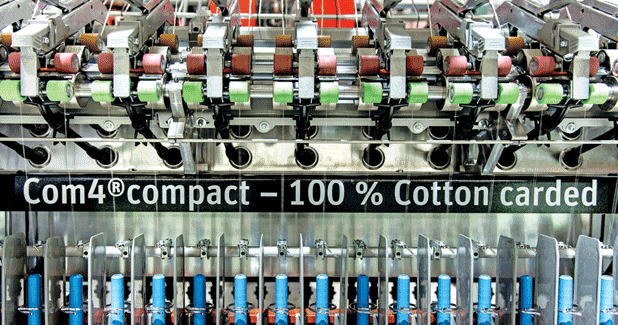
The new Q-Package for best yarn quality
The production of best yarn quality at lowest manufacturing costs is the constant challenge of every spinner. With the Q-Package, Rieter developed a solution that allows all ring and compact spinners to either improve the yarn quality or simplify the choice of fibres.
Rieter’s G 36 and K 46 are now available with up to 1,824 spindles and are always equipped with the suction system ECOrized for lowest energy consumption, says Vijaykumar More.
The production of best yarn quality at lowest manufacturing costs is the constant challenge of every spinner. With the Q-Package, Rieter developed a solution that allows all ring and compact spinners to either improve the yarn quality or simplify the choice of fibres. The yarn quality can thereby be improved in certain parameters by up to 30 per cent.
Rieter’s ring and compact spinning machines with their unique spinning geometry are known as standards for productivity at lowest yarn manufacturing costs. The latest models G 36 and K 46 are now available with up to 1,824 spindles and are always equipped with the suction system ECOrized for lowest energy consumption. The latest components in the drafting system called Q-Package were presented for the first time at the ITMA 2015 in Milan for both machines (Fig. 1).
Consistent quality has always set standards
The Ri-Q-Draft drafting system, tried and tested a million times, with the low-wear suction drum including the air guide element “Detect†for the compact spinning machine and the “Best-in-Class†components from Bracker and Novibra, allow highest productivity without compromising the quality. Here, the long-term consistency of Rieter machines is worth special mention. Ri-Q-Draft has always been a key to achieving the best running properties.
Superior yarn characteristics
The Q-Package is the combination of a newly developed nose bar with the ACP cradle (Fig. 2) instead of the familiar Ri-Q-Bridge and the standard cradle. This allows adjusted fibre guidance and can in many cases be optimised by insertion of a drop-shaped pin. This version is integrated in the latest machine configuration and alongside the standard system, which is still available, can be selected at the customer’s request. Here, the unique spinning geometry and all other proven components remain unchanged.
Both machines, G 36 and K 46, that were equipped in the field with the Q-Package (Fig. 3), showed a reduction of imperfections as well as Classimat faults of up to 30 per cent without influencing the yarn tenacity or the hairiness in the process (Fig. 4). Additionally, clear advantages with the K 46 in downstream processing through fewer warp thread breaks could be evidenced.
More advantages at high short fibre ratio
The advantages with the yarn characteristics are clearly far more distinctive with a raw material that has a high short fibre ratio, as due to the pin the short fibres are significantly better guided than previously. Thus the choice of fibre is simplified. A raw material with a slightly higher short fibre content can achieve comparable yarn values. Also yarns of count Ne 30 and finer showed a reduction of at least 10 per cent with the imperfections and Classimat faults. In the best case, quality improvements of 20 to 30 per cent are possible. The Q-Package offers a wide field of possibilities to select the settings according to the requirements of the yarn buyer.
The best solutions on one machine
Alongside the economical production of best quality yarns, the G 36 and K 46 machines impress with their simple operation. The greatest possible number of settings can be adjusted and controlled direct on the machine panel.
The following functions make the machines unique in their application:
- draft change in a matter of seconds with FLEXIdraft
- cop change without underwinding with SERVOgrip
- reliable doffing with ROBOdoff
- partial spinning startup of the machine with FLEXIstart
- electrically-driven cop transport SERVOdisc.
The production of specialities such as twin yarns and fancy or core yarn is also easily possible on both machines. The advantages are completed by the extraordinary technical competence drawn from over two hundred years, which allowed Rieter to become the innovation leader. That is an obligation for new and further developments, where the added value for the customers is always at the forefront.
The article is authored by Vijaykumar More, who is Product Manager Ring / Compact Spinning at Rieter. He can be contacted at:vijaykumar.more@rieter.com