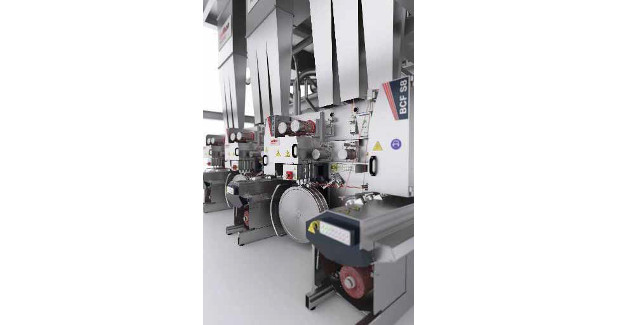
BCF S8 with CPC-T: Colour separation has never been so easy
Until now, it was difficult to produce highly colour-separated or accentuated BCF yarns from polyamide 6, but in the future, this will be possible thanks to the CPC-T.
Until now, it was difficult to produce highly colour-separated or accentuated BCF yarns from polyamide 6, but in the future, this will be possible thanks to the CPC-T.
Oerlikon Neumag promises more flexibility in the colour pattern design of carpets with the latest carpet yarn system BCF S8 at DOMOTEX 2020 in Hanover. All trade fair visitors can convince themselves of the possibilities for product differentiation in Hall 11, Stand A36.
Multi-coloured carpets are becoming increasingly popular and the desire for significantly more flexible colour mixing variants for product differentiation is increasing. Oerlikon Neumag has focused on this and developed the BCF S8, a platform that leaves nothing to be desired when it comes to the colour separation of tricolour yarns – from mélange to strongly separated.
Over 200,000 different shades out of 3 colours
The core component in this process is the new, patent-pending Colour Pop Compacting Unit (CPC-T) for an even more flexible and even colour separation. Individually controllable air pressures per colour in the CPC-T provide a pre-tangling, which results in an accentuation of the colours and thus enables over 200,000 different shades.
Colour Pop Compacting also for PA6 yarns
Until now, it was difficult to produce highly colour-separated or accentuated BCF yarns from polyamide 6, but in the future, this will be possible thanks to the CPC-T. Thanks to the new design, the CPC-T is now also suitable for processes with low thread tensions.
RoTac³ tangle unit with extensive modifications
Significant technological changes to the RoTac³ tangle unit lead to even more efficient BCF yarn tangling. On the one hand, the nozzle has been optimised flow-wise so that the air pressure can be reduced by approximately 10 per cent compared to the previous version with the same knot strength. Furthermore, the nozzle bearing arrangements have been improved. As a result, either higher speeds or nozzle rings with a higher number of holes can be driven, which results in even more knots in the yarn.
The RoTac³ is part of the standard scope of delivery for the newer BCF S8. The tangle unit is optionally available for the single-thread Sytec One plant as well as for the three-thread S+ and can be retrofitted on request.
Oerlikon for PET carpet applications now cover 0.5 to 30 dpf
In addition to the BCF S8 technology described above, Oerlikon Manmade Fibers offers another system concept based on a POY and texturing process. This configuration is designed for a carpet and home textile product range, which is based on a very soft and puffy polyester thread with BCF-like properties due to the small dpf. The target is yarns with a titer up to a maximum of 1,300 dtex and typically over 1,000 filaments. Typical products are, for example, a 1300 dtex f1152 or 660dtex f1152 and 990 dtex f768. The machine concept consists of the well-known WINGS HD POY winder and the new eAFK Big-V texturing machine.
Oerlikon develops modern materials, systems and surface technologies and provides specialised services aimed at securing high-performance products and systems with long lifespan for customers. Supported by its technological core competencies and its strong financial footing, the corporation continues its medium-term growth plan by implementing three strategic factors: focusing on attractive growth markets, ensuring structural growth and expanding through targeted M&A activities. Oerlikon is a globally-leading technology and engineering corporation, operating its business in two segments (Surface Solutions and Manmade Fibers) and employing around 10,500 members of staff at 175 sites in 37 countries worldwide. In 2018, Oerlikon generated sales of CHF 2.6 billion and invested around CHF 120 million in research & development.
With its Oerlikon Barmag, Oerlikon Neumag and Oerlikon Nonwoven brands, Oerlikon Manmade Fibers segment is the world market leader for manmade fiber filament spinning systems, texturing machines, BCF systems, staple fiber systems, solutions for the production of nonwovens and – as a service provider – offers engineering solutions for the entire textile value added chain. As a future oriented company, the research and development at this division of the Oerlikon Group is driven by energy efficiency and sustainable technologies (e-save). With the supply of continuous polycondensation and extrusion systems and their key components, the company caters to the entire process – from the monomer all the way through to the textured yarn. The product portfolio is rounded off by automation and industry 4.0 solutions. The primary markets for the products of Oerlikon Barmag are in Asia, especially in China, India and Turkey, and – for those of Oerlikon Neumag and Oerlikon Nonwoven – in the USA, Asia, Turkey and Europe.
Worldwide, the segment – with just fewer than 3,000 employees – has a presence in 120 countries of production, sales and distribution and service organisations. At the R&D centers in Remscheid, Neumünster (Germany) and Suzhou (China), highly-qualified engineers, technologists and technicians develop innovative and technologically-leading products for tomorrow’s world.