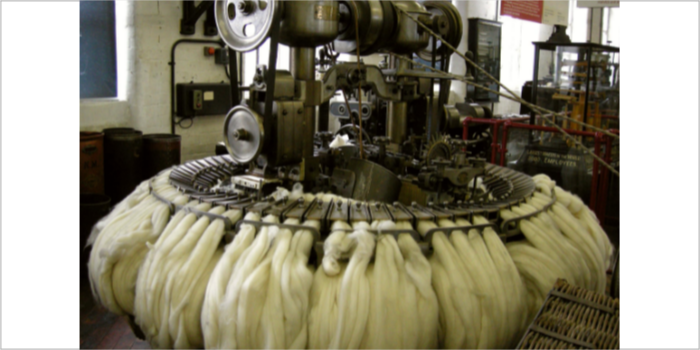
AFIS-driven combing system: Spinning profit and quality
Most spinners experience quality inconsistency. However, the ‘right first time and every time’ concept is possible with cotton spinning. TG Sarathy, in this article, explains a new perspective on the comber process assuming that other machines in the flow are set alright.
One of the big challenges faced by the cotton spinners is consistency in spinning performance and finished yarn quality irrespective of inconsistent natural raw material (cotton) quality. To improve the yarn quality, it is a must to improve the raw material quality. In this process, we are all aware that comber is the only machine in eliminating the selected short fiber in the spinning process sequence. To utilise this machine optimally one should think “Are we using this machine in the right perspective! Did the noil (comber waste) extracted is correspond to the quality achieved! Are we getting consistency in yarn quality in combed count throughout the year at the minimum cost of quality?”
But in reality, most of the spinners experienced for sure that the quality is inconsistent and struggling to maintain it on many occasions. They experience a lot of surprises in spinning performance and quality. However, the ‘Right first time and every time’ concept is possible with cotton spinning! This article explains a new perspective on the comber process assuming that other machines in the flow are set alright. Many spinners are fixing stringent standards from raw material to finished products and try to ensure it within standard limits. In practical fails several times when the cotton lots are replaced. In this article, we are sharing Texcoms Textile Solutions’ global experience in various mills based on a comprehensive study on how to maintain consistent yarn quality in combed counts throughout the year practically through “AFIS (Advanced Fiber Information System) driven combing system”.
1.0 Basics of combing process
Combing is an additional process to produce finer, smoother, lustrous yarn by way of upgrading the quality of raw material, at the cost of additional expenditure on machines, floor-space and personnel, together with a loss of raw material. Comber eliminates precisely pre-determined quantity of short fibers, fiber hooks, remaining impurities, foreign materials, neps and produce a sliver with maximum possible evenness with more straight and parallel fibers.
2.0 Current industry practices
In the general mill practices, as a part of the “in-process quality assurance system,” the comber noil percent is checked in a predetermined testing schedule. It is maintained within a specified tolerance limit say +_ 0.5% between combers. Whenever Comber noil percent goes beyond mill tolerance limit the same will be brought to mill standard level. To bring the comber noil to standard level, mill technician normally readjusts the noil index, top comb setting, etc., in individual combers. This results in deviation of the setting uniformity between combers to maintain standard noil per cent. Thus, various combers in the same process have widely varying noil index setting to maintain standard noil per cent.
3.0 Guidance for process engineering
In a normal mill practice, set the comber parameters based on raw material specifications and finished product quality requirements while introducing new cotton mixing. The extraction of comber noil per cent was also fixed with this baseline. But eventually, the comber noil per cent varies in R&D tests after some time. There are two types of noil variations in the modern comber shed:
a) Shed average comber noil per cent
b) Noil variations between comber
First of all, let us find the reason behind the noil variation in each type. Probable causes for variation in overall shed average comber noil per cent beyond tolerance limit are lap weight variations and variation in feed lap short fiber per cent (SFCn or short fibre content in numbers). Certainly, lap weight variations can be narrowed down by process control in carding, pre comber drawing and lap former. Overall, average comber waste shall be maintained within the tolerance of +_ 0.2%.
The progressive wear of comb components, such as the pins in the circular and top combs, or a decrease in the pressure between the drawing-off rollers or nipper jaws, non-uniform setting, shortened unicomb brush height, condition of the nipper, mechanical conditions and process parameters can each significantly affect noil produced during combing between combers in the identical process. Waste variation between comber could contribute to Yarn Imperfections and strength variations. Comber waste variation between combers should be maintained within the tolerance of +_ 0.5%.
Inadequate knowledge and skill lead to not following standard-setting procedures, use of standard tools and sometimes constraints of time results in the low level of setting accuracy. The waste at comber can be reduced by increasing pre comber draft up to a certain limit without affecting the resultant yarn quality. It is often more economical to run the card at a somewhat low production rate than to take out extra comber waste. The noil is a sensitive variable of the combing configuration and is also influenced by comb speed variation, fibre alignment and the incidence of hooks, variations in sliver linear density, pre-carding conditions, different mean fibre lengths and a back draft applied at the first operation after carding. The process parameters which decide the amount of noil per cent are the type of feed, feed amount/nip, detaching distance (the distance between the detaching roller nip to the bottom nipper nip), type of top comb and amount of top comb penetration.
4.0 AFIS driven quality system
If the comber and back process is set precisely (i.e. the similar detaching distance (Noil index), Uni comb & top comb setting, comber speed, feed/nip, type of feed and lap weight), the comber machine delivers consistent sliver quality. But the noil per cent may increase or decrease according to infeed short fibre variations.
Comber noil going down in the same preset conditions represents identical yarn quality with noil savings. Likely, comber noil is going up in same preset conditions represents same yarn quality with higher noil per cent due to increase in input lap short fibres or process deficiency. The feed short fibres may go up due to raw material quality variations and incorrect process engineering. The back process shall be checked and corrected before fixing on a comber. AFIS-driven quality system supports yarn quality sustenance, process reengineering, machine setting accuracy and improves yarn recovery. Quality sustenance ultimately pays a premium price and repeat orders. AFIS driven quality system is the only way to achieve this milestone in the competitive market.
5.0 How can we control the combers on day-to-day basis
The following parameters are tested in AFIS – driven quality system in combing process to monitor and control the process on day-to-day basis:
5.1 Comber sliver short fibers (SFCn): Comber sliver shall be tested in AFIS instrument and AFIS standards shall be fixed against current practice of fixing standard comber noil per cent. Readjusting the comber noil unknowingly to maintain standard noil level leads to yarn quality variations.
Fix standards for neps,5% length and SFCn for each process according to the finished yarn quality requirements and customer acceptance level. Fix tolerance limit for Go and No Go. The proper place for controlling neps is carding and not combing. There is a limited scope of reducing neps in comber. Five per cent length varies according to raw material variations and can be controlled with the best quality management system in raw material procurement and bale/lot management. Although Comber feed lap SFCn is affected based on raw material quality management system, comber being a short fibre removal machine is ensuring uniform output sliver SFCn by readjusting the noil level automatically. Focus on raw material SFCn and uniformity index helps to narrow down the variation in comber noil to the maximum extent. Practically in most of the mills, the neps and 5% length are under control. But short fibres are varying widely in cotton from a few stations /varieties which shall be monitored and maintained within industry-standard acceptance level. The mixing issue shall be done with a comprehensive analysis of cotton lots, stations, varieties and of course cotton specifications to average out quality as well cost. Despite all our sincere efforts for consistent raw material quality, cotton is a natural fiber that will have variations. Mills are testing around 0.001% of a representative sample in every cotton lot. Best sampling system and standardized testing procedures shall be formed to match the sample results with bulk cotton supply.
5.2 Comber noil short fibers (SFCn): Short fibers in comber noil shall be tested at fixed intervals. Comber waste should contain at least >80 % short fibres (SFCn) to minimise good fibre loss. In our study, it is observed that few mills are maintaining even 60% Short fibers in comber noil and losing considerable good fibres. The loss amounting to INR 0.5 to 2 /Kg at raw material cost of INR 130/Kg. The waste at comber needs to be checked and controlled due to the following reasons: More waste than the nominal means financial loss. Less waste than the nominal could lead to unacceptable yarn quality performance. More removal of short fibres and neps may not always contribute to yarn quality or performance. The high cost of removing even one percent extra comber waste makes it vital that a mill should carefully choose the optimum level of comber waste for each mixing and then exercise a strict control on all combers to maintain the waste at the desired level. During our study, it was observed that there is a good scope of minimising the manufacturing cost for the required yarn quality with a perfectly set combing process.
5.3 Comber short fibre removal efficiency per cent (SFRE%): The short fibre removal efficiency per cent is defined as the the percentage of eliminated short fibres (SFCn) compared to feed short fibres (lap SFCn) in the Combing process. To schedule testing of short fibres in comber lap, combed sliver and comber noil to improve combing performance. SFRE per cent in modern combers normally ranging between 55 to 70%. Process reengineering is the base to improve it dramatically. Surprisingly, the data checked in mills is ranging between 35 to 50% only due to lack of awareness or testing facility. To compensate for such low values, the mills, encourage to extract higher comber noil by 1 to 4 % to maintain the same quality. Increasing the top comb penetration, disturbs the combed fringe though it increases the combing efficiency and reduces yarn imperfections, but the classimat long faults and unevenness of the fabric increases. The study reveals that short fibre removal % and % improvement in mean length are higher with forward feed as compared to that with backward feed at any level of noil.
CATEGORIES Automation