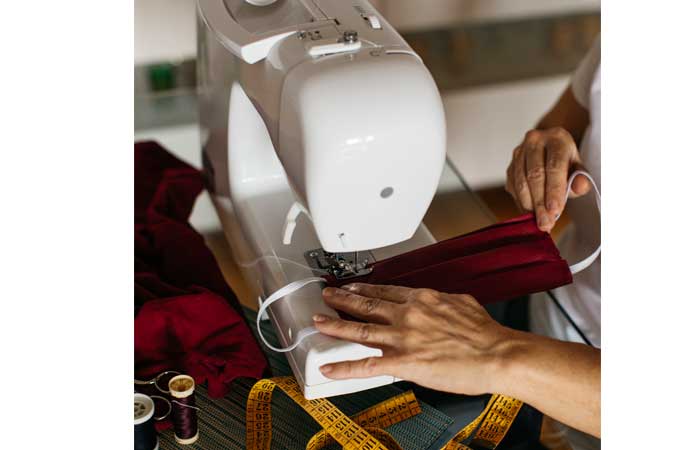
Transforming textile manufacturing through customer-centric approach
Every organisation has a distinct culture that shapes its progress and defines its identity. Culture is formed by the collective behaviours and attitudes of its people, and it can be deeply ingrained in well-established companies, requiring significant effort to change. In newer entities, culture often originates from the habits and management styles of its owners, which then influences the behavior of others within the organisation. When new employees join, they adapt to this culture and become part of its fabric. As a company grows, its culture becomes more consolidated.
One essential aspect of a company-wide culture is customer focus. It involves a deep understanding of customer needs and a commitment to satisfying those needs. Walmart serves as an excellent example of a customer-focused culture. Founder Sam Walton built a small grocery store into the retail giant Walmart, amassing a fortune of over $23 billion. His guiding principle was to treat the customer as king. This mindset led to the implementation of numerous customer-friendly practices, with signs in every store displaying “satisfaction guaranteed.” By prioritising the customer and empowering them, Walmart set itself apart from other retailers. In India also, there are many companies that follow the customer centric approach, that adding value to their operations.
Customer focus is not merely a department or a set of tactics; it is a fundamental cultural mindset that permeates the entire organisation. By embracing customer focus, companies can build strong relationships, enhance loyalty, and stay ahead of the competition in an ever-changing market landscape.
“The purpose of a business is to create and keep a customer.” – Peter Drucker
Understand your customers
Understanding customers is crucial in any business, including the textile industry, where each stage of the value chain serves as a customer to the preceding one. The textile value chain begins with sourcing raw materials, such as natural fibres like cotton, wool, or silk, or synthetic fibres like polyester and nylon. These fibres are spun into yarn, then woven or knitted into fabrics. The fabrics undergo dyeing, printing, and finishing to achieve the desired colours, patterns, and textures. They are then cut, sewn, and assembled into garments or home textiles. Finally, finished products are distributed through wholesalers, retailers, or digital platforms. This multi-stage process involves diverse stakeholders, each influencing quality and efficiency. Understanding this chain enables businesses to optimise production, improve customer satisfaction, and enhance overall competitiveness.
While it’s often the role of sales and marketing teams to interact directly with customers, adopting a customer-centric approach is essential for all members of the organisation. Collecting and meticulously analysing diverse data types, including product specifics and customer feedback, can enrich the understanding of customer needs and preferences. Carrying out measures like surveys or evaluations can offer precious insights into how customers perceive your business. Sharing these findings across the organisation is critical, as it guarantees all teams are aware of customers’ feedback and can collectively contribute towards enhancing customer experience. This holistic approach can instigate improvements at every stage of the textile value chain, eventually leading to a product that surpasses the expectations of the end customer.
Effective communication between various stakeholders – suppliers, producers, and end-users, is a cornerstone of a successful management system in the industry. As a spinner, your clientele may comprise of weavers, knitters, value addition groups, and garment manufacturers. Weavers can further be sub-categorised into greige yarn weavers or dyed yarn weavers, whereas knitters might be circular or warp knitters, who may work with either greige or dyed yarn. Cultivating transparent and open communication with these customers ensures their specific requirements are comprehended and fulfilled, paving the way for a reciprocally beneficial business relationship.
Customer satisfaction
The likelihood of making a sale to a satisfied customer is 60-70 per cent, whereas the probability of selling to a new customer is only around 20 per cent. This clearly demonstrates that it is much easier and more advantageous to conduct business with satisfied customers compared to acquiring new ones. In fact, the cost of acquiring a new customer is estimated to be 4-6 times higher than retaining existing customers.
The ultimate success of any company relies heavily on the satisfaction of its customers. Regardless of the stage at which a company is in its development, customers should always be given top priority before profits. Customer satisfaction serves as a crucial indicator of future sales, as satisfied customers are more likely to continue doing business with the same company.
Understanding customer requirement
Fibre manufacturing: Fibre manufacturers, whether producing polyester or viscose, primarily cater to spinners, who rely on fibre quality for efficient yarn production. Spinners prioritise smooth machine operation, aiming to prevent issues like lapping, fly generation, and breakages that disrupt production and waste raw material. Consistency in fibre characteristics such as length, strength, fineness, uniformity, elasticity, cleanliness, maturity, and colour is crucial, as these directly impact yarn quality, influencing its strength, smoothness, softness, lustre, resilience, and dye absorption. Ensuring stable fibre properties enhances both processing efficiency and the performance of the final yarn.
Spinning: When it comes to yarn, customers place significant importance on two critical parameters: strength and unevenness. Low yarn strength can have several negative implications. Firstly, it leads to lower efficiency in subsequent processes, as weaker yarns are more prone to breakage during weaving or knitting. Each break adds a fault to the fabric, affecting its appearance and overall quality. Additionally, low yarn strength results in lower fabric strength, limiting its suitability for certain applications that require higher durability.
On the other hand, higher yarn unevenness has its own set of consequences. It leads to poor fabric appearance, as uneven yarn results in inconsistencies in the fabric’s surface. This can be visually unappealing and affect the overall aesthetic quality of the fabric. Furthermore, high unevenness negatively impacts the fabric’s handle, making it feel rough or irregular. This can result in a diminished level of comfort and satisfaction for the end consumer. Additionally, yarn unevenness can contribute to defects in the fabric, compromising its structural integrity and potentially reducing its lifespan.
Weft yarn: In weft yarn, specific standards must be met to ensure smooth weaving operations. A critical parameter is the breakage level, which should not exceed one break per 100,000 meters of weft insertion. Even a single weak spot in every 24 cops of 60’s count yarn can lead to weft breaks during weaving. Additionally, breaking force and elongation are key factors, as they determine yarn strength and stretchability. Consistency in these properties is crucial to maintaining fabric uniformity and overall quality.
Another important consideration is Classimat, which classifies yarn defects, identifying weak spots or potential breakage points. This system enables better quality control by detecting and quantifying defects, ensuring that only yarn meeting acceptable standards is used in weaving. By carefully monitoring these parameters, manufacturers can minimise breakages, enhance weaving efficiency, and produce high-quality fabrics that meet customer expectations.
Warp yarn: Warp yarn must meet specific standards to ensure smooth warping and weaving processes. A critical parameter during warping is the end breakage level, with a good standard being less than 0.4 breaks per 1,000,000 meters for combed yarn and less than 0.8 for carded yarn. In weaving, breakages should be kept below 0.4 per 1,000 warp threads and 100,000 picks to enhance efficiency and productivity.
Hairiness and its variations are also crucial, as excessive loose fibres can affect fabric appearance. Controlling hairiness ensures a smooth, uniform surface and high-quality fabric. Meeting these warp yarn requirements through strict quality control minimises breakages, optimises production efficiency, and ensures fabrics meet customer expectations.
Knitting yarn: Knitting yarn must meet specific requirements to ensure smooth processing and high-quality fabric. While strength is a secondary consideration, it should be sufficient to withstand the forces exerted during knitting and fabric use. Elongation and elasticity play a crucial role in accommodating the stretching and recovery needed during knitting, helping maintain fabric shape and structure. The absence of weak and thick places is essential, as inconsistencies can lead to holes in the fabric or damage knitting machine needles. A low friction value of around 0.15 m is desirable to minimise resistance between the yarn and the knitting machine, ensuring smoother operation. Maintaining uniform moisture content is also critical, as fluctuations can cause yarn breakage, uneven tension, and fabric distortion. A relatively high and consistent hairiness value is preferred, enhancing fabric feel, appearance, and resistance to pilling. Additionally, knitting yarn typically has a lower twist level, contributing to a softer handle and better drape. Yarn evenness is vital for a uniform fabric surface, while a low count coefficient of variation (CV) ensures consistency in yarn thickness, improving overall fabric quality. Meeting these parameters is essential for achieving efficiency in knitting and producing superior knitted textiles.
By ensuring that knitting yarn meets these requirements, manufacturers can produce high-quality knitted fabrics that exhibit good strength, elasticity, uniformity, and handle. Meeting these specifications contributes to the overall performance and aesthetic appeal of knitted garments and textiles.
Fabric: The quality of the base fabric is instrumental in determining the outcome of fabric processing, including dyeing, printing, and finishing stages. A primary aspect is uniformity; the fabric must exhibit consistency in weave density, yarn composition, and weight, as any discrepancies may result in uneven dye or print application, leading to defects in the final product. Cleanliness is equally vital, as impurities such as dust or oil stains can interfere with dye absorption, causing spotting or staining. Strength and durability are also key parameters, ensuring the fabric withstands the various chemical and mechanical treatments involved in fabric processing without sustaining damage. Additionally, absorbency plays a crucial role, as the fabric must effectively and evenly absorb dyes and finishes to prevent inconsistencies in color and texture.
Fabric structure, including the weave and yarn count, must be suitable for the intended processing technique and final product specifications, as certain weaves or yarn types may be incompatible with specific dyeing or printing methodologies. Controlling fabric shrinkage is another critical factor, requiring preconditioning or pre-shrinking to prevent size variations during subsequent processing stages. Furthermore, the fabric must be free of defects such as holes, tears, or loose threads, which could become more pronounced during processing and compromise the aesthetics and quality of the finished textile. Ensuring these parameters in the base fabric enhances the efficiency of fabric processing and contributes to the production of superior-quality textiles.
Garmenting: The selection of fabric in garment manufacturing plays a crucial role in determining aesthetics, functionality, and comfort. An ideal fabric should have excellent drape and flexibility, conforming to body contours for a better fit and ease of movement. Dimensional stability is essential to retain size and shape through wearing, washing, and ironing. Durability and strength ensure the fabric withstands manufacturing processes and daily use. Absorbency and colourfastness are key considerations, along with ease of care, favouring machine-washable, quick-drying, or wrinkle-resistant fabrics. With growing emphasis on sustainability, fabrics with minimal ecological impact, recyclability, or biodegradability are gaining importance. Ultimately, fabric selection must meet diverse criteria to produce high-quality, visually appealing, and comfortable garments.
Measuring and achieving customer satisfaction: Key factors to consider
Customer satisfaction is a subjective aspect that varies across industries and individual customers. As a business, it is crucial to actively measure the level of customer satisfaction to ensure continuous improvement. Monitoring customer feedback and assessing whether their requirements have been met is an integral part of a quality management system. Customer satisfaction has a direct impact on customer retention, and the quality of products and services plays a significant role in shaping customer perception and success in the market.
To achieve customer satisfaction, meeting customer requirements is essential but not sufficient. Falling short of meeting expectations is likely to result in disappointment. Key attributes of customer satisfaction can be summarised as follows:
- Product quality: Ensuring that the products meet or exceed customer expectations in terms of performance, durability, and reliability.
- Delivery process and packaging: Providing efficient and reliable delivery services, along with appealing and protective packaging for the products.
- Timely delivery: Keeping commitments made to customers regarding delivery timelines and meeting their expectations.
- Price: Offering products and services at a competitive and reasonable price point that provides value for money.
- Responsiveness and complaint resolution: Being responsive to customer concerns, promptly addressing complaints, and effectively resolving any issues that may arise.
- Communication, accessibility, and attitude: Maintaining open and clear communication channels with customers, being easily accessible, and demonstrating a positive and customer-oriented attitude.
By prioritising customer satisfaction, businesses can strengthen their reputation, build loyalty, and drive long-term success. Identifying customer expectations requires periodic reviews, market studies, personal visits, informal conversations, and satisfaction surveys. A suitable strategy or combination of techniques should be chosen based on the customer base and available resources. Regular assessment of expectations and effective measurement methods enable businesses to refine their offerings, address key concerns, and enhance overall customer satisfaction, ensuring sustained growth and competitiveness.
Quality is when the customer returns, not the goods.
About the author:
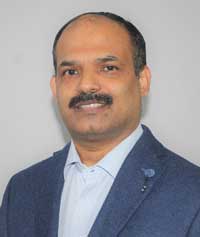
A Textile Engineer by profession, Manoj Kumar is having more than 25 years of industrial experience both in India and abroad. Presently he works at a Public Sector Company in a senior management position. He discovered a passion for writing after long years of industry experience on subjects close to his heart, i.e., management and wellness, offering creative solutions for success and happiness.