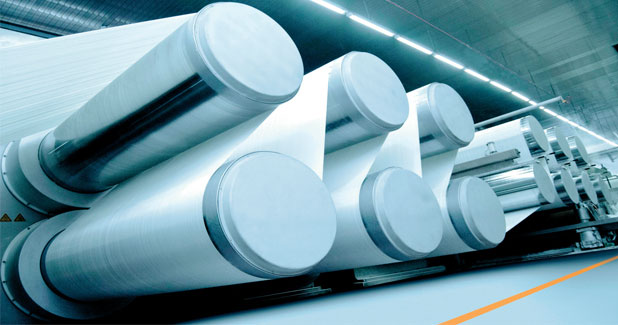
A greener environment due to PLA staple fibre yarns
PLA staple fibres are a possible alternative as a substitution of existing synthetic fibre products. The replacement of oil-based polymers by bio-based alternatives is a topic that is regarded with high priority in textile innovation programmes, aver Vadim Tenner, Marie-Isabel Popzyk, Yves-Simon Gloy, Raf Van Olmen and Thomas Gries.
PLA staple fibres are a possible alternative as a substitution of existing synthetic fibre products. The replacement of oil-based polymers by bio-based alternatives is a topic that is regarded with high priority in textile innovation programmes, aver Vadim Tenner, Marie-Isabel Popzyk, Yves-Simon Gloy, Raf Van Olmen and Thomas Gries.
Currently, Europe consumes more than 6 million tonnes of textile fibres: About 34 per cent for clothing, 27 per cent for housing and carpeting, 38 per cent for other industrial technical usages. The European textile and clothing industry has a longstanding tradition of leadership in terms of innovation, fashion and creativity, and even thought it increasingly encounters fierce global competition and significant relocation of manufacturing to low-wage countries ? with ?165 billion turnover ? it continues to represent one of Europe?s major industrial sectors.
Today, the textile industry is challenged to make a radical shift towards innovative and high value-added products to counter the competition with low-wage countries. At the same time, European industry is looking to find links to the environment-concerned customers via the increased use of renewable and recyclable/recycled materials.
Poly lactic acid (PLA) is at the moment produced from starch (corn) or from sugar (sugarbeet). The fibre products are highly smooth and completely non-irritating to the skin, while being 100 per cent biodegradable and compostable. PLA staple fibres are a possible alternative as a substitution of existing synthetic fibre products. The replacement of oil-based polymers by bio-based alternatives is a topic that is regarded with high priority in textile innovation programmes.
SPEY targets textile application, in specific: bed linen. This product is less vulnerable for degradation compared to applications like a T-shirt that needs to be washed after each use. Former projects for textile application like Biotext had a low economic feasibility due to low spinning speeds. SPEY provides higher spinning speeds and less degradation for PLA suited applications. The general innovation target of SPEY is the exploitation of the market potential of biopolymer based textile products by the development of PLA staple fibre spun yarns, and to increase the quality of these yarns.
At medium term, the market potential is estimated to the production of 40.000 t/a for PLA and PLA blended yarns with a volume of approximately 140 million ?/a all over Europe when comparable properties of existing yarns are reached. The yarns containing PLA staple fibres can be implemented in a variety of textile segments: apparel, upholstery, technical textiles (work wear), medical applications (gauze bandages) or home textiles and will be able to compete with standard cotton/PES staple fibre yarns. The aim of this project is to develop the technology and expertise to economically produce PLA-based spun yarns and blended spun yarns (PLA in combination with viscose or cotton) with properties comparable to existing PES alternatives. It is targeted to develop in commercially available conditions, high quality bio-based spun yarns with a high durability (long life time). This goal can only be achieved when all parameters relevant for production of high quality PLA spun yarns are defined, both in the extrusion process and the yarn spinning process.
PLA offers additional end-of-life possibilities. It is known and demonstrated that PLA can be recycled via melt processing and due to the low melting temperature and the limited water-uptake the process has a low cost and offers good qualitative products. Also hydrolysis to feedstock (monomers) is possible. In contrast with most oil based polymers, PLA can be composted or used in biogas installations. This is important in applications such as blend spinning since it is known that for blends such as PES/cotton yarns (a big-volume product in staple fibre yarns) there are at the moment no good end-of-life revalorisation possibilities.
The SPEY project contributes to a greener environment. Depending on the crop used 3.3 up to 6 tonnes of PLA can be produced per hectare crop yield. This is very efficient compared to the production of about one tonne of cotton per hectare. During 2012, 190 ktons of PES fibres were produced just in Germany. The total energy consumption to produce PLA is about 50 per cent lower than for PES (Fig. 1) and as a consequence also the total emission of greenhouse gases is about 60 per cent lower for PLA than for PES (Fig. 1).
Moreover, there?s not much oil occurrence in Europe but enough area for cultivable land for food and crop for technical use. The industry of agriculture and forestry are offered alternative production and income possibilities.
Implementation
Aim of the current work package within the SPEY project is the production of staple fibre yarns of commercially available PLA and of experimental PLA by Centexbel. Also, spinning methods for processing PLA are optimised and PLA staple fibre yarns with improved properties are developed. Cotton and PES (Table 1) based yarns will be the benchmark for the development of the PLA staple fibre yarns. The main target is to reach a breaking tenacity in the range of 16-30 cN/tex.
Commercially available PLA staple fibres by De Saedeleir (DS) Textile Platform N.V., Dendermonde, Belgium, are the project bench mark for commercially available staple fibres. The fibres are carded and further processed into a sliver. The sliver is spun into a yarn using the ring spinning technology.
The experimental PLA filaments are cut and texturated at the UCM of the company Barnet Europe GmbH & Co. KG. Spin finish application is performed by the UCM Bozzetto GmbH. At ITA the fibres are processed into a sliver and send to the UCM member Schlafhorst for rotor and ring spinning. An overview of the work packages is provided in Fig. 2:
Results
The mechanical and thermal boundary conditions for staple fibres are evaluated during the ring spinning process. Due to the high amount of needed material and since the production volume of experimental PLA by Centexbel is limited, this work package is carried out with PET and not PLA.
Within the next step, staple fibre yarns of commercially available PLA and of experimental PLA by Centexbel are produced. Spinning methods for processing PLA are optimised and PLA staple fibre yarns with improved properties are developed. The process parameters from the PET-yarn production serve as a bench mark for the further ring spinning. PLA staple fibres by De Saedeleir (DS) Textile Platform N.V., Dendermonde, Belgium, are the project bench mark for commercially available staple fibres and properties are shown in Table 3. It is evident, that the staple fibres by DS are twice as long as the PET staple fibres, while having only 20 per cent of the tenacity. Also, the yarn count of PLA by DS is about five-times as high as for commercial PET. The ring spinning process was mainly stable; only limited yarn breaks occurred.
Table 4 shows the fibre properties of the DS PLA fibres after different processing steps. Staple fibre length is reduced during carding. Also, some degradation occurs showing in the limited tenacity and elongation at break. The laboratory results of DS PLA ring yarn (Table 5) are the benchmark for the following experimental PLA ring yarns. The fibres from DS are suitable for ring spinning with long staple drawing system, due to their staple fiber length of 76 mm. The result is a yarn strength of 8.2 cN/tex (Table 5).
The goal behind the development of different experimental PLA multifilaments by Centexbel is to achieve physiological properties, similar to cotton, for PLA yarn. The following experimental multifilaments (Table 6) are developed till now and sent to ITA for the development of textile structures. Further batches will be produced till the end of 2017.
The spin finish Monopol MW 5866 is by Bozzetto GmbH, Krefeld, Germany and Avi Fil PP 743B is by Vertexco, Menen, Belgium. The experimental PLA filaments from Centexbel were cut and curled by Fa. Barnet Europe GmbH & Co. KG. The fibre length lies within 40 and 45 mm, which is sufficient for further processing. Further polymer batches will be optimised for an accurate fibre length of 38 mm.
Batch 01 was not processible into yarn, due to its high Titer of 10.97 dtex. Trials with Batch 02 show, that the fibre properties decrease rapidly after cutting and crimping. Strangely the properties increase after the following processing steps of spin finish application and carding. The laboratory tests were repeated and the results were confirmed. The fibre count was also tested showing a finer fibre of 3.58 dtex after the cutting and crimping process (before 4.05 dtex). The fibre count was taken into account for the laboratory tests. The strength of the ring yarn of 8.3 cN/tex (Table 8) suggests the assumption that the fibre tenacity must still be around 13.55 cN/tex (Table 7). Also, all machine parameters for testing of the fibres were the same.
The ring yarn of batch 02 was processed on a ring spinning machine at ITA. A stable process was not reached, many yarn breaks occurred. The high number of yarn breaks can be owned to the limited tenacity. Also, each yarn break causes an irregularity in the yarn when threads are joined again. Table 8 shows the laboratory results of batch 02 ring yarn.
Batch 03 was not applied with an additional spin finish for rotor spinning since spinning trials showed no necessity for a second spin finish. Its properties after different processing steps are shown in Table 9.
A pre-trial was carried out first using a fibre blend of 50/50 PLA/cotton and a MDTA 3 for sliver production. The opening roll shortened the staple fibres from 32.14 ± 2.95 mm to 24.05 ± 8.09 mm. Due to the very short staple fibre length and an irregular staple fibre length distribution, ring spinning trials were not successful. The fibre shortening can be attributed to the low fibre tenacity. With the rotor spinning technology it was possible to process a yarn but with only a limited yarn strength. Machine parameters were set according to Table 10.
At the glass transition temperature (TG) lactic acid is released and degradation phenomena occur. For the crimping process, the fibers must be heated to TG. At present, this process step shows the highest mechanical stress on the material, as a result of which the fibre strength continuously decreases owned to degradation processes.
Since the texturation process that was used for the prior batches causes a degradation of the PLA, for batch 04 trials with the air-jet texturation process were carried out. The temperature was set lower than the glass transition temperature in order to avoid degradation phenomena. It has been tried to texturate the filaments by mechanical stress. Very low crimping occurred; the filaments in the multifilament were mainly separated from each other. Also, the multifilament showed many knots after passing the air-jet nozzle. Batch 04 was also not equipped with a second spin finish. The fibre properties of Batch 04 after different processing steps are listed in Table 11.
Conclusion
The scientific findings from the performed experiments show, that the production speeds of 150 ? 250 m/min targeted in the proposal cannot be obtained. Rotor revolutions needed for these production speeds cause high fibre abrasion that leeds to low mechanical properties of the yarn and these fibre rubbles hinder further processing steps, e.g. weaving.
The trials with batch 01 were cancelled, due to an unstable spinning process. Batch 02 was prepared with the same processing steps. The start spinning of the material was not possible. A yarn could still be produced by Fa. Schlafhorst, branch office of the Saurer Germany GmbH & Co. KG, Übach-Palenberg, on the Autocoro 9 while feeding the material into the running process. After the yarn break, attempts for automated spinning start on this machine were not successful. A successful spinning process and a followed circular knitting was possible with batch 03 (Fig. 3), due to the spin finish Monopol MW 5866 and a significantly finer yarn with 3.34 dtex. Further experiments with batches 03 and 04 on ring and rotor spinning machines will be performed in 05/2017.
Authors?Vadim Tenner, Marie-Isabel Popzyk, Yves-Simon Gloy and Thomas Gries?are from Institut für Textiltechnik der RWTH Aachen University, Aachen, Germany.Raf Van Olmen is from Centexbel, Gent, Belgium.