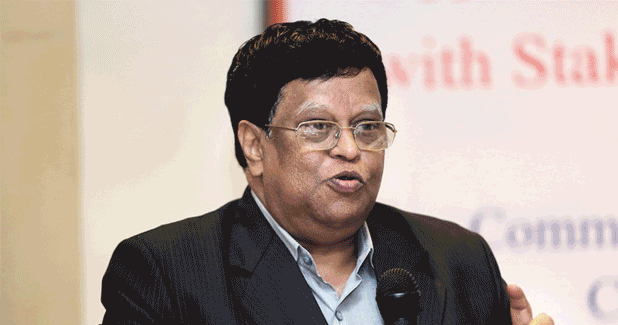
There is huge shortage of skilled labour in textile
The Textile Sector Skill Council (TSC), a non-profit organisation, works towards the development of skilled workforce for the textile industry through setting curriculum for training and accreditation of trade competency.
The Textile Sector Skill Council (TSC), a non-profit organisation, works towards the development of skilled workforce for the textile industry through setting curriculum for training and accreditation of trade competency. TSC is to facilitate scalable “skill training†to the complete work force engaged in the manufacture of textile and hand-loom products. TSC is represented by industry, government and academia to develop innovative skill solutions and to investment in skills and job creation. The key objective of TSC is to define the skill requirement of the industry and to create a deployable talent pool of workforce for the textile industry.
Dr JV Rao, Chief Executive Officer, TSC, speaks on the status of skilled labour in the Indian textile industry, and the segments that are suffering from severe shortage of skilled labour.
Excerpts…
What is the status of skilled labour in the Indian textile industry? Give us some statistics.
There is a huge shortage of skilled labour in Indian textile industry. A big issue which employers are facing today, is absenteeism due to the social system of India. There isn’t an absolute shortage of labour, the problem is absenteeism and churning. India is a country with multiple festivals, hence local workers take leave without notice on and off – making production planning a challenge. The model of migrate residential labour faces the problem of they taking two to three months holiday in a year for reasons like Holi, harvesting, marriages, deaths, Diwali, Chat puja and so on. Further they get benefits under MNREGA for 100 days which makes their stays at home comfortable.
Majority of the workforce in the textile industry is involved in the manufacturing activities. About 85-86 per cent of employment is at worker level for which the required skills can be acquired with a short/modular and focused intervention and thereby enhancing employability of those with minimal education. Such skills can also be obtained in lesser time duration as compared to engineering or ITI courses. Cotton and man-made textiles account for more than 80 per cent of the employment in the textile sector. It is estimated that out of the total number of persons employed in handlooms, handicrafts, and sericulture, about 50 per cent are women. There are more women in the household industry than in the registered small scale or cottage units. However, in the organised sector the percentage of women workers is extremely low, with the exception being in southern part of the country. It is expected that the overall employment in the sector would increase from about 33 to 35 million currently to about 60 to 62 million by 2022. This would translate to an incremental human resource requirement of about 25 million persons. Of this, textile sector has the potential to employ about 17 million persons incrementally till 2022.
Which are the segments in Indian textile industry suffering from severe shortage of skilled labour? Why these segments?
The textile industry (except the spinning sector) is fragmented in nature on account of policy restrictions relating to labour laws and the fiscal advantages enjoyed by the small-scale units. The textile units mostly engage in job work (sub-contracting) and hence a large portion of the employment is in the production activities. Also, the small units do not have explicit demarcation of functions for sourcing, sales, etc. Though all segments suffer severe shortage of skilled labour, spinning, being mostly organized sector is slightly better than the others.
What are the steps taken by the TSC in the last few years? What are the results so far?
TSC, since its inception in August 2014, has striven to create a robust ecosystem for skilling in the textile mill and handloom sector. TSC is governed by 14 Textile Mill Associations and four Export Promotion Councils and has three technical committees to decide various aspects for ensuring quality skilling in the sector. Till date, TSC has developed 88 qualification packs listing the competencies required for 80 per cent of job roles in the textile mill and handloom sector, which are declared as National Standards by National Skill Development Council. Out of these 68 are approved by National Skills Qualification Framework (NSQF).
TSC has facilitated to skilling in the sector in various modes-short term training of fresh candidates and recognition of prior learning under PMKVY and non-PMKVY schemes. TSC is engaged with State Skill Development Missions in Punjab, Haryana, Andhra Pradesh, Tamil Nadu, Maharashtra, Madhya Pradesh, Uttar Pradesh, Uttarakhand, Assam and Jharkhand for skilling of youth in those States.
TSC partners with National backward Class Finance and development Corporation (NBCFDC), NSFKFDC, NSCFDC and is also connected with a wide network of industries and handloom organisations for conducting the trainings. TSC has 14 assessment agencies on board and conducts third-party assessment of skilling under various schemes. Till date, TSC has facilitated certification of over 88,000 candidates, including RPL in textile mills and handloom sector. TSC also facilitates exhibitions, job melas through its stakeholders in various states. Till date, TSC has conducted 56 awareness workshops and has been involved in 11 exhibitions and 11 job melas across the country. TSC has been awarded the “Best SSC†by NBCFDC in the year 2016-17 and “Champion SSC†in the year 2017-18 by the Ministry of Skill Development & Entrepreneurship for steps taken in skilling in the textile mill and handloom sector. TSC is engaged with 11 State Skill Development Missions for facilitating skilling in respective States.
What are the problems faced in skilling the labour for textile industry? What are the prospects and what can be learnt from countries so far successful in this field?
The major challenges faced are skilling costs, increasing wages, policy issues, competition from cheap imports, low demand, rupee appreciation, weak transport infrastructure, tariff and non-tariff barriers, mobilisation of candidates for skilling, high attrition rates due to tough working conditions and low wages in the textile industry. Another problem is absenteeism and migration of skilled labour to other sectors offering slightly better wages or comfort–making skill planning a challenge. Even though many textile industries offer residential facilities to the labour, they take two to three months leave annually for visiting their home town for festivals, harvesting, marriages, deaths, etc. and do not have a fixed duration for returning. Further many get benefits under MNREGA for 100 days at home town and prefer to be there for that duration.
What do you think are the industry’s role in boosting the efforts of the Government?
Many textile Industries have started participating in structured skilling through TSC under various schemes offered by the Government. They are also keen to offer Apprenticeship under National Apprenticeship Promotion Scheme (NAPS). TSC is in the process of developing the curriculum for the same in consultation with the industry. More industries should come forward and connect to TSC to boost the efforts of the Government.
How do you think the recently announced Scheme for Capacity Building Textile Sector (SCBTS) is expected to give a fresh impetus to skilling labour?
The ‘scheme for capacity building in textile sector’, approved by Union Cabinet entailing skill development with an outlay of Rs 1,300 crore, for the period from 2017-18 to 2019-20 will have National Skill Qualification Framework compliant training courses with funding norms as per the common norms notified by the Ministry of Skill Development and Entrepreneurship. The scheme will also promote skilling and skill upgradation in the traditional sectors through respective sectoral divisions/organisations of the Ministry of Textiles; besides providing livelihood to all sections of the society across the country. This will give a major boost and thrust to the industry, as the immediate impact of such a large injection in skilling will be felt all across.
We hope that the execution isn’t cumbersome and time taking, which demotivates the actual employer from using it and then it becomes just a middleman/intermediaries business opportunity. Six sigma skill certifications to ensure quality must be encouraged by the Government to ensure adequate professionals to check and maintain right-first time production.
What are the targets of TSC for skilling labour in the next five years? What are the expectations and investments needed?
The sector is projected to provide employment to at least an additional 20 million people from the current 45 million to 65 million by 2023. TSC targets to establish ecosystem for over 200 job roles to address the skill gap in the textile Mill and Handloom sector. It also aspires to run at least one Centre of Excellence (CoE) for Training of Trainers in each of the four regions of the country. These CoEs may also work as Common facility centres and provide knowledge support to the local industry and handloom Weavers and help the explore new designs and wider markets.
Do the labour policies in India needed be toned up? If so, what are your suggestions for the industry and policy makers?
In ancient times, Indian textiles was famous across the world for its quality and had a major share in the market. However, with time, it has suffered. Textile industry needs a few strategic inputs for reviving its lost glory. For ensuring adequate amount of quality raw material, it is suggested that instead of going for minimum prices through budgetary support, measures should be taken to increase productivity of fibres in the same area using higher yield seeds, technology for crop management and reduced wastage in logistics and storage. Support provided through TUFS to ensure timely disbursements will increase viability fo spindles addition/upgradation in Spinning. In addition, rationalisation of duty structure across all fibres to ensure parity with natural fibres is needed as the consumer demand is shifting towards man-made fibres.
The weaving sector needs support in terms of access to state-of-the-art technology, raw material availability at affordable costs at local level, trained manpower, inputs on fashion and market trends and uninterrupted affordable power to run the industries. While the dyeing industry also needs support with the above mentioned, there is a dire need for handholding for finding ways to reduce production cost, right first time colour matching, maintaining health safety and pollution norms and availability of eco-friendly dyes at reasonable costs. Initiative from the government for establishment of infrastructure for ensuring compliance to environmental standards as the costs for developing the same at individual mill level is too high. The inputs costs including labour, power, transport etc as well as Corporate tax in India is much higher than in some of neighbouring South Asian countries and hence textile production is shifting to these countries. It will be helpful if these points are kept in mind while framing the policies.