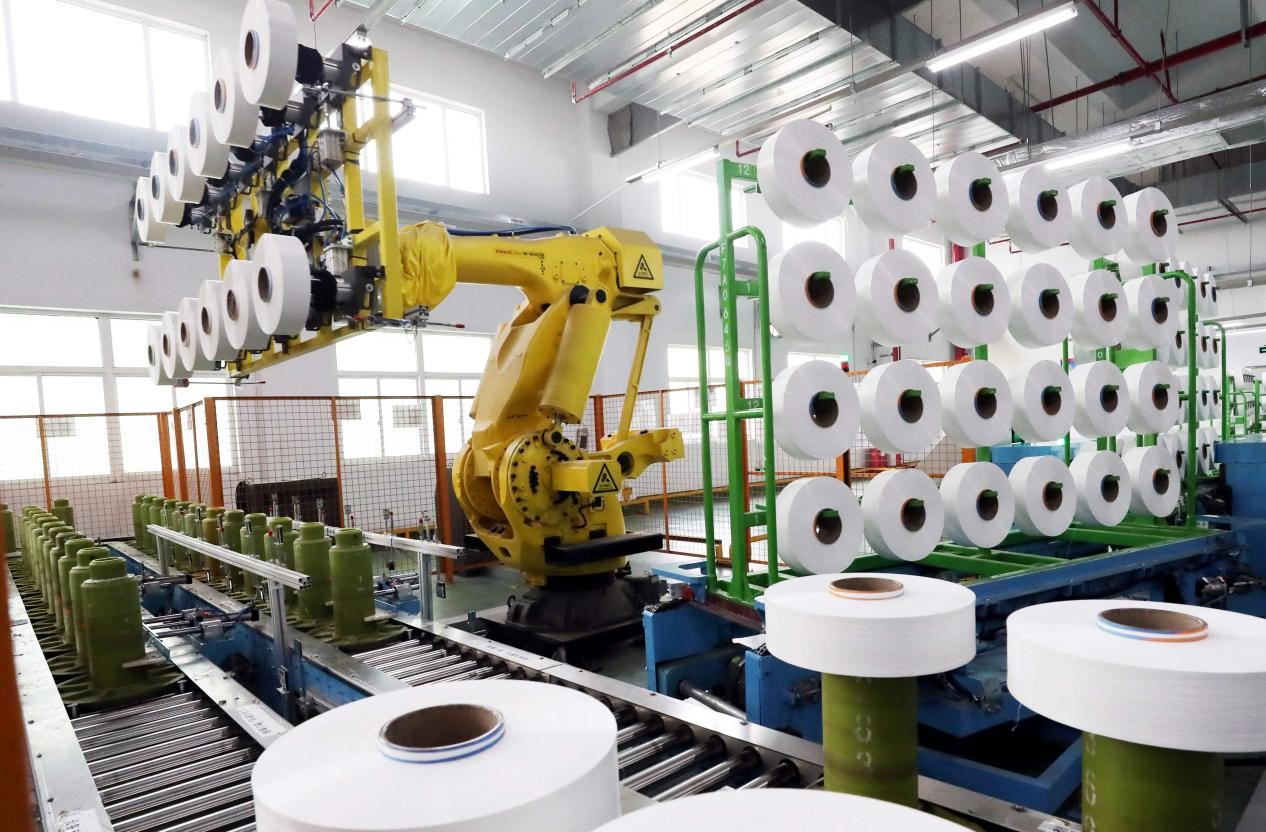
Unlock new business values with automation
The textile industry has been able to multiply productivity by several times due to automation. Further developments are anticipated as time goes on to lower the power requirements of textile technology and increase its speed and effectiveness. And it won’t be long before the textile sector is completely automated. Divya Shetty explores the process of automation in the textile sector and automated processes used by the companies.
The textile industry is increasingly recognised as a global sector. The fact that textiles are ubiquitous has led to their inclusion among the sources of study in the modern world. The textile business employs people from all around the world. There are many various kinds of fibres, yarns, and textiles used to make textile products. In the past, the only technology employed in the textile business was hand-operated and common. The use of technology gradually increased, and in the modern era because of the continuously evolving demands, numerous researchers and businesspeople have begun focusing on various types of cutting-edge modern equipment and technological aspects with the intention of improving product quality and increasing production. The automation or mechanisation of the textile industry is one such topic nowadays.
What is automation?
Through the use of automated machinery and contemporary technology, automation is a unique form of mechanisation that makes it possible to boost factory output quickly and efficiently. Automation is the process of decreasing the labour of workers in various production departments by coordinating their efforts with various machinery through automatic control. As a result, more textile items are produced with less resources and in less time. Hence, automation can be defined as the mechanised or automatic performance of tasks. Automation can now be linked to the production of textile raw materials, including ginning, spinning, weaving and knitting, dyeing, printing, and the garment sector.
Advantages of automation
The following are some advantages of using automated machinery and tools in the textile and apparel industries:
Boost in productivity: Automation raises output by improving the effectiveness of the process. When a labourer completes the task, there is a potential of inaccuracy, reduced productivity because of weariness, and worker breaks. However, using an automated procedure to complete the work reduces these and boosts productivity.
Higher inventory turnover: When industrial productivity rises, so does the industry’s material turnover. The conversion of raw materials, cut components, and semi-finished components into the finished garment takes longer with manual activities. Hence, increased inventory turnover is accomplished by automation.
Quality improvement: As previously indicated, automation reduces the amount of inaccuracy in clothing caused by human participation. This results in goods with fewer faults, higher quality, and lower rates of rejection.
Avoids repetitive work: Progressive bundle system (PBS) of production is used by the majority of garment manufacturers to replace repetitive and monotonous work. In PBS, one employee does a particular task and hands it off to the other. As a result, the labour becomes repetitive and boring for the employee. This may result in exhaustion and decreased effectiveness. Automation, on the other hand, can assist in avoiding these since machines are used to carry out all of these repetitive tasks.
Decline in product and batch variability: As labour is used less, there is a corresponding decrease in the variability of the products generated by various workers. Similar to this, the variability of the same product produced in several batches (during various periods of time or in other businesses) is similarly decreased.
Beyond human capacity: Some professions that need highly skilled labour can be performed by automation. As electrical devices and other gadgets become more integrated into modern clothing, significant skill is frequently required to carry out these activities. Automation makes it much simpler to accomplish these goals.
Reduction of direct labour costs and overheads: Automation contributes to higher production and efficiency while lowering direct labour expenses and overheads. Moreover, automation facilitates the work of several operators. Also, there is less need for personnel to receive training for each new style and other quality-related training. As a result, labour overheads and their associated costs are decreased.
Automation process in textile industry
There are several areas of automation in the production of garments including the yarn and fabric manufacturing process. Here are the applications of automation in the textile production.
Fabric inspection: Traditionally, fabric inspections were carried out manually, making it frequently impossible to precisely identify problems. The fabric inspection procedure is made more effective with the usage of automated technology. One of the most challenging textile processes to automate is fabric examination. For automatic fabric inspection, a variety of techniques, including the statistical approach, spectral approach, and model-based approach, can be used. In each of these techniques, the fabric image is modified by a modelling tool or piece of software to obtain details about the degree of the fabric problem. The found flaws are automatically noted on the fabric, and if there are too many of them in one fabric lot, it is discarded.
CAM and AutoCAD: The design of fabric used to be done by hand in the past. In order to spend a lot of time and capture the design on paper. But nowadays, computer-aided design (CAD) and computer-aided manufacturing (CAM) are used by clothing producers to create their products. Computer programmes called CAD are used to develop 3D designs for garments, and CAD then delivers those designs to CAM. Based on that data, CAM oversees and controls the production process.
Fabric spreading: Earlier, spreading fabric was a manual process that required employees to spread the fabric by hand. Moreover, more than one worker was needed to finish the task. Next came the semi-automatic device, where one may use the device to accomplish the task. At the moment, completely automatic devices can be used to spread cloth. When spreading fabric automatically,
- By maintaining the length-width in accordance with the operator’s directions, the work is completed swiftly.
- Automatically spliced and begins spreading new fabric where the previous roll has ended.
- An efficient and high-quality sensor is employed to detect faults, and the flawed fabric is automatically cut.
- Counting the ply number, and when the designated ply number is reached, the machine automatically shuts off.
- This machine can spread any kind of fabric.
- Less labour is needed, which takes less time.
- Unfortunately, operating this equipment requires a professional operator and is highly expensive.
Fabric cutting
Earlier, this technique was also carried out manually, but it is currently done using an automatic cloth cutter. The fabric can now be cut more precisely and smoothly than before as a result. According to the pattern’s design for the garment, it is now saved directly in the computer’s memory without being printed out, and using that information, the cutting machine will automatically and properly cut numerous layers of fabric together. Elsewhere else, a laser is likewise used to cut things. When compared to manually or operator operated devices, the usage of automatic cutting machines has lowered both the number of people and the amount of time.
Sewing
The majority of the garment manufacturing process, particularly the sewing process, is still carried out by skilled employees in nations like Vietnam, Vietnam, Cambodia, and Laos. Sewing Robot or automatic sewing machine purchases by manufacturers have not advanced significantly, which has helped maintain their investment cheap. But, manufacturers who haven’t made the investment in cutting-edge machinery face fierce rivalry to keep labour costs down. Industrial robots that can handle fabric during sewing activities are currently being constructed in order to automate the sewing process and eliminate the need for human labour. These automatic machines make seams in a manner akin to that of conventional sewing machines. The formation of several sewing stitches, including the overlock stitch, double chain stitch, double lock stitch, etc.
Sewing robot
The Sewbo is an industrial robot used in the clothing industry for manipulating and grasping fabric. There have been several test runs employing robots to sew the entire garment. Sewbo, a robot created by Zornow that can automatically handle fabric components during sewing, is one such example. Zornow created the “Sewbo” robot in 2015, which can sew a T-shirt from beginning to end. This accomplishment represented a significant step towards obtaining complete outfit automation at 100%. It is possible to programme the robot for a particular size and look. The robot must be reprogrammed if the size or kind of clothing changes.
LOWRY SewBot is a unique kind of robot created specifically for the apparel business, and it was created by American company “Softwear Automation” with its headquarters in Atlanta. These SewBots were created using cutting-edge industrial 4.0 revolution technologies, such as advanced robotics or computer vision, which can analyse and work with cloth much like a human. SewBots can complete a variety of garment production operations, including fabric cutting, sewing, waking, labelling, and inspection, all under the control of a single touch panel.
Innovations in automation
The entire textile value chain (associations, businesses and universities) have rapidly adapted automated practise and here are a few example of how they are utilising it.
At the Cotton Corporation of India (CCI), manual systems are minimised by CCI in the procurement of cotton. Equipment like digital moisture metres and micronnaire testers are available at all its’ procurement centres to ensure that farmers get right price for their produce, based on scientific assessment of quality at the spot.
To move ahead on the path of digitalisation, CCI is also in the process of implementing QR code using Block Chain Technology from processing of cotton and warehousing till its e-auction sale to the buyers. This will create a benchmark to the textile industry and will be a milestone for development of brand image of Indian cotton.
Dollar industries has introduced the Integrating Auto Replenishment System (ARS) and Distributor Management Systems for Lakshya distributors. It is currently working to implement ARS at the supply chain level. An after-sales service app is being developed at the retail level and activity tracker for the sales team. The business operations are in the process of transitioning from Oracle ERP to SAP. The company is also integrating automated tele-calling for our tele-callers for enhanced customer management.
With these transitions, Dollar Industries is aiming to achieve transparent engagements with retailers, gain deeper insights about on-ground realities that will doubtless lead to increased productivity and efficiencies.
Indo Count has improvised its lighting system across the manufacturing units from conventional lighting to LED based lighting system, we have upgraded our Compressors/pumps/motors to reduce energy consumption, optimising fuel to steam ratios, optimised usage of resources etc. All these contributed to significant reduction in Scope 1 & Scope 2 emission.
Khosla Profil’s majority of the RFID stock is now completely having RFID kits. They use them before taking them off, dispatching them, and then using them again. A lot of work which was formerly done manually, has been digitalised.
Use of block chain and traceability can also help to combat the issue of green washing in the textile industry. Many brands claim to be sustainable or ethical, but often lack the necessary evidence to back up these claims e.g. recent cases of H&M and SHEIN among other brands. By implementing a block chain based traceability system, it would be possible to verify the sustainability and ethical practices of each supplier and manufacturer, ensuring that claims made by brands are backed up by reliable and accurate data.
Digitalisation opens up options for transparently presenting the origin, ingredients and production routes i.e. the entire journey of a product. It will change the perception and the process of the entire industry. It is not only desired for sustainability, it is also desired for the control of costs and margins within the global supply chain that is driving the turn to resource efficiency and therefore sustainability as well. Digitalisation is now one of the most powerful tools for influencing the market.
PDS is doing some interesting changes in the digital side, especially with product development and sampling. They are using a 3D design. The 3D design has a number of benefits- the company can reduce the number of samples that are produced, and can change the sample straight away. Whether it’s colour, the drape, the fit, or even embroidery and fabric- manufacturers can see real-time what fits best! This approach reduces lead times, prevents overstocking and over-inventory- not to mention quick decision-making.
SIMA has been imparting various skill development programs of both Centre as well as State Governments for the benefit of textile industry. SIMA was one of the implementing agencies for undertaking training under Pradhan Mantri Kaushal Vikas Yojana (2016-2020) to train trainees for Southern States namely Tamil Nadu, Andhra Pradesh, Telangana & Kerala during April 2019. So far 1300 candidates have been successfully enrolled in the PMKVY (2016-2020) and the mills have directly derived benefit out of the same.
The Association was selected as one of the implementing agency by Tamil Nadu Skill Development Corporation to give certification for experienced workers in Textile Sector under TNSDC RPL programme. In first phase we have completed RPL program for around 5000 workers.
The Mahlo Qualiscan QMS-12 is a modular system for the measurement, logging, and control of critical process parameters over the entire width and length of a running web.
The QMS-12 can be used virtually in every area of industry in which products are produced or finished (including coated products) as a web. The versatile sensors and measuring devices of the QMS-12 can sense, log, and continuously control (in-process) parameters as weight per m2, coating weight, moisture, or thickness of web-type products.
Automation: The next big thing
Automation and robotics are now widely used in the textile sector. The textile industry is already seeing significant robotics breakthroughs. Yet, the sectors that produce textiles do not use mass production. There are often fewer studies on robots and automation in textile manufacturing. Because of this, the applications of robots in the textile industry have not significantly deviated from standard handling, assembly, welding, cutting, and so forth. In order to further investigate the use of robotics in the textile business, our textile manufacturer must invest and take the appropriate steps.
We now understand that robotics and automation are essential for boosting production and prosperity in the textile and clothing sector, as was covered above. The sooner robotics and automation are introduced into the textile and garment industries, the more benefits there will be. Thus, the textile and garment industries cannot compare to robotics and automation in order to remain in the current cutthroat market.
Inspiring from various efforts of Government of India, the textiles industry is now seriously investing in latest technology and adopting solutions for digitisation, IoT integration, AI, and ERP and simplifying the entire fabrication process, from farm to fashion. The above collaborative efforts of all stakeholders will really be helpful in improving India’s position as a low cost, quality supplier and India will become a great leader in coming years.