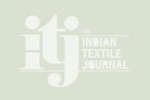
A study on lubrication practices in ring frames
The quality of grease, represented by its unit cost, plays a significant role in deciding the frequency of application, affirm D Shanmuganandam, J Sreenivasan and N Parthasarathy. As we are aware, wrong selection and inadequate quantity of lubricants and inappropriate frequency of application not only affect the working performance of machines.
The quality of grease, represented by its unit cost, plays a significant role in deciding the frequency of application, affirm D Shanmuganandam, J Sreenivasan and N Parthasarathy.
As we are aware, wrong selection and inadequate quantity of lubricants and inappropriate frequency of application not only affect the working performance of machines but also increase the requirement of spare parts, manpower and electric power. On the other hand, higher consumption of lubricants will increase the cost of maintenance.
Recently, SITRA had conducted an inter-mill study on the practices being followed by the mills in the lubrication of ring frames. Lubrication of a ring frame involves greasing and oiling, of which oiling is further divided into two categories: spindle oil application and other oil application. The study had been confined to long length ring frames from two popular makes, comprising four models.
Lubrication practices such as schedules and frequencies, quantity of application and type of lubricants and their unit cost, followed by the mills in the four models were collected through a questionnaire. The salient findings of the study are covered in this paper.
Participation of mills
As many as 87 mills from different parts of the country, most of them hi-tech, had participated in the study by sending the filled-in questionnaire to SITRA. The profile of participation shows that about 70 per cent of the mills were from the four southern states and the remaining were from nine different states and union territories.
Expected consumption of lubricants
Based on the information furnished by the mills in the questionnaire, the expected consumption of grease, spindle oil and other oils per spindle per year (in terms of quantity as well as cost) was estimated for all the four models of ring frames which are represented as A, B, C and D (Table 1). Average consumption of grease in the four models ranged from 10.4 g to 12.4 g per spindle per year. The expected consumption of spindle oil averaged at 8.7 ml per spindle per year whereas that of other oils averaged at 18.7 ml per spindle per year. This would mean that a 1,200 spindle ring frame would consume, on the average, about 14 kg of grease, 10 litres of spindle oil and 22 litres of other oils per year. In a 30,000 spindle mill, the total consumption of lubricants per year in the ring frame shed, on the average, would be 340 kg of grease, 260 litres of spindle oil and 560 litres of other oils. A further analysis of the data given in the above table reveals that the inter-mill differences in the expected consumption of grease ranged from 4-8 times in the four models. In the case of consumption of spindle oil and other oils, the inter-mill differences ranged respectively from 3-8 times and 5-16 times in the different models.
Cost of lubricants per spindle per year
Total expected cost of lubricants per spindle per year amounted to about Rs 9, ranging from Rs 8.3 to Rs 9.3 between models (Table 2). Of the total cost, grease accounted for about 50 per cent followed by other oils (34 per cent) and spindle oil (17 per cent) (Figure1).
In terms of per frame (1,200 spindles) per year, the average cost of lubricants worked out to around Rs 11,000, which means that a 30,000 spindle mill would spend, on the average, about Rs 2.6 lakh per year for lubricating the ring frames. Inter-mill differences in the cost of individual lubricants per spindle per year were also very high in all the four models; 5-17 times in grease, 3-6 times in spindle oil and 7-28 times in other oils.
Reasons for the high inter-mill differences
Though some differences in the consumption o