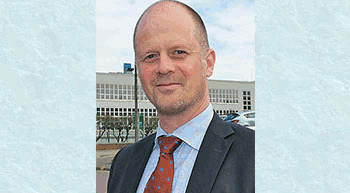
We see big potential for Spray Applicator in Asia
US-based Baldwin Technology Company Inc is one of the leading international manufacturers and full service suppliers of process automation equipment and related consumables for the print, film, corrugated, textile and paper industries.
US-based Baldwin Technology Company Inc is one of the leading international manufacturers and full service suppliers of process automation equipment and related consumables for the print, film, corrugated, textile and paper industries. The company´s Spray Applicator has been researched and developed over a period of more than two years. The base technology has been proven for more than 30 years in the offset printing industry with more than 30,000 applicators installed across the world. The high demands on reliability and service from the newspaper printing industry have been inherited down to the genes of the textile finishing version of the product. The high frequency valves, precision nozzles and high speed controls are the heart and brain of the system and the key to the even and controlled application. The modular design and engineered functions are the backbone of the system and are vital for the flexibility and reliability.
Baldwin exhibited its Spray Applicator at ITMA Milano along with IR dryer, and both these products attracted a steady stream of interested customers during the exhibition. The company also plans to display Spray Applicator at the upcoming ITMA Asia event in Shanghai. Per Stenflo, VP ´ Product Line Spray, Baldwin, in an exclusive tete-a-tete with the ITJ team shares his views.
What are the major products of your company for the textile industry? What are their applications and USPs?
Baldwin has several products for the textile industry.
Our Spray Applicator is ideal for applying low viscosity finishing chemistry to the textile. Typically this would be water/solid repellents, fabric softeners, flame retardants or simply water for preparation or remoistening. With our Spray Applicator and supply solutions, the process of changing jobs is done in a fraction of the time that is normally required today. The process is fully automated and within a few minutes you´re up and running. There is not only the time saved there is also a substantial saving on chemistry. In a traditional process there is often 200-300 litres chemistry waste at job change. With our solution the waste is minimised to a few litres. Spray systems are often associated with large amounts of overspray and difficulties of keeping nozzles or discs clean as well as spreading potentially dangerous aerosols in the work environment. In the Baldwin Spray Applicator, these issues have been resolved. The system is compact and easy to retrofit on existing lines.
Baldwin also offers advanced filtration systems suitable for the textile industry. There are various filter technologies depending on requirements. Everything from filter mat-based systems to highly sophisticated crossflow filtration.
Baldwin has a division completely devoted to UV and IR drying and curing. We are in the forefront of technology when it comes to LED UV systems.
Which are your major markets globally?
Until now we have mainly focused on the European and North American markets. With the fantastic response we have gotten on these markets and some recent success where the benefits of our systems have been proven we are now ready to address the global textile market.
The success at Vagotex in Italy has really boosted the interest in our products. The finishing industry in Italy has the character of a community where word travels fast. The fantastic savings that we have been able to show at Vagotex has opened many eyes and our local sales is very busy with inquiries. In this application, we apply a water-resistant coating on fabrics for sportswear. Not least on the laminating line the solution has offered the possibility to reduce the number of process steps and freeing up a lot of production capacity.
In the US, we are working with a large brand with manufacturing sites around the world. The focus is mainly to apply fabric softeners. They have previous experience of using spray but have had problems with dripping, spreading aerosols in the working environment and uneven distribution. These problems are all avoided with our enclosed Spray Applicator. We apply just the right amount of chemistry in a very even layer varying speeds.
What were the products showcased at ITMA Milano? How was the response, especially from Asian countries?
At ITMA in Milano, we exhibited our Spray Applicator and IR dryer. Both products attracted a steady stream of interested customers.
Among the visitors in our booth there were many from Asia. These customers represented both local companies and larger international brands with manufacturing plants in Asia.
Now that you plan to participate at ITMA Asia, what are your strategies and products to be showcased?
At ITMA Asia, our focus will primarily be on our newly upgraded Spray Applicator. We see a huge potential for this product in Asia. Since many years we have an office in Shanghai that has focused on the local print market. Now they will be involved to drive our activities in China and Southeast Asia.
In India, you already have some presence in other than textile products, I think. What are your specific plans to enter the Indian market for textile products?
We are in contact with several larger textile producers in India. Until now these contacts have been maintained from Europe.
With the introduction of our textile industry products in Asia, our New Delhi production facility will become increasingly involved in both sales and support of these products.
Are there any plans to increase your presence in Asian markets? And also any plans to enlarge your portfolio for the textile industry. If any give details.
There are currently no plans to enlarge our presence in Asia. We are well positioned both for sales and manufacturing in the region.
We are an innovating company and invest heavily in R&D. Our target is to change the textile finishing industry to become more environmentally sustainable and help our customers to increase productivity and reduce cost for finishing chemistry. To support this ambition, there will be new products and solutions launched in a steady pace.
Per Stenflo can be contacted at:
Email: per.stenflo@baldwintech.com | Tel: +46 709769596
Baldwin´s Spray Applicator for textile finishing at Vagotex
Baldwin´s Spray Applicator for textile finishing is now in full production at Vagotex, a leading Italian supplier of finished textiles, primarily for sports collections, located in Verona, northern Italy. Following a smooth installation, the system has delivered more than the anticipated benefits, particularly on laminated products. The new process has improved productivity significantly, eliminating one full process step. Also on the traditional water repellent finishing, the system has improved productivity and reduced waste of chemistry. The challenge to change from C8 to C6 & C4 chemistry has been made a lot smoother thanks to the implementation of the Baldwin Spray Applicator. This is much due to the automatic and quick change between chemistry with minimum waste.
Elisabetta Gaspari, General Manager, Vagotex, said, ´We have truly benefitted from the installation of the Baldwin Spray Applicator and made substantial savings on quality cost and increased productivity. On the laminated products we have been able to free up to 50 per cent of the time in the stenter line, which has increased production time and eliminated a bottle neck in our process. For cost and environmental reasons, we are also very happy about the savings on chemistry that the flexibility of the system has provided. Today we change chemistry in 2-5 minutes, a process that before would take 30 minutes.´
Per Stenflo said, ´We are very grateful to Gaspari and Vagotex for their courage to be a pioneer in the textile finishing industry. They obviously saw the potential benefits that our system could bring to them and were prepared to take the risk to invest in new technology. To us, this is a true success story where our newly launched system has delivered benefits beyond our expectations to our valued customer. This is encouraging and gives new energy to pursue our goal to change the textile finishing business to become smarter and greener.´