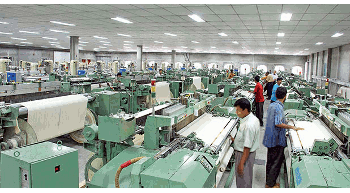
Energy savings in textile mills
Textile mills have been operating the waste recovery system (WRS) to suck the waste from the cards, combers and blow room after matching the collective specs of waste suction flow and Pascal pressure requirements to the WRS. After a few years, the parameters are altered due to change of equipment, variations in cotton, changing quality needs suiting to market. Here, we have to keep the energy saving option always open, routinely during the above. Though the WRS OEM has given the Pascal gauge at the filter box, and at the individual cards, the mill has to maintain the optimum Pascal suction at each of the card.
Why textile mills see instant energy savings in their WRS now, explains Ashok S.
Textile mills have been operating the waste recovery system (WRS) to suck the waste from the cards, combers and blow room after matching the collective specs of waste suction flow and Pascal pressure requirements to the WRS. After a few years, the parameters are altered due to change of equipment, variations in cotton, changing quality needs suiting to market. Here, we have to keep the energy saving option always open, routinely during the above. Though the WRS OEM has given the Pascal gauge at the filter box, and at the individual cards, the mill has to maintain the optimum Pascal suction at each of the card. Since the same is not condition monitored routinely, the mill is losing heavily in WRS and now each mill is finding this proposal as a low hanging fruit in ECON measure.
Where is the daily energy loss happening in WRS?
The daily energy loss is in practically measured in terms of Pascal pressure variations at each point namely the fan end, across the primary and secondary filters, starting point of the main header, end of the main header, branch duct before and after the duct shutter near the card. Any Pascal drop in each area and comparing the same with the base data during commissioning in the above inspection points will indicate the overall energy loss and relative loss in each machine. Savings in Pascal drop leads to KW savings in blower power consumption.
How this can be monitored to reduce in cards?
The individual card Pascal reading will indicate us whether the carding machine sucks or the leakage from the air inside the machine is sucked more. Relative readings routinely measured, will indicate us the leakage + consumption in each card.
Today, purchase a Digital Pascal meter costing around Rs 6,000 only. Use of U tube manometer is prone to measurement and reading errors. For each card, put your meter above the shutter near the card, and first take the Pascal reading. Now close the shutter and check how much the Pascal raises.
You repeat this exercise say in four cards of the same branch header. Comparing Pascal raise in each card and whichever card shows higher Pascal relatively (compared to other cards) shows more leakage + consumption inside that machine thro its duct gaps, leak thro hoses, fittings, seal leak in inspection covers, etc.
Repeat the same exercise by putting the Pascal meter at the start of the branch header catering to say four cards. By closing each card shutter what is Pascal raise noticed relatively (compared to other cards)?
This will confirm the leakage + consumption in card and the leakage up to the point of measurement in the branch off point of sub header. Repeat the same exercise when you are opening the each card shutter, what is the Pascal drop relatively (compared to other cards) measured in each card? Now put the Pascal meter at the start of the main header in the carding area. Let us say we have two branch ducts catering to eight cards say four cards in each branch.
Repeat the above exercise by closing a set of cards in one branch and higher the Pascal raise seen in the other branch indicates the more leakage + consumption in that branch. Repeat this exercise when re-opening the duct & the cards catered to; to see relative Pascal drop between the two ducts.
How this can be monitored to reduce in WRS?
Check with WRS OEM what the maximum/minimum/optimum Pascal drop is across the primary filter, secondary filter when the whole WRS system is working. Also the mill needs to know what is the Pascal drop from end to end from the main header starting to the tail end of header, tail end of branch headers, when all the cards are lined up for the WRS. This data is to be maintained by the mill since WRS commissioning.
For this system approach, the commissioning report is the back reference for all the above records. If the same is not done till date, please initiate today, this exercise from your end, repeat the same with the OEM at premises to confirm the healthy workings of WRS. All the above readings are to be taken when air flow is normally running only. Pascal measurement in a less/no air flow area in the ducts/system will give erroneous measurements.
Every year once we have to remove the main & sub ducts from the top, lower the same to ground. Inspect for any leaks thro flanges, duct chokes and leaks thro corrosion etc. Either in design or even after late realisation, please keep the ducts as short and straight as possible.
Allow no T type joints, but ensure the air flow is not turbulent but laminar only at any X section of duct. If the holes are not put in the duct, please use drilling machine to make a hole in duct at a point in a straight and top of plane and where fluff accumulation will not occur later. Don’t’ use spindle as poker to put hole in duct, as this leads to fluff collection inside around the duct hole.
What is the low cost energy saving measure?
To reduce the belt transmission losses now: Firstly change the Vee belts in WRS fans to Raw cogged belts. Measure with the motor and blower Tacho to confirm how much the load RPM is lost in the old V belts and now how much RPM regained after the cogged belt replacement? When you plan for pulley re-sizing, plan this activity simultaneously, to maintain the Pascal requirements. Motor belt transmission losses to correct now. Look for the motor losses now: Check the motor is loaded at the efficient band of say, 60 to 80 per cent loading. If not, take steps to correct the same now. Lubrication of motor and fan housing bearings with the Polyurea-thickened-Lithium Mineral oil grease will reduce the friction losses in motor.
This can be confirmed by using thermal imager before and after the exercise. The easy location where instantly we can measure the No-load KW of the motor in a textile mill is at the WRS motor only. So periodically monitor the same for motor loss. In any routine thermal imaging survey, WRS motor and motor alignment invariably shows the Hot spot. Please check and correct the same today as hot spot is a symptom of energy loss in bearing, alignment, wrong mountings, etc.
Inspect backward curved centrifugal blower working: Routinely remove the fluff deposits in the fan blades and in housing. Confirm with the OEM what can be done to the existing blower and the WRS system to reduce energy. Many mills have shortened, expanded the delivery duct from blower as the same was obstructing the blower rated CFM to be exhausted out, thus allowing free exhaust flow.
Look for primary and secondary filter pressure drops: What is the rated Pascal pressure drop, minimum, maximum and optimized pressure drop across the filters recommended by the OEM? What are the other types of filter suiting to the mill operating conditions to achieve energy savings without polluting environment?
The mill & vendor have to decide the periodicity of cleaning/replacing the filter, what will be the Pascal pressure drop before and after cleaning the same. Also what is the optimum period to change the filter so that the energy loss can be reduced by increasing the frequency of cleaning/swapping/replacing of filters?
Routine condition monitoring of Pascal: From blower to card in stages will yield quick instant results of energy loss in each area and the same can be rectified in few days. Pulley re-sizing needs to be done today to match the Pascal drop from end to end is less than the acceptable band.
Now the pressure band is very vast varying from 300 to 600 Pascal. Generating a higher Pascal suction at blower end and the damper control near the cards to regulate say from 900 to 700 Pascal or 1000 to 800 Pascal is inefficient mode of control.
Instead of that, keep the damper fully open in each card (with minor adjustments) so as to generate less Pascal at blower end. Many mills target this area routinely and achieve instant energy savings without compromising the carding, blow room etc Pascal requirements. Let the mill make use of Pascal pressure switch inside the card to give at least visual alarm for less than 800 Pascal setting and that it need not trip the machine. As such, this switch is bypassed in many mills now.
What is high cost measure to achieve energy savings?
Nowadays, the textile mill adds a VFD to any system like AC plant, compressor, Pneumafil suction, Autoconer suction etc to achieve energy savings in dynamically varying loads. Now the mill has to accept that WRS Pascal is a dynamically varying but slow variable.
Here too, we can plan for VFD to achieve more energy savings in the system as the day to day Pascal variations give scope for more power saving thro VFD. Practically VFD retrofit to WRS is the most efficient & power saving approach to operate the WRS instead of the inefficient damper controls now.
How OEM can help the industry to reduce energy?
But in parallel, to discuss with the WRS OEM to achieve improve upon the fan & system efficiency, reduced energy consumption, and later plan to swap the existing system to energy efficient version. Ultimately the KW per 1,000 CMH in the optimum Pascal range (this Pascal requirement varies from mill to mill) is the deciding factor to replace from old to latest versions. The OEM can optimise the speed and fan curves of blower for giving maximum suction flow at the mill’s optimised pressure requirements. Also, see to it that the latest version is fitted with IE 3 version inverter duty energy efficient motor.
Thrust to target the energy reduction: Of all the industry segments, the textile spinning mill only plans for the low-cost energy solutions as they are economical initially. They go for high cost investments to increase/improve the production. But they don’t prioritise energy related investments to reduce energy consumption as well improve the energy efficiency in utility.
The First Year Payback on the investment will indicate how much the mill will save in a big way with high cost investments in utility. They must keep in mind that high-cost solutions yield more energy savings in utility than the low cost instantly retrofit-able solutions. We must weigh the pros and cons of the ECON measure to reduce energy loss in any system and give priority to high cost, higher savings permanent solutions. But obviously we must also remember that energy savings is possible in a healthy suction process with excess inputs, but not in a starved suction process having design flaws, due to utility selection, duct sizing and say more cards now than the planned cards before, undersized filters, etc. So after correcting this, then right sizing and loading is tried to achieve energy savings now. Removal of system defects automatically yields savings.
Ashok Sethuraman is a BEE Accredited Energy Auditor from Coimbatore. He can be contacted at: ashok@energymeasuretosave.com