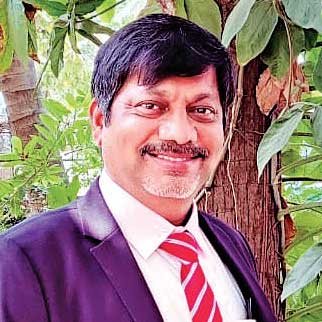
A.T.E. offers the best technology at affordable price
A.T.E. Enterprises, which has a formidable presence in textile engineering, provides cutting edge machinery solutions for every textile process. For spinning mills, A.T.E. offers the latest technology systems for blowrooms, cards, drawframes, combers, twisting machines, humidification systems as well as a range of accessories and spinning machinery components. Heading the company’s spinning division is Kiran Hanchate, VP – Spinning, A.T.E. Enterprises Private Limited, who has been associated with A.T.E. for the last 22 years. In this interview with Rakesh Rao, Kiran Hanchate highlights the trends in the textile manufacturing and the company’s growth plans.
As a solution provider to the textile industry, how is A.T.E. Enterprises helping textile companies to overcome manufacturing challenges?
We have over 80 years’ experience in the textile industry. Our aim is to be a single window solution provider for the industry – in spinning, weaving, processing and also in utilities (like ETP, automation, Industry 4.0 etc.) Our objective is to bring in state-of-the-art technology solutions for problems faced by the industry such as manpower shortage. We have introduced many automated solutions for the textile industry.
The industry is looking at reducing energy consumption. So, we introduced TeraSpin energy-saving spindles that result in energy savings of about 5%-11%. By just changing the old spindles you can save energy in ring frames, which is a major source of energy consumption. Also, the payback period is very short.
In 2020, the textile sector was badly hit due to the COVID 19 pandemic. Are you seeing normalcy returning back in the sector? How is the order flow for A.T.E. at present?
Yes, it is normal. In 2020-21, there was a decrease in textile exports, as both, the supply chain and demand were disrupted due to COVID. In 2021-22, we started seeing signs of recovery both in the economy and in the demand for textiles. For spinning, for certain products we are booked till 2024, while for others we are booked for the next 12-13 months. In short, post COVID, there’s been a solid recovery.
Are you seeing widespread recovery or uptick is restricted to specific segment/s?
The growth has been widespread because lot of buyers are opting for the China Plus One policy and are looking to divert business to India. We are seeing big growth all across – especially in home textiles and technical textiles (like hygiene, medical, and recycled and blended yarns). The Indian textile industry can grow to be the world’s leading textile supplier.
You have been a solution provider to the textile industry. What do you bring to the table for customers? How is A.T.E. helping them to modernise?
A.T.E. always strives to bring in state-of-the-art technology to the industry. During COVID times, after discussing internally and with customers, we realised the biggest pain point for the industry is manpower. For example, in blowrooms (where you need manpower for bringing in bales, opening the bales and manual feeding), we have the right solutions from Trützschler for automatic bale opening. There has been a demand for blended yarns and we have seen a surge in requirements for tuft blending, for which Trützschler has a fully automatic process. Automation of this process has really brought down the manpower requirement and also increased quality and production.
Similarly, old cards which were running at low speeds have been replaced by modern cards. When a customer replaces a third or fourth generation card with Trützschler’s TC 15, the productivity goes up by 80%. We also have cone-to-container (C2C) solution from SIEGER which is an automated transportation solution that enhances efficiency and saves manpower, space and time. With C2C, the cone can be transported to the container automatically from the winding machine to container. We are seeing lot of interest and demand for C2C systems.
The government has announced a number of schemes/initiatives for textiles (including PLI schemes, MITRA parks, etc). How will the textile industry and the suppliers to this industry benefit from these measures?
Growth projected for the Indian textile industry, by various market research reports, is at 11% CAGR. By 2028, it is expected that the industry will touch $ 225 billion. It’s a massive growth and there is a huge demand from the world because of China Plus One policy and the ban on Xinjiang cotton. This has increased the demand from India. The new policies of the Indian government will help the industry to increase production, develop new products and cater to the global demand.
In the recent months, many textile companies have announced investments for capacity expansion. Will this factor lead to more demand for A.T.E. products?
Capacity expansion activity peaked in 2011. After 2011, for the last 9 to 10 years, there has been a minimal addition of spindle capacity. Now there is a big upswing in demand for all types of textile yarn, such as blends, Vortex yarn, recycling. etc. After COVID, labour is an area of concern for many mills. With modernisation, mills can achieve their targets with minimum labour. Increased yarn demand and focussed reduction in yarn manufacturing costs are the factors leading to increased demand for textile machinery.
One of the factors affecting the industry at present is the raw materials, especially cotton prices. Against this background, could you throw some light on how modern mills or machines can help spinning mills to improve their productivity?
When the markets opened up after the first wave,the textile industry saw a big surge in the market with consumption growing very rapidly. This created a huge demand for Indian cotton leading to the rise in cotton prices.
A.T.E. has a very good solution which helps reduce waste in blow rooms and cards. We offer Trützschler’s Universal Cleaner CL-U (which comes with WASTECONTROL) and waste controller in carding machines. We have seen that customers are enjoying up to 1% saving in fibre which is a considerable saving considering the current cotton prices. Truetzschler’s Waste Cleaner CL-R is another useful product in this
area that, depending on the type of waste, can enable recovery of around 50-60% fibres from the waste. This is how A.T.E. helps its customers to reduce their waste and increase profitability.
While India has a sizable share in the cotton-based textile products global, its share in the MMF, tech textile and, even garmenting, is miniscule. What are the reasons for it? What are probable solutions?
In cotton, we have approximately 10% cost advantage compared to the global prices. We don’t have the same kind of benefit in man-made fibres. The solution is we need to have a lower cost of raw material to be competitive in the market. New incentives like PLI schemes, which have been announced by the government, may help in reducing our raw material costs in man-made fibre and make Indian spinning mills competitive. India has state-of-the-art technologies in mills that use synthetic raw materials. What it needs is access to competitively priced cost raw materials to make it globally cost competitive.
The market for synthetics is on the rise due to increased applications in sportswear, active wear, technical textiles, medical textiles, etc. The demand for MMF is growing faster than cotton. In India, the garment sector is considered to be a sunset industry, with no large investments taking place in the sector. We will have to develop large capacities to increase our cost competitiveness (while maintaining quality and timely delivery) to become globally competitive in garments.
Against the background of COVID 19 pandemic, what are the new challenges and opportunities before the Indian textile industry?
The China Plus One policy has really opened up the doors to new markets for Indian textile industry. Apart from this, we also see that the US ban on Xinjiang cotton has created another opportunity. There is a huge inflow of orders. The major challenge for the industry is managing supply chain, which was severely disrupted due to COVID pandemic. Another hurdle is the increased raw material price which is pushing India’s yarn prices up and increasing upstream prices. This may make us uncompetitive in the global market. Hence, there is a need to take steps to reduce our raw material costs, increase our productivity and quality which will help us be competitive in the global market.
Has there been any change in the demand pattern in the post-COVID era compared to pre-COVID period?
Post COVID, we are seeing a big upswing in the man-made fibres market. There has been a good demand for hosiery yarns because of work-at-home culture. As the hosiery products are seeing an uptick, the demand for viscose-related products has also witnessed a jump. At the same time, we have seen the flow of machinery more towards man-made fibres.
What are the emerging trends in textile manufacturing?
In textile manufacturing, more and more hygiene products are emerging because of the pandemic and increasing awareness about health & hygiene. Also, the demand for non-wovens and home textiles is increasing; thus, propelling the requirements of textile machinery.
What are your growth plans for your division?
We will focus on bringing solutions to customers with very affordable technology and state-of-art machinery. Additionally, we also will focus on automation which is the need of the hour. Our aim is to always bring in the best technology that will increase the productivity of the customer while at the same time reducing maintenance.
Kiran Hanchate, VP – Spinning, A.T.E. Enterprises Private Limited