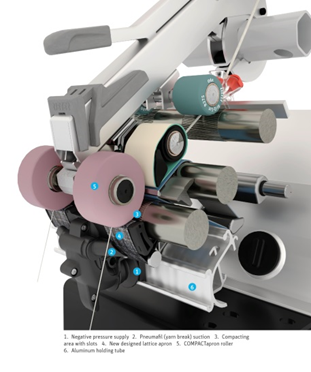
3D compacting pushes the limits of yarn strength
By reducing conversion cost by 10 per cent, COMPACTapron is the right system for competitive spinning mills.
COMPACTapron, the latest addition to the Suessen compacting family, sets a new benchmark for yarn tenacity with an additional 0.5 to 1 cN/tex compared to other compacting systems. By reducing conversion cost by 10 per cent, COMPACTapron is the right system for competitive spinning mills.
COMPACTapron makes compact spinning more affordable. It offers the right balance between high productivity and low operational costs without compromising on quality. Most importantly, this latest compacting device reduces electricity costs. The system is suitable for most machine types and common materials including blends from yarn counts Ne 20 to Ne 80.
Low conversion costs
The design of COMPACTapron (Figure 1) makes it a formidable asset to reduce the cost of conversion. It features only one big cot, resulting in 50 per cent less maintenance time and almost no lapping. As COMPACTapron needs very few consumable parts, it has a very low spare parts cost per spindle per year. The optimised suction slot allows reduced air flow and power demand and thus contributes to 60 per cent energy saving.
High yarn tenacity and excellent quality
Yarn strength is crucial in determining the quality of the final spinning product. Thanks to 3D technology, COMPACTapron transports fibres in the condensing zone over the suction slot in a distinctive distance to the mesh apron so that all fibres are entirely compacted. The distance between the nip lines of COMPACTapron is shorter than the shortest fibre so that fibres are smartly guided through the compacting zone, thus achieving better yarn strengths compared to competitors. The overall result is an additional 0.5 to 1 cN/tex, a yarn tenacity unmatched in the market.
Flexibility
The improved raw material yield gives spinners more options to optimize cost so they can choose between twist reduction to enhance productivity, adjusting the raw material mix, or obtaining a higher selling price in downstream processes.
With less energy requirement, less maintenance and fewer spare parts, COMPACTapron not only boosts yarn tenacity, it gives spinning mills a real competitive edge.
About Rieter
Rieter is the world’s leading supplier of systems for manufacturing yarn from staple fibres in spinning mills. Based in Winterthur (Switzerland), the company develops and manufactures machinery, systems and components used to convert natural and
man-made fibres and their blends into yarns in the most cost-efficient manner. Cutting-edge spinning technology from Rieter contributes to sustainability in the textile value chain by minimizing the use of resources. Rieter has been in business for more than 225 years, has 18 production locations in ten countries and employs a global workforce of around 5 590, about 16.4% of whom are based in Switzerland. Rieter is listed on the SIX Swiss Exchange under ticker symbol RIEN. www.rieter.com
About Suessen
Suessen, the world’s leading manufacturer of spinning systems and components for spinning machines, is a subsidiary of the Rieter Group. The company, based in Suessen (Germany), creates customer value through system expertise, innovative solutions, after-sales excellence and global presence. The considerable investments in R&D ensure the further development of technical and technological components in an uncompromising and resolute manner. The focus is on universal applicability, improved yarn quality, increased service life, reduced maintenance and proven reliability in industrial application. www.suessen.com