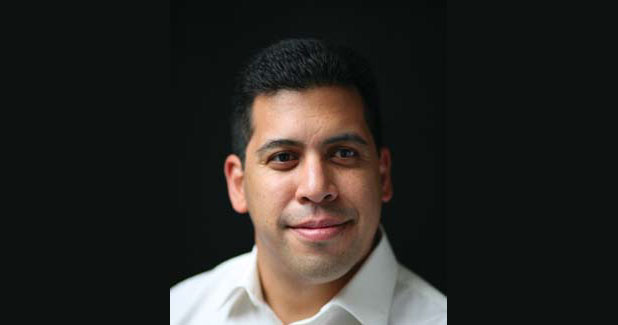
A perPETual devotion to converting PET bottles to filament yarn
Incorporated in 2007, perPETual has developed, and patented a breakthrough proprietary recycling process which transforms post-consumer polyester plastic bottles back into high quality environmentally sustainable esters.
Incorporated in 2007, perPETual has developed, and patented a breakthrough proprietary recycling process which transforms post-consumer polyester plastic bottles back into high quality environmentally sustainable esters. The company has transformed over 1.5 billion used PET bottles into about 45 million sqm of high-quality sustainable polyester fabric. perPETual partnered with brands such as Decathlon, Adidas, Puma, H&M, etc. who have used perpetual yarn’s fabric to make approximately 44 million t-shirts, 12 million garments and four million bags and accessories. Many fashion and sports brands are moving to recycled polyester so they can be more environmentally friendly in product lines.
Ventureast invested in Polygenta Technologies (a subsidiary of perPETual Global) in 2013 through its Ventureast Life Fund III. Today, Polygenta converts over a million waste PET bottles per day into 100 per cent recycle content, premium quality polyester yarns, and exports worldwide.In an interview with the ITJ, the company’s Founder, Dr Vivek Tandon, speaks on the latest trend of converting PET bottles into polyester yarn, and its latest machinery.
At a time, when this concept of converting PET bottles into polyester happening widely abroad, how did this idea strike your company? How was the beginning and progress?
PET bottles have been recycled into lower value staple filament yarns for many years. Companies such as Indorama and Reliance were some of the first to do so. The problems with making staple fibre however, are that it is a mechanical process, utilising a low level of technology and is ultimately seen as a dirtier process. This is because only the outside surface of the plastic is cleaned during the cleaning process, and these mechanical recyclers are not able to remove the contaminants that are absorbed inside the plastic. Another issue is that mechanical recycling is batch-based, meaning that end product quality is inconsistent, and the quality of the product is batch dependent. perPETual’s breakthrough technology and patented process allows for plastic bottles to be transformed back into an ester on a continuous basis with the removal of all contamination both on the surface of the plastic bottles and within the plastic, resulting in product whose quality is consistently at a high-level.
perPETual was incorporated in 2007 when our (now patented) breakthrough proprietary recycling process for transforming used PET plastic bottles back into high-quality environmentally sustainable esters was conceptualised. This, alongside the company ethos of seeing plastic not only as waste, but as a valuable resource to be used repeatedly helped make perPETual the company that it is today. We want to continue to make a material difference to the world and encourage each and every person to do the same.
perPETual acquired and developed our first full-scale plant based in Nashik, India and operated by our manufacturing partner Polygenta. All of the high-quality filament yarn produced at the Nashik plant are made from 100 per cent used plastic bottles.
What is the total capacity and how was this achieved over the years? Give us a glimpse of the facilities & the set-up?
perPETual’s currently convert over 2 million clear PET plastic bottles into 8,000 tonnes of perPETual filament yarns. We are currently fundraising to expand the current plant capacity to 30,000 tonnes per year and we are working with partners to build new perPETual recycling facilities in other locations across the globe. We have a goal of converting 50 million bottles a day into high-quality sustainable ester 2022.
The Nashik plant operated by our manufacturing partner Polygenta takes in 2 million plastic bottles a day which are reverse engineered into high quality sustainable ester before being converted into POY (Partially Orientated Yarn), DTY (Drawn Textured Yarns) and FDY (Fully Drawn Yarns)
What are the technologies used, and what is the import content and indigenous content in the machinery?
perPETual has globally patented out unique technology and process. We use a combination of our own equipment and machinery for assembling our process; and we use locally sourced equipment for the general areas of the plant such as generators and water utility treatment facilities.
How many brand partners are there and what are the achievements in this line by your company?
perPETual currently has over 40 customers/brands on a repeat basis and has entered into successful partnerships with various brands and textile mills globally to help with this supply. Some of the brands we supply to include Adidas, Decathlon, H&M, Zara, Puma and C&A, some of which have recently announced their intent to switch to an increased level of sustainable polyester used throughout their products. Decathlon being one such brand that recently announced its desire to increase the amount of sustainable recycled polyester used in its products sold in France by 100 per cent. Another is Adidas which has similarly announced its pledge to switch all polyester used in its products to sustainable recycled polyester by 2024.
Throughout the years we have had many achievements as a company, some notable inclusions being in 2012 when we were announced as the IFC Sustainable Investment of The Year and our recent recognition at Davos as being a global leader in the circular economies SME category. Also, as of December 2017 perPETual hit the milestone of having recycled over 1.5 billion used plastic bottles into approximately 15,000 tonnes of high-grade sustainable perPETual filament yarn.
PET bottles are slowly being phased out, and what will be the future in case you run short of raw material?
Although the various world governments have made pledges to combat the growing plastic pollution problem that we face (driven in party by programme such as that by Sir David Attenborough’s in Blue Planet II) there is still an abundance of plastic bottles on the market totalling over 660 billion per year. Many nations, for example Haiti, rely predominantly on bottled water as they do not have the systems to supply their population with clean drinking water. Indeed, this is true of most of the high growth countries in the world including India
In fact, PET plastic is not a problem when it is viewed as a feedstock rather than a waste product. perPETual can convert plastic bottles back into ester and back into plastic bottles or polyester textiles. We have the technology to allow used plastic bottles to be recycled again and again and again.
We have also successfully trialled T2T (Textile-to-Textile) recycling in small batch quantities. Thus, allowing us to transform unwanted polyester-based textile garments back into sustainable ester using our process. This ester can then be used to create new PET-based products. Products made from our ester can be put back through our process repeatedly (depicted in the diagram below), thus contributing to the circular economies and giving us scope at a large enough scale to ‘fuel ourselves’ in the future.
What do you think is the future of PET conversion, and what are your company’s plans for the future in this area?
In the 1960s, aluminum cans could be seen polluting the beaches and the land. Companies claimed they could recycle the used cans but in reality, most companies only downcycled them or required heavy subsidies to be profitable. Finally, Alcan developed a technology which was able to profitably recycle aluminum cans and, today, more than 75 per cent of the world’s aluminum comes from recycled aluminum. perPETual is the Alcan of the PET plastic industry. We have developed a technology which can be profitable, and can environmentally and efficiently recycle used PET plastic bottles. We hope that over the next 15 to 20 years, the perPETual technology can ensure that most PET based products are made from recycled, used plastic rather than from oil-based chemicals.
For further information refer to www.perpetual-global.com or email: vtandon@perpetual-global.com
– SAMUEL JOSEPH