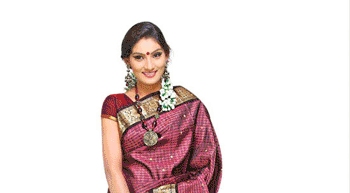
Weaving success via clusters
Dr Anita Desai reviews the cluster concept, from its inception to the main contemporary regional science with focus on the tangible elements of sari weaving clusters irrespective of the popularity. The Indian textile industry is as old as the word textile itself. It works on an independent basis starting from the procurement of raw material to the final production of actual textiles.
Dr Anita Desai reviews the cluster concept, from its inception to the main contemporary regional science with focus on the tangible elements of sari weaving clusters irrespective of the popularity.
The Indian textile industry is as old as the word textile itself. It works on an independent basis starting from the procurement of raw material to the final production of actual textiles.
Clusters are an alternative organisation of the value chain, promoting both competition and cooperation; without competition a cluster will fail. Clusters highlight that not only what happens inside enterprises matters, but also what happens outside them; the business environment is crucial, and its features are determinant elements of competition sophistication. High quality physical infrastructure will maximise the efficiency of logistics, well-educated personnel will positively impact the productivity of services and a court system that resolves disputes fairly and rapidly will facilitate operations. A cluster allows each member firm to benefit as if it had a greater scale.
Indian textile industry is highly fragmented as about 95 per cent of the industry is unorganised. The predominance of micro, small and medium enterprises (MSMEs) are under pressure to modernise, expand and cut cost as there is increasing internal competition as well as from outside which is forcing individual units to look for economies of scale. A large number of units therefore are coming together either in the form of strategic alliances or become a part of the cluster. There is a global trend of buyers on cutting down on the number of suppliers and to prefer sourcing their entire requirements from two to three vendors to ensure consistent quality and sustainable quantities which the industry is finding it difficult to fulfill.
Under these circumstances, clusters have come to play. The Government of India took cluster development to the next level by way of setting up Greenfield Cluster Parks wherein it launched and implemented various cluster based schemes like Mega Cluster Scheme and Scheme for Integrated Textile Parks (SITP) for setting up of Greenfield textile parks being implemented by the Ministry of Textiles, Scheme for Mega Food Parks by Ministry of Food Processing Industries etc. Typically a Greenfield Textile Cluster would have the manufacturing and related service units from cotton spinning to garment manufacturing comprising of many independent units working in close co-ordination & as a forward or backward integration to each other. With investment on new textile machinery, generally the projects need longer time for payback.
Indian Clusters and Cluster Development Policy
This section about Indian clusters and cluster development policy begins with macro-economic and policy considerations, to continue with an introduction to India SMEs, which represent the core of manufacturing employment and essentially operate in clusters. The important fabric manufacturing cultures are Kanchipuram, Arani, Kumbakonam, Chanderi, Maheshwari, Salem and Karur, Bangalore and Mysore, Illkal, Guledgudda, Kota, Banaras, Sulakuchi,
History
Over the ages, India has conjured up different images at different times, but one constant through the centuries has been its textiles and one region, which has always been in the picture in this regard has been Tamil Nadu. Early records speak of fine muslin and silks and hand painted calicos that the Greeks came to buy from Tamizhagam, the home of Tamil. Uraiyur, Karur and Madurai, situated close to the cotton fields, were major centres of weaving. They still are the most prominent centers for the exquisite weaving products.
The raw materials used in the silk weaving centres are not indigenous to Tamil Nadu for ?Zari? comes all the way from Surat while neighbouring Karnataka supplies the silk. Indeed Karnataka meets the silk needs of not just Kanchipuram but the whole of India.
Tamil Nadu arts
From the coarse Chettinad saris, to the saris of Salem, Rasipuram and Coimbatore, to the fine gold bordered muslins of Madurai or its more recent medium weight reasonable saris that are printed or resist-dyed and are popularly referred to as the ?Madurai Sungudi?, the weaves of Tamil Nadu offer wide choice.
Kanchipuram silks
Kanchipuram is famous for its silks. As the vast range of cottons are not withstanding, these textiles are overshadowed by their glamorous counterpart, the silks and more specifically those from Kanchipuram. Research suggests that silk was a new entrant into Kanchipuram, for till a century and a half back, Kanchipuram was primarily a cotton-weaving centre. It was the Thanjavur -Kumbakonam belt and ?Arani? along with Salem that produced the ?Pattu Pudavai? today the finer, better-woven and more expensive silk saris for Kanchipuram. Kanchipuram silk saris are woven in two parts. The Pallu-and-border are woven as one unit and attached to the body of the sari, which is woven separately. The motifs used are derived from traditional temple architectural forms. Over the years inputs from weavers, designers and the weaver service centres have led to an increasing variety of designs and colours and created a special market niche for the Kanchipuram silks.
Thanjavur and Kumbakonam silks
Thanjavur is another silk center, which specialises in the use of Zari and brocade work. These saris are heavy and opulent. Thanjavur and Kumbakonam create saris similar to Kanchipuram but the Mundhi or end pieces are finished differently. Using a technique called ?Porai? the weavers pull the warp threads, at the join of two colours, into loops at the back and then cut it close.
Arani saris
Arani is located in the district of Thiruvannamalai in the state of Tamil Nadu. Arani is one of the most important silk centers of Tamil Nadu. Arani handlooms are well known for the durability of the colours used in the yarn. The mixture of colour gives the durability.
To create designs in the saris, first the design is been made in a computer and then loaded into the Jacquard in the loom. The specialty of Arani saris is that a sari is made with two different bodies on each side and two different pallus, which can be used as two different saris. Saris are designed so shrewdly that in one side of the body half will be in one colour and the other half with another colour and at the two ends different pallus and in the other side the entire body will be of one colour with one pallu.
Chanderi saris
There have been changes in the methodologies, equipments and even the compositions of yarns in past. The heritage is attached with the skills of weaving high quality fabric products here. The weavers are actually the symbol of the heritage, as they have been the ones, who produced the kinds of fabrics that received appreciation even from the royals. Originally, Chanderi was always woven using hand spun cotton warps and wefts. It was spun as fine as 300 counts, and was as prized among cotton fabrics as the famed muslins of Dhaka. However, the Industrial Revolution sounded the first death knell on this beautiful textile. The British imported cheaper 120 to 200 count cotton from Manchester, which greatly eroded the market for the more expensive Chanderi cloth. In the 1930s, Chanderi weavers discovered Japanese silk.
Karur fabrics
Karur is the administrative headquarters of Karur District, Tamil Nadu. Located on the banks of River Amaravathi, it has been ruled, at different times, by the Chera, Vijayanagar Empire, Madurai Nayaks, Hyder Ali, Carnatic kingdom, and the British.
It is located at a distance of 370 kms southwest of the state capital Chennai. It is well known for hand loom, power loom textile products, paper and bus body works industries.
Maheshwari saris
The beautiful Maheshwari saris are among the most popular saris produced in India. These saris are in demand not only in India, but also in international markets. This article aims at studying the origin of the Maheshwari sari, the motifs and colours used and the other special features of the sari.
The detailing on the walls of the Fort of Maheshwar inspired the designs in the Maheshwari saris. The popular designs used in these saris, which were inspired from the designs on the fort walls are the ?Chatai? pattern that is the ?Mat? pattern, the ?Chameli ka phool? pattern that is the ?Chameli flower? pattern, the ?Eent? pattern that is the ?Brick? pattern as well as the ?Heera? pattern that is the ?Diamond? pattern. These designs are found on Maheshwari saris today.
Maheshwari saris were initially made only in dark shades like red, maroon, black, purple and green. Today, these saris are also being made in lighter shades and gold and silver threads are being made use of.
Bagru prints
Bagru, a rural Indian village in Rajasthan, is situated about 30 km east of Jaipur city. Its traditional process of handblock printing on textiles, with rich natural colours has been known for many centuries.
Bagru Chhipas came from Sawai Madhopur, Alwar, Jhunjhunu, and Sikar districts of Rajasthan to settle in Bagru and make it their home. They are known for their unique designs of luxuriant trellises in sophisticated natural colours.
Varanasi / Banaras saris
Varanasi (Banaras) sari is silk and gold-wrapped silk yarn with supplementary weft brocade (zari). Banarasi saris are saris made in Varanasi, a city that is also called Banaras. The saris are among the finest saris in India and are known for their gold and silver brocade or zari, fine silk and opulent embroidery. The saris are made of finely woven silk and are decorated with intricate design, and, because of these engravings, are relatively heavy.
Their special characteristics are Mughal inspired designs such as intricate intertwining floral and foliate motifs, kalga and bel, a string of upright leaves called jhallar at the outer, edge of border is a characteristic of these saris. Other features are gold work, compact weaving, figures with small details, metallic visual effects, pallus, jal (a net like pattern), and mina work.
Sambalpuri Sari
Sambalpuri saris are a traditional hand-woven ikat or sari or sari (locally called shadhi) wherein the warp and the weft are tie-dyed before weaving. It is produced in the Bargarh, Sonepur, Sambalpur, Balangir district, Boudh District of Odisha. The sari is a traditional female garment in the Indian Subcontinent consisting of a strip of unstitched cloth ranging from four to nine metres in length that is draped over the body in various styles.
Guledgudda fabrics
Guledgudda Khana is a fabric hand woven using pure cotton thread and silk yarn by traditional weavers of Guledgudda and surrounding villages. The Guledgudda Khana fabric is a product of intricate work and design, invented and preserved by weavers of Guledgudda and surrounding villages.
Kai Krafts not only works for empowerment of the women of North Karnataka who earn their livelihood through Kasuti, but also works towards the livelihoods of various weavers of Guledgudda.
Ilkal saris
Ilkal was an ancient weaving centre where the weaving seems to have started in the 8th century AD. The growth of these saris is attributed to the patronage provided by the local chieftains in and around the town of Bellary. The availability of local raw materials helped in the growth of this sari. About 20000 people in the town of Ilkal are engaged in sari weaving.
The distinctive feature of Ilkal saris is the use of a form of embroidery called as Kasuti. The designs used in Kasuti reflect traditional patters like palanquins, elephants and lotuses, which are embroidered onto Ilkal saris. These saris are usually 9 yards in length and the pallu of the Ilkal sari (the part worn over the shoulder) carries designs of temple towers. This pallu is usually made of red silk with white patterns. The end region of the pallu is made up of patterns of different shapes like hanige (comb), koti kammli (fort ramparts), toputenne (jowar) and rampa (mountain range).
The border of the sari is very broad (4 to 6 inches) and red or maroon in colour and is made of different designs with ochre patterns.
Kota saris / Kota Doria
Kota is one of many types of sari garments made at Kota, Rajasthan and Muhammadabad Gohna, Mau in Uttar Pradesh and its nearby area. Saris are made of pure cotton and silk and have square like patterns known as khats on them. The chequered weave of a Kota sari is very popular. They are very fine weaves and weigh very less.
Originally, such saris were called Masuria because they were woven in Mysore. The weavers were subsequently brought to Kaithoon, a small town in Kota by Rao Kishore Singh, a general in the Mughal army. The weavers were brought to Kota in the late 17th and early 18th century and the saris came to be known as ?Kota-Masuria?.
Kota Doria is woven on a traditional pit loom in such a fashion that it produces square checks pattern on the fabric. The delicately wrought checks are locally known as khats. They smear onion juice and rice paste with a lot of care into the yarn making the yarn so strong that no additional finishing is needed.
Panipat saris
History, craft and cottage industries come together at this important junction between the Punjab and the Gangetic Plains. About 100 km from Delhi, in the state of Haryana, is the sprawling industrial city of Panipat, a luminary of the handloom industry in India. Long before one enters the main city, billboards proclaim the presence of the weaving units. Further, up, the main road is flanked by a string of showrooms with local handloom products on display. Panipat is famous for ?panja? durrie a kind of a floor covering, which is in great demand in India and abroad.
Pochampally saris / Pochampalli Ikat
Pochampally saris or Pochampalli Ikat is a sari made in Bhoodan Pochampall, Nalgonda district, Telangana. They are popular for their traditional geometric patterns in Ikat style of dyeing. The intricate geometric design find their way into the hands of skillful weavers and make it to the market as beautiful saris and dress material. The weavers silk and cotton are princely priced but the fair share is not shared with weavers, pushing them to poverty.
Shantipur saris
The bustling town of Shantipur in Nadia district of West Bengal, India, is just 90 km north of the metropolis of Kolkata. It has recently been declared a city. Neighbouring Fulia is often uttered in the same breath with Shantipur, their contrasting backgrounds notwithstanding. Together they are perhaps the most renowned Bengal handloom sari-weaving centres in Bengal. Shantipur and Fulia saris are household names across India. The Shantipur-Fulia region has over 125,000 handlooms, churning out Shantipuri, Tangail, and Jamdani handloom saris in a variety of yarns like cotton, tussar and silk. Dhotis, dress materials, stoles and scarves are also woven.
Sualkuchi silk
Sualkuchi is a multi-caste town under Guwahati Sub-division of Kamrup district of Assam, situated on the North bank of the mighty Brahmaputra at a distance of 30 km West of Guwahati. The town is linked with Guwahati by P.W.D roads and with Palashbari on the South bank by motor boat and country boat. As per 2001 Census, the total population of Sualkuchi was 21252 with 4023 households. As per the Census report of 2001, the workforce participation rate in the town was 37.93 per cent of the total populations, of which only 0.53 per cent were cultivators, 1.2 per cent were agricultural labours, 56.37 per cent were engaged in household industries and the remaining 41.90 per cent were engaged in other activities.
Bangalore and Mysore textiles
Karnataka has drafted a textile policy that expects to attract investments worth Rs10,000 crore and create half a million jobs in five years by offering sops to the industry. The policy is now awaiting approval of the new government. The draft policy primarily aims at two aspects: generation of employment in the rural interiors and invite new investments in the sector. The textile and readymade garment industry?the second largest employer in the state after information technology is worth nearly Rs. 5,000 crore excluding exports, and employs 500,000 workers in and around Bangalore, according to government data.
Acknowledgment
The author expresses her sincere gratitude to Prof. RSS Rao, Principal, Vogue Institute of Fashion Technology, Bangalore for his support.
Reference
- Knorringa, P. (1999), ?Agra: an Old Cluster Facing the New Competition?, in World Development, 27 (9):1587-1604
- Iconic Sari weaving clusters in India UNESCO, Culture World Heritage Centre, The List, Global Strategy, April 2014.
- Exposure visit cum study tour to textile cluster in India, March 7, 2014, Cotton Technical Assistance Programme for Africa, Govt. of India.
- Das, K., Ashgate, Hants,Conditions?, in Indian Industrial Clusters, ed. pp.21-37
- GOVERNMENT OF INDIA (1997), Report of the Expert Committee on Small Enterprises (Chairman: Abid Hussain), Ministry of Industry, New Delhi.
- SARKAR, T. (2005), ?Handicrafts and the ?Cluster Development Approach?: The Hand Block Printed Textiles
- Cluster of Jaipur?, in Indian Industrial Clusters, ed. Das, K., Ashgate, Hants, pp. 171-19
- Informal economy Centrestage, eds. R. Jhabvala, M. R. Sudarshan, J. Unni, Sage Publications India Pvt Ltd, New Delhi, pp. 39-61
- Mokashi, Ravi; Kire, Menuolhoulie. ?Silk Weaving Tradition of Sualkuchi, Assam?. D?source. Retrieved 10 January 2013.
The author is Senior Associate Professor & Head of Department – Fashion and Apparel Technology, Vogue Institute of Fashion Technology, Bangalore. She can be contacted at: Email: anitaajaydesai@gmail.com