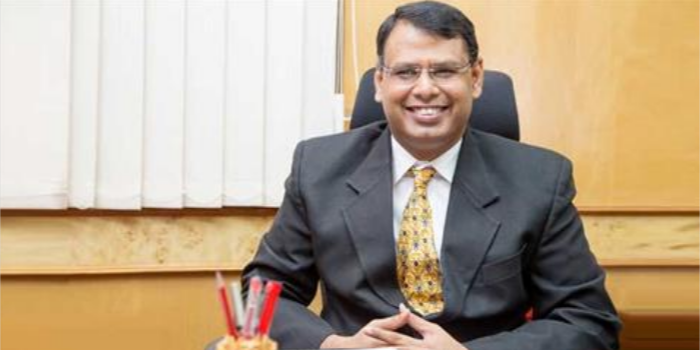
A Ilavarasu: SAA aims to set up wet spinning technology
In this interview, Anandan Ilavarasu, CMD, S A Aanandan Spinning Mills Pvt Ltd (SAA India), talks about policy anomalies and suggests some solutions to give a boost to spinning industry.
Heavy reliance on cotton, unavailability of
low-cost manmade fibre and lack of modernisation are hindering the growth of
Indian spinning industry. In this interview, Anandan Ilavarasu, CMD, S A Aanandan Spinning Mills Pvt
Ltd (SAA India), talks about policy anomalies and suggests some probable
solutions for giving a boost to Indian spinning industry.
What are your thoughts on rising yarn prices?
The increase in yarn price is very much
required to save the ailing spinning mills. Most of them have borne the brunt
in the past years. This Bull Run will help the spinners to recoup the losses in
part and plan for much needed modernisation and automation.
What are the challenges that this industry
encounters? What would be your suggestions to overcome them?
The biggest challenge for the cotton spinning
industry is availability of quality cotton at stable prices throughout the
year. Cotton being a seasonable commodity is largely held by traders both Indian
and MNC. However, the MNC traders have access to finance at international
rates, so they buy cheaply in season and sell dear during the off season.
Unfortunately, the bankers are unable to provide industry specific support for
stocking cotton at peak season. Secondly, this year’s budget levied 12% duty on
imports of cotton despite the fact that we are dependent overseas for ELS,
contamination free and branded cotton like Cotton
made in Africa (CmiA). We have represented through our apex associations
to the textile ministry to correct this anomaly.
Thirdly, the world is moving towards
increased consumption of manmade fibres (about 70%) and balance is natural
fibres (about 30%). However, Indian textiles are still cotton focussed and thereby
playing in a small ground and losing the desired market share. The reason for
this global apposite is mainly due to monopoly production of polyester, viscose,
acrylic fibres and levying unnecessary anti-dumping duties to protect few
industrial giants. Therefore, Indian mills have to buy manmade fibre at an
inflated price vis-Ã -vis neighbouring Asian spinners, thereby making Indian manmade
garments uncompetitive. Unless this most important anomaly is corrected, Indian
textile sector growth trajectory can only be flat.
When it comes to automation and digitisation
in the spinning industry, very few manufacturers have made the leap and
invested in technologies. Why is that?
The spinning industry is highly capital
intensive and needs large capital at low coupon rates to service the debts. But
bankers follow the same yardstick for all industries and thereby many who have
used debt finance to modernise and automate had to face the heat during recession.
Ideally, the industry now needs to tap the capital market and take a hard look
at alternative finance options.
What steps have been taken at your
organisation to progress towards automation?
We have invested heavily in modernisation of
the plant and machinery. But limited access to capital is the hindrance for us
to move towards complete automation.
What innovations or technologies have you
invested in or plan to do so in the future?
Hygro spinning, auto piecing, spindle
monitoring and link winding are the technologies we plan to invest in the future.
Which are your major markets in India and
abroad?
In India, it is Tiruppur, Erode, Salem and
Kolkata. Internationally, it is Turkey, Germany, Japan, Bangladesh, China, Myanmar
and Sri Lanka.
What are the long- and short-term goals set
by your company?
Our short-term goals are to focus on
sustainable- and social-complaint products like organic, fair trade, recycled,
Better Cotton Initiative (BCI), and CmiA yarns and, thereby, reducing the
carbon footprints. Our long-term goals are to set up wet spinning technology
for spinning bast fibre like flax, ramie, hemp and worsted spinning for wool.