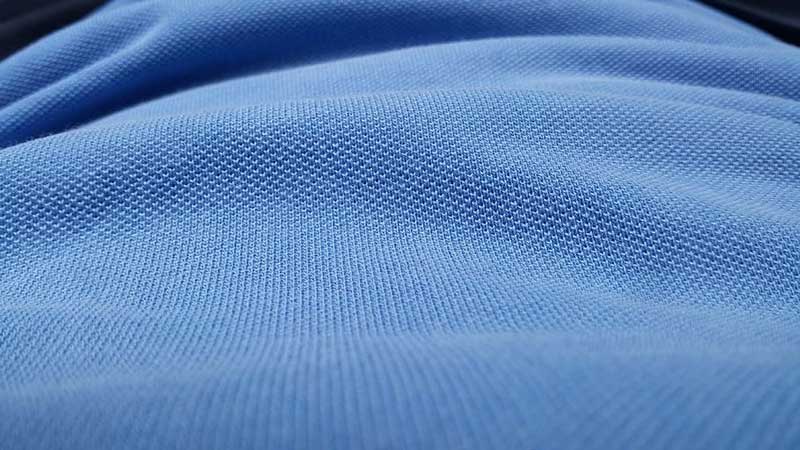
Fashion, why not polyester?
Fashion trends of the future will be more about the environmental impact than the bright and beautiful colours, asserts Kamal Kulshreshtha.
Awareness has increased manifold about sustainability and how we need to make conscious efforts to lessen the burden on environment in all walks of life. The textile and apparel industry, like any other manufacturing activity also consumes energy and pollutes. Hence the talk about sustainable fashion.
Lets first understand the difference between fashion and clothes. Fashion begins where clothes end. Clothes are fashionable but fashion might not always be clothes. So a garment made of fibre in its natural hue is just that – a garment and not fashion. The moment you add colour to fabric, it is fashion. Fashion is all about making a statement. A garment made of natural material like Kevlar, cotton, furs, skins, wool etc. are for protection and comfort rather than fashion. So fashion started centuries ago when fabric was not just draped but cut and stitched and later dyed and painted on to make the consumer stand out. It is still the same – fashion is a way of expressing individuality. Fashion is here to stay.
The aesthetic appeal of clothes lies in their colour, construction and styling. While construction and styling are not polluting unless we start nit-picking, in which case every human activity would be polluting, adding colour to clothes can be polluting. Colour to clothes may be added in a number of ways:
- Dyeing the fibre – before or after it is fibre formation
- Dyeing the yarn – after yarn formation
- Dyeing the fabric – including washing denim to impart special effects
- Printing the fabric
- Printing the finished garment
Now that we have set the perspective, let us look at the different raw materials we use in textile application that is the fibre type in creating fashion.
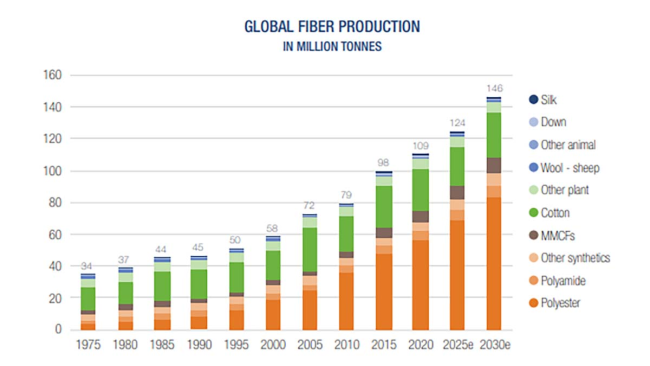
The use of polyester is growing and the share of cotton is shrinking. According to the Common Objective report, 52 per cent of all fibres is polyester with cotton occupying a paltry 23 per cent share. This is often lamented by fashion watchers. Environmentalists decry ill effects of microplastics that harm the balance of nature. Textile and Apparel industry is particularly in the cross hairs because it responsible for close to 20 per cent of all water pollution and releases tons of GHG (greenhouse gases). Polyester is inexpensive but it is despised on social media and otherwise. Polyester is plentiful and man-made but cotton enjoys worldwide support as it is farmed.
No doubt cotton plantations help reduce the carbon dioxide in atmosphere. It helps fight climate change. The more cotton we use, the less microplastics in our oceans and in the mountains. Cotton also helps alleviate poverty as it is a cash crop. It enables the use of other vegetable fibres like Jute to make blends that are more suitable on tactile aspects, so important in fashion. It has several merits over polyester but does that make polyester a devil to be condemned?
For all the maligning that polyester in textile usage suffers, is it really as a big a villain as it is made out to be? That is the point to ponder. So let us look at how polyester is made.
As plastic goes, we produce 450 tons of plastic every year. Till date we have produced more than 9 billion tonne of plastic. Some of these plastic polymers will take hundreds of years to break down into tinier molecules. PET the raw material for polyester is also plastic and is derived from petroleum in the process of factional distillation where the process is such that 0.9 kg of petroleum yields 0.76 kg of petrol the remaining mass has to be either burned out or vapourised and captured. 159 litres of crude oil results in 170 litres of refined petroleum products. Out of this 170 litres, PET constitutes just 4.2 litres or given its density of 1.35 kg/m3, weigh 5.67 kg. Rest of the 165 litres odd distilled out of crude oil or 97 per cent roughly is converted into other plastic forms that are used, resued and disposed off by the world. Some of this plastic, mind you, goes into lifesaving items like tubes for intravenous fluid transfer. Some of it is burnt to power servers that IT industry uses that make it possible for us to be critical about petrochemicals on social media or elsewhere. Like it or not, petrochemicals like fashion are not going away anytime soon. Perhaps it is worth noting that though rapid strides have been made in renewal and non-conventional energy sources, the mining and consuming of crude oil has not gone down.
Less than 1 per cent of the total crude oil processed is converted into PET. Most of the PET is used for making polyester fibre but PET also has alternative uses like being moulded into containers or bottles. Fashion industry is blamed for the portion that gets converted into fibres – some 55 million tons of it, ie. more than 50 per cent of the total fibre consumed in T&A industry. Therefore no matter how big the grey water footprint of polyester fibre might be and no matter how much it costs us in GHG emissions, textiles is responsible only for a tiny fraction of the polluting effects from this manmade fibre.
Carbon footprint is about the effect of greenhouse gases that get released in a particular activity in terms of weight of carbon dioxide which would have equivalent effect on Earth. For polyester this is 6.4 CO2 e, ie. GHG equivlanet of 6.4 kg of carbon dioxide is released into the atmosphere to get 2 sqm of polyester fabric. Why 2 sqm of fabric? because that is pretty much what you need to make a shirt. The Hemp Foundation compares carbon footprint of various material as below:

While the table above might come as bit of a surprise, especially since we consider polyester to be the devil but there are other experts who says the carbon footprint of polyester is double that of cotton. So a lot depends on the manufacturing method, process and technique and perhaps the environment itself. Let us look at some of the fibre to fabric production stages:
Energy consumed in the making of textiles
- Transport of fibre: This could be very different depending upon the geographical location of the yarn spinning mill.
- Climatic conditions: A cotton textile producing mill might have to spend tremendous amount of energy to maintain ambient temperature and humidity on the shopfloor conducive to high speed production.
- Cotton requires a more intense opening and cleaning than polyester since the latter is relatively free of contaminants and undesirable matter.
- For combed counts, 15 to 18 per cent fibres are removed. Hence a 40s combed cotton yarn would require not only more machinery and conditioned space but also results in a lower yield per kW expended, when compared to equivalent spun polyester yarn.
- Similarly, the weaving of cotton would require a higher level of humidity to be maintained than if it was a polyester weaving unit.
- The Ukg or energy units expended to produce kg of yarn for combed 40s cotton yarn is
- Fabric made from continuous filament polyester yarn requires less steps than spun polyester. SO the type of polyester fibre also makes a difference.
Energy consumed in the usage of textiles
- Conversion of finished fabric to garments or made ups in home furnishings
- Transport of finished fabric to cutting, stitching or embellishment units
- Transport, display and storage of finished textile products for the end user
- Storage and maintenance of textile goods by users – home and institutional
Somebody who has an education in textile manufacturing or has spent time in a composite spinning-weaving-processing mill will tell you that the space needed for converting a bale of cotton to finished fabric is a lot more than space needed to convert a bale of polyester into fabric.
The blowroom for cotton would have more variety of blenders, cleaners and openers than a blowroom line for polyester
The cards that convert opened fibre into a web of fibre that can be attenuated into sliver for further processing remove more weight from cotton than for polyester.
Combing a process that removes 16 or 18 per cent fibres from the cotton fleece is an additional process that applies only to cotton and not to polyester.
Extra energy has to be expended in not only making the additional machinery for cotton fibre processing but also maintaining temperature and humidity in a narrow band in the occupied space which obviously will be a lot more than for polyester fibre to yarn conversion.
In short, Ukg or electrical units consumed per kg of yarn produced is a lot higher for cotton than for polyester of same count and TM. South India Spinners Association has found out that to produce 40s count polyester 20 per cent less energy is consumed than for producing 40s cotton count.
Spinning and Weaving activities are not confined to salubrious environs of Coimbatore which naturally supports conversion of cotton fibre to fabric with minimal air conditioning. Fibre to Fabric conversion is done through the length and breadth of the country and that means the operating conditions require ambient temperature and humidity to be maintained in a narrow band to achieve good productivity and consistency in quality.
Not only does cotton require more energy to get converted into fabric, it also requires higher water usage and causes massive amounts of dyes and chemicals getting released into waterways if not treated and disposed of with ZLD plants.
The Water Footprint of Cotton Consumption report points out “consumers in the EU25 countries indirectly contribute for about 20 per cent to the desiccation of the Aral Sea”.
Cotton cultivation is not just labour intensive but also water intensive. It should be very concerning to textile industry policy makers that a research paper under UNESCO-IHE (Institute of Water Education) should term cotton textile exports as export of virtual water. As per this study, virtual water content that gets exported per kg of cotton textiles from India is around 21 litres. What is worse for countries like Egypt and Uzbekistan is that almost all of the water required for cotton cultivation is by diverting water from fresh water bodies, ie. Water that would have otherwise been used to grow food crops instead of a cash crop. What’s more this study reveals, “consumers in the EU25 countries indirectly contribute for about 20 per cent to the desiccation of the Aral Sea.”
Virtual water content of cotton products at different stages of production for the major cotton producing (m3/ tonne)
Source: ResearchGate
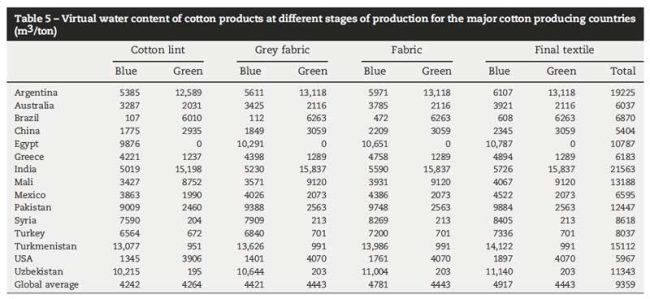
Cotton Australia, representative body of cotton growers in Australia, in 2013 reported water usage of 6-7 megalitres per hectare of cotton field, as compared to 11.5 Mlitres for paddy and 5.1 for fruit and nut trees.
In the Indian context, cotton fields are rain fed as well as irrigated. One might say that rainwater used in irrigation is not really used up. It is transpired back into the atmosphere or it runs aground to replenish aquifers but the pesticides and fertilisers that are so important for productivity and . So what our agriculture and textile industry policy makers should be concerned with is the irrigation water that gets diverted from food crops to a cash crop. The country average is 1.4 times higher than the global average for the irrigated water usage in the cultivation oc cotton as reported in this article by Mint. The top 3 states, in Mint that are better than the world average for efficient use of irrigation for cotton are Andhra, Gujarat and Maharashtra. In which states should cotton cultivation be incentivised and in which states it should not be is something that policy makers could do well to think about but that is another discussion altogether.
Returning back to the subject of this write-up, it is very interesting that finished dyed polyester fabric could be made with a fraction of the total water usage as compared to cotton with dope dyeing fibre(melt spinning of coloured fibre instead dyeing the fibre, yarn or fabric after it is baled for transport to textile mills). This is substantial saving of precious water.
Similarly, the printing of polyester fabric can be entirely water dry using the digital inkjet printing technique of printing on paper and then transferring the motif on fabric by heat press. This zero water usage technique of creating fashion has been adopted all over the world and continues to witness strong growth.
Let us celebrate the increasing share of polyester fibre in textiles.
Polyester fabric is generally not comfortable in warm humid clmates but in that area too fibres have been developed that make it a lot more . Sure, nothing is as comfortable as a cotton garment next to your skin but even
Printing yarn is a more recent and a brilliant innovation that adds colour to yarn as per a pre-set program for set lengths as short as a few cm if you like. Coloreel from Sweden has to be mentioned in this context and everytime the magic has been on display at various exhibitions for the last 2 years or so, there is a huge crowd staring at it in awe.
Finally what we scoff at is the touch and feel of polyester. Nature is supreme and cotton fibre is amazing. The gap in tactile supremacy of cotton over polyester is however reducing. It starts with the fibre, its denier and cross-section and ability to impart fuzziness or peach finish and of course, marketing makes polyester textiles a lot more acceptable.
Consumer also prefer polyester for its easy care properties. Requires less ironing, doesn’t soil or stain easily, dries quicker, lasts till you get bored of it. Those are not just reduction in domestic chores but also result in in reduced use of water for laundry, less energy to dry and iron. Bring in recycled PET and as per Common Objective Report, “Manufacturing rPET generates 79 per cent less carbon emissions than producing its virgin counterpart.”
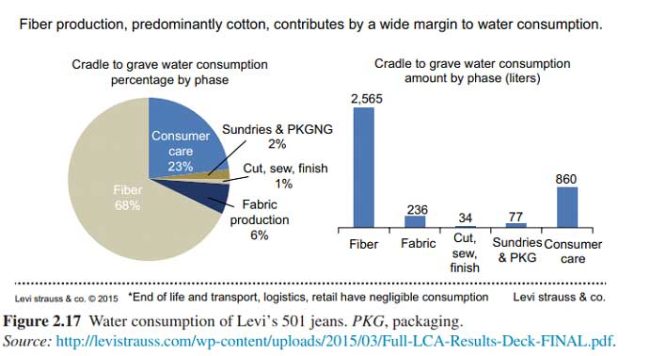
Figure 1: Water consumption of Levi’s 501 jeans. PKG = packaging.
Source: Levi Strauss
Fashion trends of the future will be more about the environmental impact than the bright and beautiful colours. Fashion is about making a statement. So how about the grey water footprint of the shirt I am wearing is more and more individuals want to stand out for their awareness and caring for the environment. So the next time you see an eco-warrior proclaiming all hail cotton, just point to the jeans he is wearing and point out that the half a kilo of cotton garment probably took 10,000 litres of water to get the cotton fibre for it and another 10,000 litres of water to give the form and look it is in. Had he opted for a polyester-blended denim fabric for the jeans, he could reduce the 10,000 litres that went into growing the cotton by 30 per cent perhaps. Further, if he bought jeans that were imparted colour and fancy wash effect with digital printing on ecru woven fabric using water based pigment inks, he would have probably reduced the total water footprint from 20,000 litres to 10,000 litres for the garment (see Figure 1).
References
⦁ https://www.commonobjective.co/article/fibre-briefing-polyester
⦁ https://ourworldindata.org/grapher/cumulative-global-plastics
⦁ In a barrel of oil – Energy Education
⦁ https://hempfoundation.net/7-major-fibers-textiles-in-the-world-and-their-carbon-footprint/
⦁ Can fashion ever be sustainable? – BBC Future
⦁ http://www.sispa.in/wp-content/uploads/2017/05/Sitra-Conversion-Guide-Lines.pdf
⦁ https://www.researchgate.net/publication/228377230_The_Water_Footprint_of_Cotton_Consumption
⦁ https://www.livemint.com/Opinion/vZ3FOtNe9m0XCm0U7J5XxN/Indias-farms-have-a-far-worse-scorecard-on-water-use-than-I.html
⦁ https://www.commonobjective.co/article/fibre-briefing-polyester
About the author:
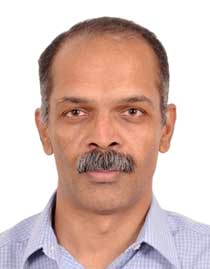
Kamal Kulshreshtha is a specialist in industrial sales and marketing. He is a Textile Engineer with PGDBM having some 25 years of rich cross-functional experience in B2B sales and marketing of project sales and concept sales. He has contributed to the textile and plastic packaging industries in Indian and international markets, with a penchant for incisive insights. Kulshreshtha has widely travelled with rich exposure to businesses spanning cotton spinning, worsted spinning, melt spinning, and cultures across the globe, from Japan to Latin America, through Europe. An avid participant on Linkedin he has published works to his credit in overseas publications as well.