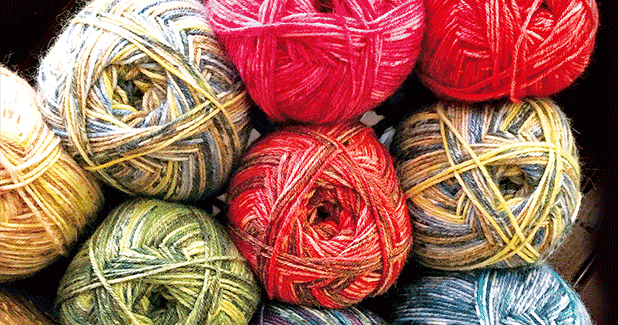
New-age yarns blend with changing needs
The cup of cappuccino on a winter’s day, NILIT Heat nylon yarn from Nilit, made with coffee charcoal, warms wearers from the inside out. Wearers enjoy a comfortable sweat-free sensation due to the excellent absorption and moisture management provided by the yarns.
A spate of space-age yarns is ushering in a new era of added values to the Indian yarn market. Some trend-setting innovations are explored.
Like a cup of cappuccino on a winter’s day, NILIT Heat nylon yarn from Nilit, made with coffee charcoal, warms wearers from the inside out. Wearers enjoy a comfortable sweat-free sensation due to the excellent absorption and moisture management provided by the yarns. Similarly, there are yarns that can give fabrics a high control on humidity, odour resistance and permanent protection against UV rays. Speciality yarns [like these], which are a great way to add another creative dimension to any knitting project, are flooding the Indian markets. These yarns are known to be stylish and more decorative than most other types and are made to be combined with other yarns to create a beautiful and unique design that is all your own.
Avinash Mayekar, MD & CEO of Suvin Advisors, thinks that India has already positioned strongly in international market in terms of conventional yarns, but now time has come to understand the importance of value addition in textile yarns. He added, “Umpteen numbers of different yarns are developed in international market depending upon the properties, end-uses, different finishes, different textures and different looks.†He added, “Global trend will be shifting from occasion specific clothing to function based clothing where fabric properties will be playing major role. Some of the trends like temperature controlled and IT-embedded technical garments will be gaining more importance in coming future. Increasing awareness on climatic changes, global warming, eco-friendly concept and enormous industrial growth will be leading to more focus on functional clothing than need specific clothing.â€
The best yarn quality from Rieter
Com4® yarns—from Switzerland-based Rieter—are yarns that fulfill the most exacting requirements and ensure competitiveness in a dynamic market. Thanks to mature technologies, yarn production in Rieter ring, compact, rotor and airjet spinning processes demonstrates a high level of efficiency and achieves excellent yarn quality. Rieter customers profit from optimised production costs and good selling outlets. The benefits of the Com4® yarns are also visible in downstream processing and in the final product, e.g. from high processing speeds, less fibre fly and low size pick-up through to excellent pilling values, low spirality tendency and high-wearing comfort.
Each Com4® yarn has its own properties – not in comparison to other yarns but rather for what the respective Com4® yarn stand. The comparison of the properties is decisive in the selection of the most suitable Com4® yarn for the respective textile application.
In yarn manufacture, compromises must often be made between quality and costs and this can lead to the benefits offered by a spinning technology not being fully exploited. Thus, a smaller rotor is used to achieve higher productivity, which conversely leads to lower yarn volume.
Many properties are strongly dependent on the yarn count and the raw material used. The tables show the main characteristics of each yarn that can be found in practice. Com4®ring is characterised by high flexibility in the use of the raw material, the yarn count and the yarn character. It possesses a high degree of strength and high and even yarn hairiness.
Com4®compact is also distinguished by extremely high strength, even yarn structure, low hairiness and high yarn density. Com4® jet has a unique yarn structure with very low, short hairiness. Com4® jet yarn is a voluminous yarn which positively influences the opacity of the yarn in the fabric. Due to its special fibre bonding, it also has a high level of resistance to abrasion.
Recron rules the polyester market
Even India’s biggest business conglomerate is not far behind in speciality yarn market. Reliance Industries’ Recron is capturing the high-polyester textured yarn market. This was clearly visible during the recently-concluded Yarns and Fibres expo in Mumbai.
While speaking to a senior official from Reliance during the expo who wished to stay anonymous, said, “Recron is India’s leading manufacturer of high-quality polyester textured yarn. Consistently pushing the boundaries of comfort and luxury, yarns help create some of the finest fabrics that define fashion around the world. With Recron PTY, you get the very best in apparel and non-apparel yarns.â€
Products offered under Recron are: Recron partially oriented yarn (POY), Recron polyester textured yarn (PTY), Recron fully drawn yarn (FDY) and Recron industrial yarns (IDY). Reliance is a major exporter of textured yarns from India and has presence in over 35 countries across Europe, Americas, Africa and the Middle-East. The export customer portfolio consists of some of the very discerning and quality conscious buyers in the world. Recron Textured Yarns are available across the globe through our vast network of offices, delivery centres and agents.
“Recron Certified is a consumer initiative from the Polyester business of Reliance Industries Ltd. It was launched in the year 2002, in response to the Indian consumer’s crying need for good quality, standardised sleep products at affordable prices. As such, Recron Certified Pillows were the first ever ‘Certified’ products in the history of Sleep & Home Comfort Products in India,†said the spokesperson from Reliance.
Linen: The yarn for Indian conditions
The various advantages associated with linen fabrics such as smoothness, coolness, lint-free, softer over longer duration, are driving the global linen fabric market. European flax fibres and Chinese linen yarns are flooding the Indian market, thanks to a spurt in consumers’ interest in linen products. Linen is the coolest fabric material in the world, the market of which is warming up day by day in India, thanks to a spurt in promotion mounted by the big names including Grasim, Raymond and many more small players. There has been a three-fold increase in the consumption of linen in India in the last five years, and the linen market has opened up opportunities for new applications like no other fibre has in the recent times. Linen is obtained from flax, a bast fibre taken from the stalk of the plant. The lustre is from the natural wax content. Colour of linen is creamy white to light tan.
Alex Vanneste, President of Belgium-based N.V. Jos Vanneste S.A, said: “Linen market is doing great in India. In fact, I would say it is growing at a good rate. A lot of new spinners are coming up. Pure linen spinning has been introduced as a economical investment in the future. Reasons could be because consumption is there, and you have competitiveness as compared to China because of labour costs. Mainly because of the availability of workers, which is not there in China.â€
N.V. Jos Vanneste S.A. is located in Kortrijk, the world centre of the flax industry. The family business is currently run by the fourth generation of Vannestes: Alex who also intend to be linen experts. The company’s worldwide renowned flax fibres, pure linen yarns and linen tops used for blending with other fibres are the results of its optimism, dynamism and know-how.
Added Alex: “There are various blends coming in India. The reason flax market not booming in India is not only because of the cost factor. For me, the reason is that on one side there is pure linen getting appreciation but on the other side not everybody can spun linen. Cotton spinners can introduce linen as an effect. Blending together you can start playing with two advantages. It is not only linen which is interesting, but a combination of both can be exciting. For e.g: pure linen in knitting is almost impossible. But if you put in the blends, you can make fantastic things. Today, they use it as an effect, but tomorrow they can use it as an advantage, which are very nice to wear on the skin.â€
Speaking on the future on linen in India, he said, “I believe a lot in India. As far as blends and pure linen is concerned, India is one of the countries for the future. It is an ecological fibre. It comes with the blessing of god. We don’t need extra water, we don’t need fertilisers. We grow it in a very sustainable way. We grow it in a area where food production is oversized and further Creating new possibilities for European agriculture. It is not harmful for anybody.â€
The cotton touch
As the Chinese cotton auction started at a 25 per cent premium over the prevailing fibre rate in India, Indian exporters are pinning hopes on a revival in cotton yarn exports. Despite a robust demand from Bangladesh, cotton yarn exports remained under pressure during the current financial year due to sluggish demand from China. For the April-December 2016, India’s cotton yarn exports slumped by 12 per cent to 872 million kg from 987 million kg in the corresponding period last year. Cotton yarn exports from India rose by a marginal 4.29 per cent at 1,307 million kg for FY2015-16 from 1,253 million kg for the previous year.
With 50 million spindles and 0.75 million open-end rotors, India has world’s second largest spinning capacity, commanding a share of the global cotton yarn market – currently producing over 4,700 million kg of spun yarn of which over 3,400 million kg is cotton yarn. Cotton yarn accounts for nearly 73 per cent of total spun yarn production. Indian spinning industry is the most modern and efficient in the world. India produces a wide range of yarns for every conveyable end use – non-spun or open-end; combed or carded, basic, compact, melange or fancy. India’s spinning mills produce them all for requirements ranging from a fine 200 count to a coarse 2 count.
The world’s most renowned Indian cotton yarns are available as greige, bleached, mercerised, gassed, twisted, dyed or an endless range of fashion yarns like melange, stretch, blends and so on to meet the different applications in fashion, clothing, home textiles, hosiery and industrial fabrics.
Today, Indian yarn is widely accepted in International markets as the exporters regularly meet the needs of importers with unmatched efficiency in countries like the US, Italy, Spain, Japan, China, South Korea, Taiwan, Bangladesh, Vietnam, etc.
RS Baalagurunathan, Managing Director of Tirupur-based Anandi Enterprises, a supplier of yarns and fabrics, said, “We produce and supply 100 per cent cotton yarns and its blends from the count range of Ne 10’s to 140’s both in single and double, gassed mercerised, recycled yarns ready to cut finished fabrics for both knitted and woven with BCI, GOTS and OE, GRS 2.1 certified. We offer woven bed linens, table clothes and terry towels. We are working from the very beginning with BCI cotton as well.â€
He added, “We are direct implementing partner for BCI Cotton at Orangal, Telangana with 3,500 farmers. We are running authentic organic cotton project in Salem, Tamil Nadu with 3,000 farmers certified by control union.†Baalagurunathan said, “The special products which we are producing are recycled cotton, recycled cotton with recycled poly, BCI cotton, authentic organic cotton, fair trade organic and e-mélange. We deal with retail brand buyers like Levis, M&S, C&A, H&M, Diesel, etc. We are doing 100 per cent organic cotton with herbal dyed fabric.†Another innovation in cotton yarn is Newlife-Cotton Touch. Newlife – Antibacterial range is made with antibacterial yarns with anti-smell functions, manufactured by adding an antibacterial agent during the melting. The product range combines Newlife technical properties with the natural fibres appearance. This combination is particularly suitable for a wide range of products, from sportswear to workwear.
The special composition of the yarn, due to the modified filaments section, allows the moisture to pass from the inside to the outside of the fabric, keeping the body dry. During tough physical activities, garments made with Newlife-Cotton Touch yarns guarantee high levels of comfort.
Thanks to Decora technology, it is possible to add poly-functional properties to the Newlife-Cotton Touch yarns, such as antibacterial, which makes them even more suitable for medical fabrics. With this treatment, apart from preventing bacterial growth and making it sterile, Newlife-Cotton Touch yarns, which are continuous yarns, are not subject to short fibril loss, as generally occurs with natural fibres and which is usually one of the main causes of virus spreading in hospitals.
Birlas rule the viscose segment
VFY is a natural yarn made from wood/cotton pulp. It is obtained from nature and so is a natural product (not synthetic). Raysil, the VFY manufactured by Indian Rayon, an Aditya Birla Nuvo unit, comes in a wide array of colours, including natural whites. Raysil is available in more than 600 shades, ranging from the purest tints and medium tones to vibrant deep shades. The yarn is available in fine to coarse deniers ranging from 75 to 1200. Raysil is 100-per cent biodegradable and eco-friendly.
Aditya Birla Nuvo (ABNL) with a diverse portfolio ranging from manufacturing to the service sector. It is a leading player in segments as varied as VFY, caustic soda, carbon black, fashion and lifestyle (branded apparel and accessories), agri business, textiles and insulators.
Indian Rayon, the VFY unit of ABNL, is a major player in the Indian VFY segment. The unit is the second-largest producer of VFY in India. With a capacity of 17,520 tpa, Indian Rayon is the first in India to adopt the most advanced VFY technology with 88 pot spinning machines (PSY) and 17 continuous spinning machines on parallel yarn. It also accounts for 50 per cent of India’s VFY exports, making it the country’s largest exporter of the product.
Spandex stretches to the Indian market
Spandex, lycra or elastane is a synthetic fibre known for its exceptional elasticity. It is stronger and more durable than natural rubber. Spandex fibres are produced in four different ways: melt extrusion, reaction spinning, solution dry spinning, and solution wet spinning. All of these methods include the initial step of reacting monomers to produce a prepolymer. Once the prepolymer is formed, it is reacted further in various ways and drawn out to make the fibres.
Because of its elasticity and strength (stretching up to five times its length), spandex has been incorporated into a wide range of garments, especially in skin-tight garments. A benefit of spandex is its significant strength and elasticity and its ability to return to the original shape after stretching and faster drying than ordinary fabrics.
INVIYA is a new age spandex elastane fibre made of advance polymer having long lasting elasticity with robust performance during textile processes. With exceptional qualities of stretch and recovery, it provides perfect fit with enhanced comfort and freedom of movement. INVIYA fibre can stretch up to six times of its original length with excellent recovery providing long lasting fit and shape to the garment.
INVIYA I–300 is a new series specifically developed for wide applications due to its high tenacity and better frictional properties, enabling it to run at high speed in core spinning, draw texturing and circular knitting. High-heat resistance properties of INVIYA I–300 retain its high stretch power even after re-dyeing and repeated washes. It’s developed for denims, ready-to-wear, active-wear, shape-wear and intimate-wear for high performance and durability. INVIYA I–300 in bare or covered form can be combined with various textiles raw materials like cotton, polyamide, polyester, viscose, linen, silk, cashmere and wool.
It retains its power well during fabric processing like heat-set, dyeing, finishing, etc. under controlled conditions. This makes INVIYA I–300 a revolutionary fibre, which enhances fabric performance with higher stretch, low growth, and great dimensional stability.
New breed of high-performance wool
Wool is a fibre that forms the protective covering, or fleece, of certain animals. It is most often associated with sheep, but other hairy mammals, such as goats and camels, also produce wool. Wool protects people from both heat and cold. The woollen industry in India is small in size and widely scattered. It is basically located in Punjab, Haryana, Rajasthan, UP, Maharashtra and Gujarat. Around 40 per cent, of the woollen units are located in Punjab, 27 per cent in Haryana, 10 per cent in Rajasthan, while the rest of the States account for the remaining 23 per cent of the units. A few of the larger units are located in Maharashtra, Punjab, UP, Gujarat and West Bengal.
Since indigenous production of fine quality wool required by the organised mill and the decentralised hosiery sector is very limited, India depends upon imports. Imports have been mainly from Australia and New Zealand, the major supplier is Australia. New Zealand wool is being imported mainly for Carpet sector for blending it with indigenous wool.
The Woolmark Company is the global authority on Merino wool and owns Woolmark logo. Australian Merino wool is an entirely natural fibre grown year-round. Grazing on extensive grassland terrain, Merino sheep in Australia are free-range animals that live a largely carefree existence. From the high rainfall areas of the eastern seaboard to the drier pastoral areas of the west, Merino sheep have become an integral part of the iconic Australian landscape.
A wool fibre is composed of a natural protein called keratin that is biodegradable, similar to protein found in human hair. When disposed of, Merino wool decomposes in soil in a matter of years, slowly releasing valuable nitrogen-based nutrients back into the earth, acting like a fertiliser. In contrast, synthetic fibres can be extremely slow to degrade.
– KARTHIK MUTHUVEERAN