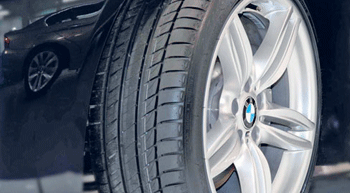
´Green´ tyre cord thanks to EvoQuench
Oerlikon Barmag is one of two companies worldwide that deliver machine solutions for the production of HMLS yarn. The material is extremely tear resistant, but elastic and temperature as well as dimensionally stable. It is predominantly used in high-speed tyres, which´as a result of the high speeds achieved´are subjected to particularly high loads.
Oerlikon Barmag is one of two companies worldwide that deliver machine solutions for the production of HMLS yarn. The material is extremely tear resistant, but elastic and temperature as well as dimensionally stable. It is predominantly used in high-speed tyres, which´as a result of the high speeds achieved´are subjected to particularly high loads. Here, strong polyestre tyre cord has almost completely replaced viscose fibre rayon for ecological reasons. The decisive benefit of HMLS yarns compared to alternative polyester yarns is the extreme dimensional stability of the high-performance yarn.
As a result of contact with the road, tyres are subjected to a constant friction, which heats up the tyres and consequently increases the internal air pressure. Therefore, the higher the speed, the higher the tyre temperature and the pressure within the tyre. And this is precisely where high-modulus polyestre comes into its own: reinforcing tires with dimensionally-stable HMLS also permits high speeds with a high degree of safety. In other words, tyres made from HMLS yarn remain dimensionally stable even under loads and at high temperatures.
Process-technology challenge
The HMLS yarn acquires its unique properties in the spinning process. High speeds in the production process guarantee a stable arrangement of the molecules within the polymer, which forms the actual filament. The internal structure of the molecule chain is in turn decisive for the dimensional stability of the subsequent yarn.
Manufacturing this challenging material in an economical manner therefore requires stable process technology and high-quality components. These determine the requirements for the spinning plant, the godets and the winders. The higher the spinning and winding speeds, the more sensitively the filaments react to even the smallest irregularities in the polymer melt, which can then quickly result in breaks in the filament. As in the case of all filament yarns, each yarn break impacts on the quality and the sale price of the yarn packages. Here, the solution lies in designing the spinning plant components in a way that balances out the unavoidable contamination in the melt. Oerlikon Barmag HMLS systems therefore now work with the EvoQuench quenching system, which has already proven itself in the textile processes. Filament bundles with up to 600 individual filaments are evenly spun, cooled and spin-finished and in this way allow homogenous threads of between 1,000 and 2,000 denier to be manufactured. The thick titers are gently and evenly drawn on up to six godet duos. The?compared to conventional industrial yarns?more intensive and longer yarn heat-treatment time guarantees the required low shrinkage values. Subsequently, the yarn is wound using latest-generation ACW high-speed winders at speeds of up to 7,000 m per minute.
Green technology
Using the EvoQuench system for manufacturing industrial yarn is also setting new standards in terms of energy savings. As in the case of textile processes, the e-save certified EvoQuench system dramatically lowers the energy consumption. Depending on the titer and the dpf, the consumption of the compressed air so decisive for the energy consumption in quenching is reduced by around 80 per cent compared to a cross-flow quenching system. For a standard system size with four positions and an assumed electricity price of US$0.15 per kilowatt hour, the system operator saves around US$ 40,000 per years in terms of energy costs by just using the EvoQuench alone.
Correspondingly, carbon footprint calculations for a four-position polyester HMLS system with EvoQuench quenching have revealed annual savings of just under 152 tonnes of CO2e compared to the alternative with cross-flow quenching. And a pleasant side effect: due to the considerably lower air consumption, the air-conditioning syst