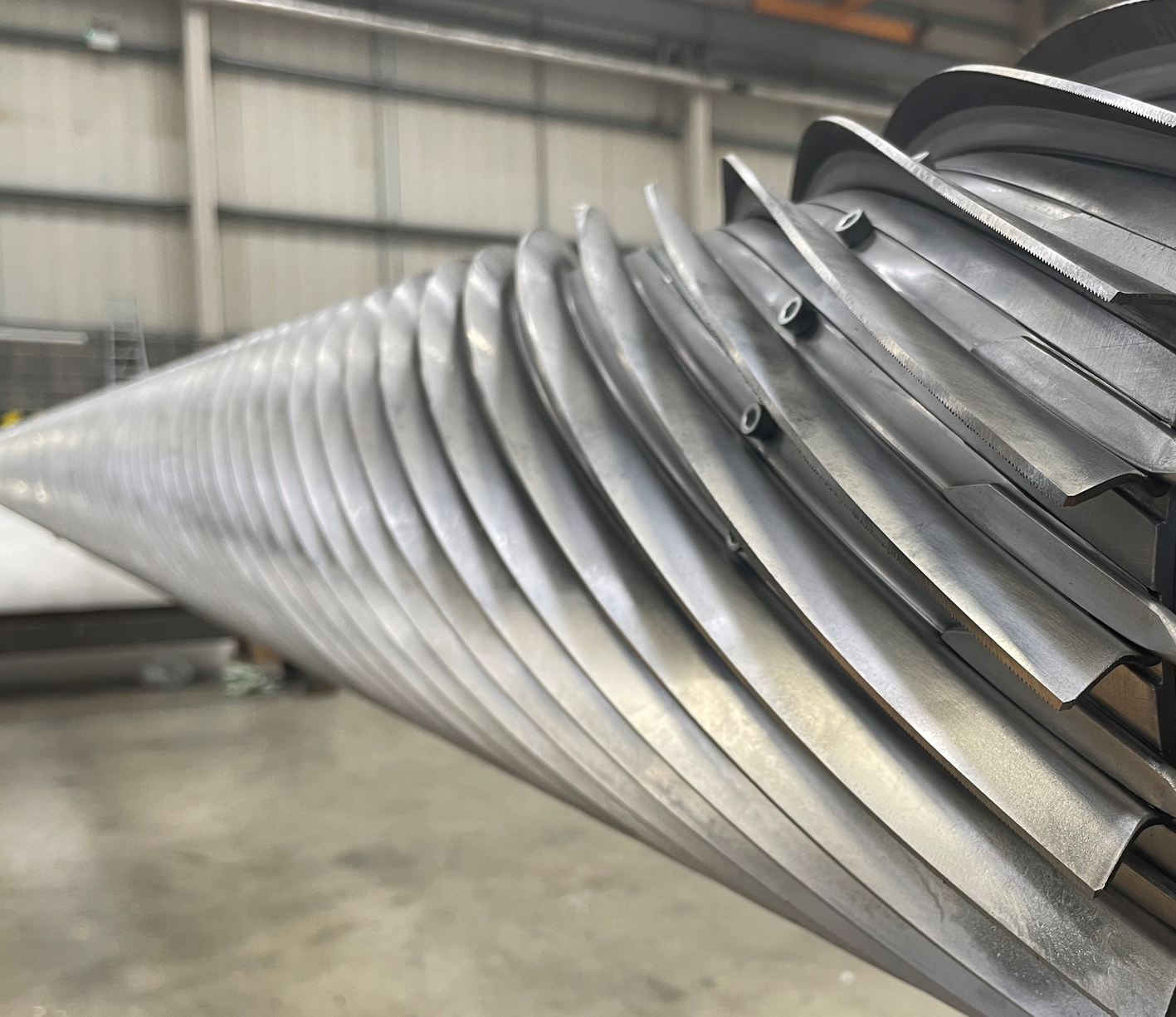
BTMA member Sellers Textile Engineers unveils Hybrid Shearing Cylinder
The Hybrid Shearing Cylinder will become standard on our latest machines and also be made available for retrofitting, to provide significant benefits to our existing users, says Neil Miller, Director, Sellers.
BTMA member Sellers Textile Engineers is marking its 110th anniversary this year with the introduction of an entirely new concept in carpet shearing, as the essential final step in ensuring tuft uniformity and ‘just new’ freshness in finished carpet rolls.
The company has for many years offered two options in the construction of its shearing cylinders – the first, namely the ‘strap-on’, incorporates spiral blades bolted to the cylinder body and the second, known as the ‘caulked-in’ ,includes spirals which are fixed very securely in a machined groove within the machine.
The new Sellers’ Hybrid Shearing Cylinder combines the benefits of both, resulting in an improved cut and finer finish, in addition to longer repeatable finishing and increased rigidity.
“The Hybrid Shearing Cylinder has all the advantages of the ‘strap-on’ spiral blade to provide a sharper and cleaner cut, along with enhanced rigidity which significantly lengthens the intervals between the necessary regrinding of the blade,” explains Neil Miller, Sellers Director. “We currently have six Hybrid Shearing Cylinders operating in the field and the earliest, which has been installed in both No1 Head position, where the majority of the shearing operation and heaviest cut is performed, and also in No3 Head, where the sharper cutting angle has resulted in a much improved surface quality.”
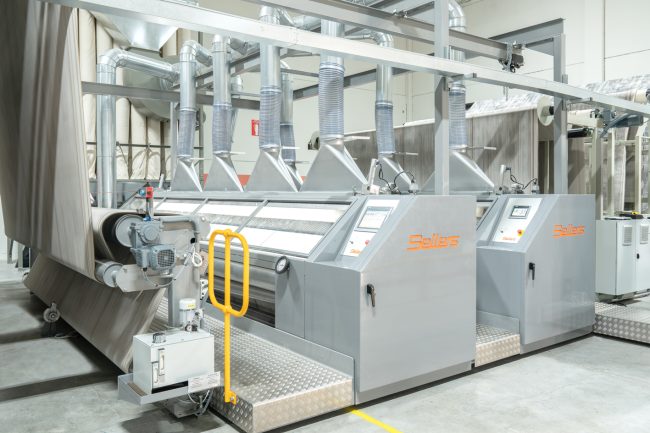
The latest advanced features of these machines include a load cell tension control drive system, an automated touch screen for easy operator control and fault diagnosis, an enhanced cleaning system including cylinder and blade separation and fully controllable pivoting beds. Further options include thickness monitoring, seam detection and metal detection systems.
Sellers shearing machines have led the field in carpet finishing for many decades, enabling the leading manufacturers to stay competitive by enabling the highest quality of finish to be achieved economically and efficiently.
“The Hybrid Shearing Cylinder will become standard on our latest machines and also be made available for retrofitting, to provide significant benefits to our existing users,” says Miller. “All of our equipment is designed, manufactured, assembled and tested at our plant in the UK, and as one of the few remaining European engineering companies to make all of our components in-house – with now over a century of accumulated know-how – flexibility in design allows our finishing solutions to be targeted to specific customers and their product requirements. Aligned to this is a lead in process control systems which ensure the accurate control, reliability and repeatability of the processing parameters on all of our machines.”
Sellers remains committed to providing complete finishing solutions for all carpet, tile and artificial grass products. Its range includes machines for tufted secondary backing, both conventional, powder and extrusion lamination, Wilton and Axminster products, artificial grass and foam lines, coating lines for bitumen, PVC, PU and other polymers, as well as shearing for all carpet products.
Ongoing developments on the company’s coating and drying lines have resulted in improved guiding and product tension control as well as dryer efficiency, reducing heat loss and optimising energy use. These include a re-design of the fan pressure boxes and impingement nozzles to increase airflow efficiency, modulating gas burners and introducing easy clean, accessible filters.
In addition, the proven dual zone system has been enhanced, giving a temperature differential of up to 80°C between top and bottom zones. Dryers can be heated by either gas or steam and operation and access have been simplified with controls via touch screen and PLC.
An extensive range of ancillary equipment is available to provide maximum flexibility to cover product requirements, for both new processing lines and as upgrades to existing equipment.
“Carpet manufacturing is now based on well-established, tried and trusted processes and it’s rare for new innovations to be introduced into this sector,” says Jason Kent, CEO, British Textile Machinery Association. “The new Sellers Hybrid Shearing Cylinder can provide a competitive edge for manufacturers which is currently being proven in the field. It’s one of a number of new innovations the company is planning to showcase at next year’s ITMA exhibition in Milan.”
Sellers1
Sellers2
FOOTNOTE TO EDITORS
Issued on behalf of the BTMA by AWOL Media.
For further information please contact:
Adrian Wilson AWOL Media 19 Sandal Cliff Wakefield, West Yorkshire WF2 6AU, UK Tel: +44 7897913134 e-mail: Adrian@awol.media.co.uk www.awolmedia.co.uk | Jason Kent CEO, BTMA City Heliport, Liverpool Road, Eccles, Manchester, M30 7RU UK Tel: +44 (0)161 707 0209 e-mail: info@btma.org.uk www.btma.org.uk |