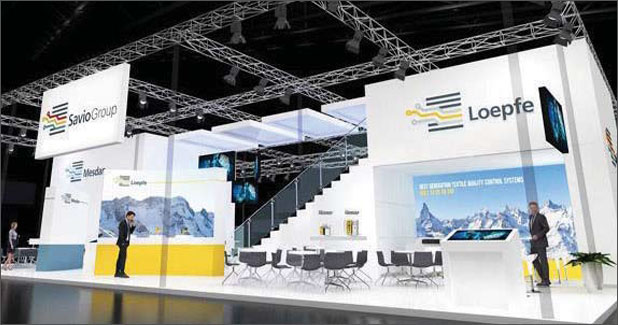
Loepfe’s range of quality control solutions
Various innovative solutions in different areas of yarn quality control will be shown to ensure an interesting visit to the Loepfe booth for all visitors.
Hall: 1 | Booth: C24
Loepfe will present a comprehensive portfolio of quality control solutions for the textile industry at ITMA Asia and will include the well-known YarnMaster ZENIT+ for winding and the WeftMaster FALCON-i for quality control of high-tech materials.
Various innovative solutions in different areas of yarn quality control will be shown to ensure an interesting visit to the Loepfe booth for all visitors. New measuring results of the highly precise YarnMaster ZENIT+ OffColor feature collected in cooperation with a customer will be available. The case study shows impressive results in detection of shade variations in polyester. The Loepfe employees will be pleased to provide more detailed information.
The increasingly popular yarn defect sensor WeftMaster FALCON-i will also be displayed. After the growing demand noticed from North America, Loepfe sees a similar growth in the Asian market for reliable yarn quality control of latest high-tech materials such as carbon fibers, monofilaments, multi-filaments as well as spun yarns in all material compositions. The optical yarn defect sensor removes smallest knots, fluff, filamentation, thick places and capillary breaks before being interwoven into the fabric. The sensor is being used more and more for safety-critical applications such as fabrics for airbags, tire cords, filtration materials, architectural fabrics and sailcloth where quality requirements are very high.
The Laboratory Solutions corner will also provide interesting information. With Swiss precision, Loepfe works systematically on its revolutionary laboratory test instruments. The focus during the ITMA Asia will be on the YARNMAP which provides a tremendous increase in yarn testing efficiency with regard to time, space, maintenance and operator attendance. All kinds of short and long staple yarns are tested fully automatically while, at the same time, preparation products of the spinning mill can be tested on a second measuring sensor.