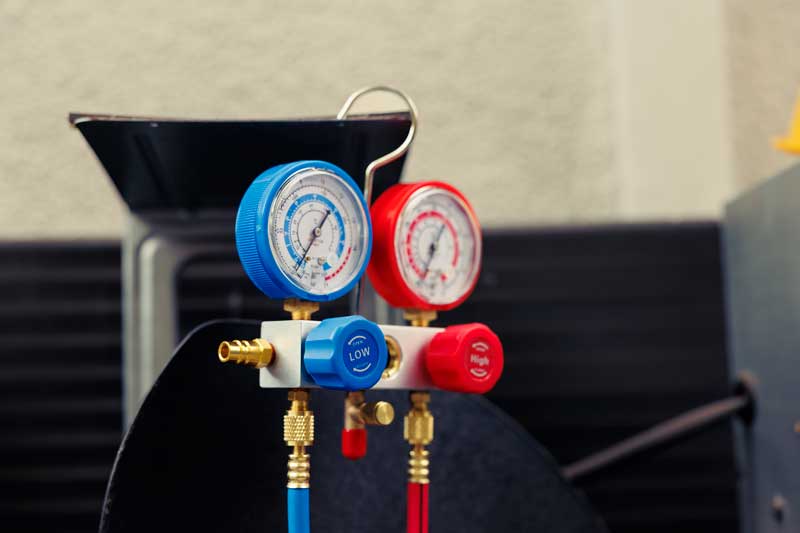
Cutting Energy Costs in Textile Manufacturing
Textile manufacturers can substantially reduce energy costs by investing in efficient air compressors, says Thomas Paulose.
Energy costs are significant in textile manufacturing, consuming a large portion of operational budgets. With growing pressure on businesses to reduce carbon footprints and operate sustainably, textile manufacturers are increasingly looking for ways to optimise energy use. One often overlooked opportunity lies in the efficient use of air compressors. These vital components play a critical role in textile production processes, from powering machines to aiding in pneumatic transportation. By optimising the performance and efficiency of air compressors, textile companies can realise substantial energy savings, improve operational efficiency, and contribute to sustainability goals.
Compressors powering textile production
Air compressors are widely used across the textile industry, particularly in spinning, weaving, dyeing, finishing, and packaging. Their primary function is to provide compressed air for various applications, such as powering pneumatic tools, operating machines, controlling automation systems, and ensuring material handling. The smooth operation of processes like air-jet spinning, automated weaving looms, and pneumatic transportation of fibres and fabrics depends heavily on compressed air.
For example, air compressors are used to propel fibres through the spinning process, ensuring precision and speed. Similarly, compressed air powers the looms and knitting machines that form fabric from yarn in weaving and knitting operations. In dyeing and finishing, air compressors control the pressure and distribution of dyes and chemicals, ensuring even application and high-quality results.
Given their extensive use, air compressors account for a considerable portion of the energy consumption in textile production. In fact, they are often one of the largest electricity consumers, particularly in large-scale operations. This means that any inefficiencies in the operation of air compressors can lead to significant energy wastage and higher production costs.
The energy challenge: Inefficient air compressors
Despite their importance, air compressors often need to be more efficient. Several factors contribute to energy waste in compressed air systems, including improper sizing, leaks, and inadequate maintenance. Inefficient air compressors may run longer than necessary, consume more energy than required, or operate at suboptimal pressure levels, wasting electricity and resources.
For example, many textile plants operate air compressors at higher pressure levels than necessary, a practice that can increase energy consumption significantly. For every 2 pounds per square inch (PSI) increase in pressure, energy consumption rises by about 1 per cent. Over time, this excess energy use can result in unnecessary financial losses. In addition, leaks in compressed air systems can result in a loss of up to 30 per cent of generated air, further compounding energy inefficiencies.
Moreover, older compressors often lack the energy-saving features found in modern models, such as variable speed drives (VSDs), energy recovery systems, and advanced control systems. These older units may continue to draw high power even when demand for compressed air is low, further increasing operational costs.
Role of efficient air compressors in reducing energy costs
By adopting more efficient air compressors and improving the overall performance of compressed air systems, textile manufacturers can reduce energy consumption, lower operational costs, and improve sustainability. Here are several strategies for achieving energy efficiency with air compressors:
Investing in energy-efficient compressors: One of the most direct ways to reduce energy costs is by upgrading to energy-efficient air compressors. Modern compressors are designed with advanced features that optimise energy use. For instance, compressors with Variable Speed Drives (VSDs) automatically adjust the compressor’s speed based on demand, allowing the unit to operate only when necessary. This prevents the waste associated with running compressors at full capacity when the demand for compressed air fluctuates.
By investing in energy-efficient air compressors, textile manufacturers can achieve energy savings of up to 50 per cent compared to older, less efficient models.
Optimising system design and configuration: Properly designing and configuring compressed air systems can also yield significant energy savings. Many compressed air systems are oversized, generating more compressed air than is necessary for the application. By right-sizing compressors to match the actual demand for air, textile plants can avoid wasting energy on excess production.
Furthermore, optimising the layout of the compressed air system can reduce energy losses due to pressure drops. Compressed air loses pressure as it travels through pipes, especially when the piping is long, convoluted, or contains sharp bends and leaks. Ensuring that the piping system is well-designed, with minimal restrictions and leaks, can help maintain adequate pressure levels without requiring compressors to work harder, saving energy.
Implementing leak detection and repair programs: Leaks are one of the most common and costly sources of energy waste in compressed air systems. In textile plants, leaks can occur at various points in the system, such as fittings, valves, hoses, and connections. While individual leaks may seem minor, they can add up over time, resulting in substantial energy loss.
A proactive leak detection and repair program can help mitigate this problem. By regularly inspecting the compressed air system, identifying leaks, and repairing them promptly, textile manufacturers can prevent air loss and reduce energy waste. Specialised leak detection equipment, such as ultrasonic leak detectors, can locate leaks that may not be audible to the human ear.
Addressing leaks can result in up to 30 per cent of energy savings, making this a cost-effective way to improve efficiency without significant capital investment.
Maintenance and monitoring: Regular maintenance is crucial to ensuring the continued efficiency of air compressors. Poorly maintained compressors are more prone to breakdowns, inefficiencies, and energy waste. Key maintenance tasks include checking and replacing air filters, cleaning intake valves, lubricating moving parts, and monitoring pressure levels.
In addition to routine maintenance, implementing a real-time monitoring system can help track the performance of air compressors and detect potential issues before they escalate. Advanced monitoring systems can provide air pressure, temperature, energy consumption, and compressor performance data. By analysing this data, textile manufacturers can identify trends, optimise system performance, and take corrective actions to prevent energy waste.
Energy recovery: Air compressors generate significant amounts of heat during operation. In traditional systems, this heat is often released into the environment, representing wasted energy. However, modern compressors can be equipped with energy recovery systems that capture and repurpose this waste heat.
For example, the heat generated by air compressors can be used to preheat water for dyeing and washing processes in textile production, reducing the need for additional energy input. Alternatively, recovered heat can be used to heat the facility, reducing heating costs during colder months. Using energy recovery systems, textile plants can reduce overall energy consumption and improve efficiency.
Air compressors play a critical role in textile production, but they also represent a significant source of energy consumption. Textile manufacturers can substantially reduce energy costs by investing in efficient air compressors, optimising system design, implementing leak detection programs, and maintaining equipment properly. These measures help companies save money and contribute to sustainability efforts by reducing carbon emissions and energy waste.
About the author:
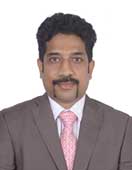
Thomas Paulose is the Vice President and Head – Oil Free Business (India, South Asia, Africa, and the Middle east) of Elgi Equipments.