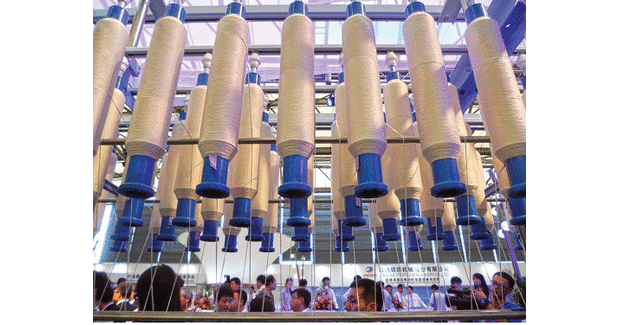
Monforts development for denim finishing continues
Monforts plans to introduce a number of new innovations for denim in the near future, including a solution for the introduction of two-way super stretch into denim in a single processing step.
Monforts plans to introduce a number of new innovations for denim in the near future, including a solution for the introduction of two-way super stretch into denim in a single processing step.
As the number one supplier of finishing ranges to the denim industry globally, the benefits of the latest Monfort Eco Line are already being enjoyed by several of the sector’s leading manufacturers in both Asia and South America.
Denim manufacturing consumes huge amounts of energy and resources at virtually all stages of production, but especially during shrink finishing, and on conventional ranges, large volumes of water, steam, chemicals and thermal energy are required. A significant portion of these resources, however, can be wasted without precise feeding, monitoring and control.
This is an issue that Monforts engineers have successfully addressed with the Eco Line for denim, based on two key technology advances – the Eco Applicator for minimum application of the selected moist finishing chemicals and the ThermoStretch.
As an alternative to conventional padding, especially for wet-in-wet solutions, the Monforts Eco Applicator can significantly reduce the amount of applied humidity required prior to the stretching and skewing of the denim fabric. It also allows mills to apply finishes to just one side of the fabric, or both, and even to apply separate finishes to each side, or to specific areas of a fabric, for endless denim differentiation possibilities.
The Monforts ThermoStretch unit carries out the skewing (weft straightening), stretching and drying in a continuous process. A modified hotflue with reinforced and adjustable rolls for determining the longitudinal tension within the fabric, the ThermoStretch benefits from a structure detector with Pleva SD 1 camera technology employing transmission and reflection lighting for the highest detection capability, in order to carefully measure and control the fabric width and the skewing.
Due to its large number of guide rolls, it is possible to stretch damp fabric in a heated chamber at a longitudinal tension of between 200-300 N with the ThermoStretch, compared to the high forces of up to 4,000 N that have previously been required to finish a typical denim fabric with a starting width of 157cm and a finished width of 151cm.
“Due to these innovations, the Eco Line system reduces energy requirements and losses, increases thermal transfer and keeps the drying energy on the textile material longer,†says Monforts Vice President Sales and Marketing Klaus A Heinrichs. “As a result energy savings of up to 50 per cent are being achieved. We will be introducing a number of new innovations for denim in the near future, including a solution for the introduction of two-way super stretch into denim in a single processing step.â€