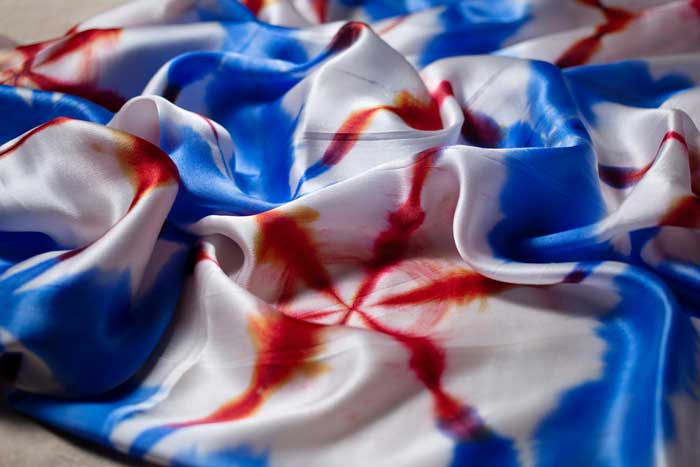
Water-saving dyeing and finishing techniques
Some countries have adopted sound wave technology of dyeing by using sonication technique of dyeing in very short time, informs Amarjeet M Daberao and Dr Vijay S Shivankar.
Water consumption is one of the major concern in textile processing industry where utilisation of water and it proper circulation in the industry is required to be controlled for minimum utilisation. It has been tried with several experimentation to reduce the consumption of water from pre-treatment to post treatment process, but not any reduction in the amount of water have been found, where as it was suggested that in the prior stage of pre-treatment, the water required for rinsing and neutralisation can be minimised if we can carry this process after the particular treatment and complete this process at end of the dyeing we can save at least 100 litres of water per kilogram of the fabric. It was studied that approximately 120 to 150 litres of water is consumed in dyeing of cotton fabric and according to this system we can save at least 20 to 50 litres of water per kg of dyeing. This saving of water at preliminary stage is not only improving the quality of dyeing but also exhibit excellent color fastness properties like fastness to light, washing, rubbing and perspiration according to standard.
The degradation and loss of fresh water ecosystem have consequences which are affecting bio diversity ecological stability. Textile industry is consuming water in dyeing and finishing department, along with water it is also Consuming high concentrated salt, alkali and dye which are not utilised completely in the dye bath during exhaustion, the prepared solution can dye the fabric but the effluent which is coming out in drainage water from the dyeing section contain unused dyes and salts which are completely going in wastage, thus increasing eh load on effluent exhibiting high BOD/COD. Fresh water is considered as a vital resource for all lives on the earth which are supporting human being and overall health of the planet, so it is our prime responsibility to keep the environment clean and reduce the hazardous effect on the environment which is blown in the river and sea water from various industries.
Some countries have adopted sound wave technology of dyeing by using sonication technique of dyeing in very short time. Implementing water saving process in dyeing of fabric with reactive dyes on cotton fabric is very necessary, however there are some places which are having scarcity of water and this leads to faulty and defective dyeing. Some countries which are not able to use water in dyeing due to unavailability needs to switch on other method of dyeing, this country have developed a technology of dyeing by using supercritical carbon dioxide instead of water. This dye does not require water to dye the fibre but they can utilise Co2 for dyeing and this may give poor colour shade, however supercritical Co2 required high pressure for dyeing and thus we can remove the consumption of water in dyeing department. Another method of saving water is by doing cationic modification of cotton fibres which improves dye absorption and reduce salt consumption; however, care is required to be taken for minimum utilisation of the auxiliaries. In this methodology sound energy is utilised to agitate particles dyes in a liquid, this ultrasonication can be conducted where we can prepare ultrasonic bath either for dyeing or for application of any critical finish on the fabric, however this is suitable for only small sample dyeing and found to be versatile for consuming less amount of water in dyeing.
About the author:
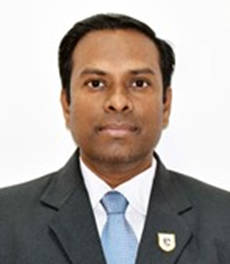
Prof Amarjeet M Daberao is the Assistant Professor and has done his M Text (Textile Technology) from DKTE, Ichalkaranji, Kolhapur. He has also done his B Text (Textile Technology) from VJTI Matunga Mumbai.
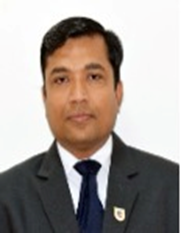
Dr Vijay S Shivankar is In-Charge Associate Dean for the Centre for Textile Functions. He is a PhD (Textile Fibre) from Sant Gadge Baba Amravati University, Amravati. Shivankar is also a MTech (Textile Technology) from Shivaji University, Kolhapur and a B Text (Textile Engineering) from Sant Gadge Baba Amravati University, Amravati.