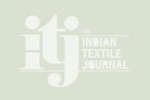
Air audit finds huge energy savings in Lakshmi Mills
In the air audit for Lakshmi Mills, ELGi focused on understanding the usage and efficiency level of its compressed air system. Acompany with over a 100-year-old legacy in the textile market in India, Lakshmi Mills, has two production facilities in Tamil Nadu – in Palladam and Kovilpatti.
In the air audit for Lakshmi Mills, ELGi focused on understanding the usage and efficiency level of its compressed air system.
Acompany with over a 100-year-old legacy in the textile market in India, Lakshmi Mills, has two production facilities in Tamil Nadu – in Palladam and Kovilpatti. The Palladam unit produces 11 tonnes of yarn a day and the Kovilpatti unit produces 12 tonnes of yarn a day.
The plants, which have a total spindle capacity of 133,392, have 18 air compressors with an installed capacity of 500 kW at 2660 cfm. These compressors are being used in the spinning process. The plants operate 8,160 hours a year (340 days x 24 hours) and pays Rs 7 per unit towards power. In all, they consume 382 kWh of power, incurring an annual power bill of Rs 218 lakh.
An air audit helped the company identify opportunities to reduce its energy consumption to 229 kWh at 1054 cfm, equivalent to power savings worth Rs 131 lakh per annum. After implementing the air audit findings, the current power consumption measured at Lakshmi Mills is 153 kWh at 956 cfm, equivalent to Rs 87 lakh per annum.
The need for an air audit
The energy efficiency of air compressor systems tends to reduce over time. To retain optimum efficiency, users need to monitor their performance and power usage, and conduct regular maintenance. Energy can be saved by changing the type of compressors being used, modifying the line design, arresting leaks and optimising usage. Air audits help identify specific problem areas in the air compressor system and provide users a comprehensive report on what they need to do to reduce energy usage.
ELGi has been conducting air audits for not only companies that use ELGi products, but also those using other compressor brands. Since 2011, when ELGi started conducting air audits, it has completed over 250 air audits and proposed savings worth Rs. 62.51 crore. For the textile industry alone, ELGi has conducted around 130 air audits.
The audit team uses flow meters, power analysers, water flow meters, digital pressure gauges, anemometers, infrared thermometers and condition monitoring equipment to evaluate an operation’s air usage. Following the analysis, the team submits a report with a summary of potential savings, along with recommended changes and associated costs. Some common problems the team sees are incorrect compressor size, inadequate air distribution system, incorrect positioning of downstream accessories and air receivers, and poor regulation of pressure.
Savings potential identified
In the air audit for Lakshmi Mills, ELGi focused on understanding the usage and efficiency level of its compressed air system. The audit mapped the plant’s compressed air generation and supply to its actual demand.
Together, these measures could lead to a total of 229 kW per hour of potential savings (40 per cent). It translates to Rs 131 lakh per year in energy savings. The study further detailed ways to optimise the available resources to save energy. It also provided a clear picture on the company’s existing and proposed compressed air system.
Lakhsmi Mills engineers have taken part in complimentary training conducted by ELGi for maintenance engineers. These trainings have helped create awareness on behaviour changes they need to make to conserve energy such as making conscious use of these energy-consuming machines, and how to monitor and identify maintenance requirements such as replacement of old fittings or acquiring new equipment.