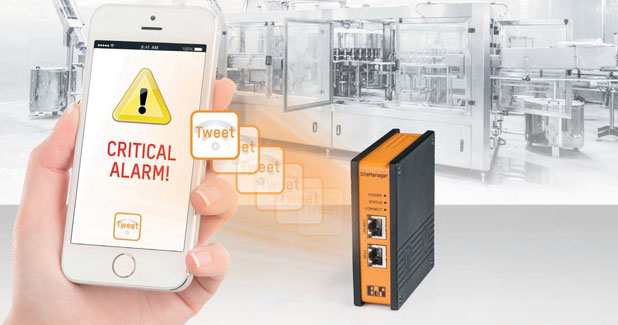
B&R: An ideal partner for textile
With Secure Remote Maintenance (SRM) solution, B&R perfectly balances the needs of IT and production.
With Secure Remote Maintenance (SRM) solution, B&R perfectly balances the needs of IT and production.
Textile industry plays a pivotal role in the Indian economy. Throughout history, the methods of textile production have constantly progressed. Since the last couple of decades, the increase use of automation has resulted in quality improvement, economic improvement and better ways of performing tasks. Use of automation in complex processed, such as cotton picking, ginning, spinning, weaving, dyeing and even in garment making, results in enormous gains in productivity and efficiency. Automated monitoring and controlling process during the manufacturing also minimises waste, costs and environmental impact. This adds the need for factories to get better service and support from machine builders, which further translates to receiving better service from automation vendors. B&R Industrial automation is a trusted name amongst machine builders when it comes to technology, aftersales service and support.
Automation and service
As with any industry, high quality products stand above all, the same goes for the textile industry. Maximum use of automated processes helps customers to be more effective and efficient. However, innumerable benefits are witnessed while implementing automation, one needs to consider maintaining and servicing these machines and factories. Many processes in textile industry are continuous processes, any unplanned stoppages due to machine failures affects productivity and profitability. Today, automation and service both go hand in hand. Service is the differentiator among the selection criteria for machine builders. Automation vendors are also providing improved service through the numerous automation advancements. However, human involvement cannot be ignored and is important for distinguishing between services.
Automation for enhanced service
Textile manufacturing being a continuous process, incudes various machines. Hence, availability of machines becomes increasingly important and any unplanned stoppages impacts productivity and profitability. Most often, the unplanned stoppage is associated with equipment failures or breakdowns and results in loss of raw material, productivity and quality.
Predictive maintenance is the answer to minimising the risks of such unplanned downtime. B&R enables machine builders to integrate predictive maintenance in individual machines and lines. Predictive maintenance can be part of individual machines and is directly integrated in the same control systems. This avoids the installation of a parallel systems and reduces costs. In case the solutions needs to be adopted by an entire factory, then B&Rs factory automation solutions APROL satisfies the requirements of such flexible and modular factories without neglecting the high demands on availability and data consistency. APROL factory automation solutions provide integrated energy and condition monitoring along with process data acquisition in a single system. This system is completely scalable and utilises open platform. Its promises 24/7 monitoring so, machines and devices can be used to the maximum duration of their lifecycle and then be replaced when actually required. In APROL, parameters such as overall equipment effectiveness (OEE) can be viewed at any time and even compared between production lines, shifts or workdays.
With Secure Remote Maintenance (SRM) solution, B&R perfectly balances the needs of IT and production. Diagnosis and maintenance of machines and factories is now easier than ever. The solution utilises the latest IT and security standards and allows for significant savings with low investment costs. SRM enables operators to have seamless secure connectivity right down to sensors and variables. Machine builders or service technicians can access machines from anywhere in the world without interfering with the IT network of the factory. The IT department of the factory configures and provides access rights; post that only authorised personnel can access the network. This offers a perfect mix of accessibility, security and data integrity. This solution helps minimising downtime, reducing service costs, faster diagnostics and maximising OEE of machines and factories.
B&R’s proactive approach for enhanced service
In order to fulfill huge demand of machine uptime, B&R has adopted express support and services activities. With a dedicated hotline number +91 83 80 800 008 and expert support team, B&R helps customers debug and diagnose the faults faster. Dedicated facilities enhances customer support experience and delivers satisfaction efficiently in a shortest possible time. With this approach, B&R is providing best in class service and support to customers enabling them reduce machine downtime. B&R has highly qualified service and support team, which is committed to customer success, and provide necessary expertise to customers to achieve a competitive advantage in their market.
In addition, B&R also has a dedicated support and service portal that provides users with additional functionality. In “material return portalâ€, customers can handle repairs and reclamations quickly and efficiently. Clear tracking of repairs, seamless flow of information between customers and B&R and online availability of all service documents for a service order (repair or reclamation) are just some of the advantages of using this portal. With the “Support portalâ€, customers can easily create support requests and view the status of existing requests. Ensuring transparent monitoring of the support process, providing complete documentation of the information flow between customers and B&R and making necessary files and documents needed for the solution available online are just a few of the benefits of using this portal.
B&R has many years of experience automating textile machines. B&R is already working with leading machine manufacturers globally and in India and owing to innovative products and quality service, they place their trust in B&R. In doing so, they have achieved a technological edge and competitive advantage in their market. With integrated automation solutions for all types of textile machines, and dedicated support and service activities makes B&R an ideal partner for those seeking a complete solution.
“Our products, innovative and technology solutions have made us a preferred automation partner for leading machine builders in textile industry. We launched the “World class support†programme to serve as a single point of contact for our customers nationwide. This dedicated number will further enhance our customers’ experience, in turn enabling them to offer their customers faster service and reduced machine downtime. Our highly qualified support team is committed to our customers’ success and has the expertise it takes to help them gain a competitive edge in their market.â€
– Ravishankar Gawhade, Manager- Support, B&R Industrial Automation
The article is authored by Pooja Patil, Corporate Communication, B&R Industrial Automation.