focus on integrating product inspection systems in the machines and the lines. Machine vision allows manufacturers to produce high quality textiles while minimising cost and maximising profits. By detecting defects before final product reach buyers, machine vision enables manufacturers to supply defect free goods, minimise waste, and promote a sustainable environment. With the help of image processing software, machine vision solution provides a feedback to guide production decisions.
Making traditional factories SMART
Many textile mills are still running isolated legacy equipment, thus, not being able to monitor real-time data of energy usage, product quality and productivity. To get more out of such digitally isolated legacy equipment and make manufacturing processes more transparent the solution is to make existing factories flexible and modular. APROL system from B&R satisfies all the requirements of brownfield as well as greenfield sites with flexible and modular solutions without neglecting the high demands on availability and data consistency. APROL enables factories to implement energy monitoring, condition monitoring and process data acquisition in one system. This is a cost effective solution for factories, as they do not need different systems for satisfying different needs. This can make new installation as well as existing installation smart and industrial IoT ready.
In a single, consistently easy-to-use platform, APROL unifies process automation, factory automation and infrastructure automation. The B&R Edge Controller makes it possible to acquire data, evaluate it and then send it to the cloud. It also facilitates gathering data from various controllers on the field and moving it to the MES/ERP systems or the cloud.
Increasing machine up time
The factories are faced with a dilemma of improving product quality, increasing system availability while at the same time cutting back on maintenance costs. Equipment is a major investment for any company and keeping it up and running is critical. Predictive maintenance plays a vital role in monitoring the condition of assets in the factories. Condition monitoring helps to reduce machine downtime and maintenance cost. APROL ConMon solution monitors the health of machinery making it ideal for implementing condition based predictive maintenance.
APROL ConMon makes it possible to acquire process and assess relevant condition parameters and can be set up with minimal efforts. It makes implementation of condition monitoring system and plant asset management solutions considerably easier.
Energy consumption in a textile mill is huge with energy bills soaring making monitoring of energy consumption in factories the need of the hour for reducing operational expenses. APROL EnMon is an energy-monitoring package allowing factories to measure, record and analyse energy consumption. Historical data allows detailed analysis of energy consumption, making it easy to identify cause and effect. By monitoring real time energy utilisation, companies can reduce operating costs and eventually improve their competitiveness in the market.
Smart manufacturing
To remain competitive in era of Industrial IoT, digital transformation is the need of the hour. B&R offers complete hardware and software solutions, comprehensive service and expertise in automation and digitalisation of textile machinery and factories. With next generation technologies and open source communication standards such as OPC UA, POWERLINK and openSAFETY as well as the powerful Automation Studio software development environment, B&R is the right partner for implementing advanced automation solutions in both new and legacy equipment. With solutions for machine to factory automation, B&R serves as a perfect partner to textile industry for sustainability, flexibility, higher productivity and profitability.